Method for decomposing ammonium chloride to prepare organic base hydrochloride and cyclohexanone-oxime synchronously
A technology of organic base hydrochloride and cyclohexanone oxime, applied in the field of chemical technology, can solve the problems of harsh reaction conditions, expensive displacers, unfavorable for industrialization and the like, and achieve the effect of convenient transportation
- Summary
- Abstract
- Description
- Claims
- Application Information
AI Technical Summary
Problems solved by technology
Method used
Image
Examples
Embodiment 1
[0036] Put 3.0g of TS-1 titanium silicon catalyst and 8.0g (150mmol) of ammonium chloride solid into the reactor, then add water 20mL (1111.1mmol), cyclohexylamine 17.2mL (150mmol), cyclohexanone 6.4mL (62mmol ), stirred and warmed up to 70°C, then added 20mL of hydrogen peroxide (H 2 o 2 196mmol), the hydrogen peroxide is added dropwise and injected by a micro-injection pump, 20mL / h (dropping is completed in 1 hour), and the normal pressure reaction is started for 1.5h at the same time; the catalyst and the reaction solution are centrifuged, and the catalyst obtained is washed with alcohol and water, and the 80 ℃ vacuum drying for 10 hours, 500 ℃ muffle furnace roasting for 4 hours, and set aside; the reaction solution obtained by centrifugation was extracted and separated by toluene to obtain an organic phase, and the organic phase was analyzed by gas chromatography, and the yield of the product cyclohexanone oxime was quantitatively calculated to be 86.1 %; The above organ...
Embodiment 2~7
[0038] The operation steps and reaction conditions are the same as in Example 1, except that cyclohexylamine is replaced by other organic bases, which are respectively dimethylamine, trimethylamine, diethylamine, triethylamine, ethylenediamine, and ethanolamine. is 150mmol. The organic phase was analyzed by gas chromatography, the yield of the product cyclohexanone oxime and the quality of organic base hydrochloride were quantitatively calculated, and various organic base hydrochloride products were characterized by infrared. The experimental results are shown in Table 1, and the characterization results are attached Figure 2-7 .
[0039] The impact of different organic bases in table 1 on the reaction of synthetic cyclohexanone oxime
[0040]
[0041]
Embodiment 8
[0043] The same operation steps and reaction conditions as in Example 1, except that in the oximation reaction, the addition of cyclohexylamine was changed to 7.6mL, and the amount of cyclohexylamine was 66mmol. After the reaction was over, the catalyst and the reaction solution were centrifuged. The organic phase is obtained through toluene extraction and separation, and the organic phase composition is analyzed by gas chromatography; the raffinate aqueous phase is distilled under reduced pressure, washed and dried to obtain the white solid cyclohexylamine hydrochloride crude product 12.2g (which contains 4.1g ammonium chloride ). The experimental results are shown in Table 2.
PUM
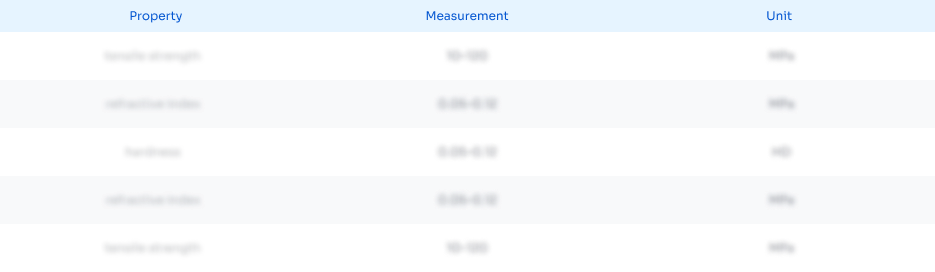
Abstract
Description
Claims
Application Information

- R&D
- Intellectual Property
- Life Sciences
- Materials
- Tech Scout
- Unparalleled Data Quality
- Higher Quality Content
- 60% Fewer Hallucinations
Browse by: Latest US Patents, China's latest patents, Technical Efficacy Thesaurus, Application Domain, Technology Topic, Popular Technical Reports.
© 2025 PatSnap. All rights reserved.Legal|Privacy policy|Modern Slavery Act Transparency Statement|Sitemap|About US| Contact US: help@patsnap.com