A Zinc Alloy Zipper Chain Tooth
A zinc alloy and sprocket technology, applied in the field of metallurgical electroplating, can solve the problems of poor adhesion between the nickel plating layer and the substrate, the application range is not very wide, and the large-scale application is limited, and the production cost is low, easy to control, and less components. Effect
- Summary
- Abstract
- Description
- Claims
- Application Information
AI Technical Summary
Problems solved by technology
Method used
Examples
Embodiment 1
[0020] A zinc alloy zipper sprocket, the sprocket is a European tooth type, including a meshing end and a mounting end; the zipper sprocket is made of 5# zinc alloy die-casting, and the two ends are formed by 5# zinc alloy one-time die-casting Integral structure, sprocket length 10mm, width 8mm, thickness 3.5mm, the surface of the sprocket has a coating; wherein, the coating is formed by the following process:
[0021] (1) Pre-plating treatment: including surface degreasing and degreasing, pickling and rust removal, and activation treatment process to improve the bonding force of the coating;
[0022] (2) Cyanide-free pre-plating of copper: the composition of the plating solution is copper pyrophosphate 100g / L; sodium pyrophosphate 50g / L, trisodium citrate 280g / L, potassium sodium tartrate 30g / L, HEDP30g / L, ethylenediamine 280g / L; ammonium bifluoride 2g / L; sodium fluoride 3g / L, lithium fluoride 6g / L; ammonia water to adjust the pH value to 9.5, the electroplating process is ca...
Embodiment 2
[0026] A zinc alloy zipper sprocket, the sprocket is a European tooth type, including a meshing end and a mounting end; the zipper sprocket is made of 5# zinc alloy die-casting, and the two ends are formed by one-time die-casting of 5# zinc alloy Integral structure, sprocket length 10mm, width 8mm, thickness 3.5mm, the surface of the sprocket has a coating; wherein, the coating is formed by the following process:
[0027] (1) Pre-plating treatment: including surface degreasing and degreasing, pickling and rust removal, activation treatment process to improve the bonding force of the coating;
[0028] (2) Cyanide-free pre-plating of copper: the composition of the plating solution is copper pyrophosphate 120g / L; sodium pyrophosphate 40g / L, trisodium citrate 300g / L, potassium sodium tartrate 26g / L, HEDP50g / L, ethylenediamine 260g / L; ammonium bifluoride 3g / L; sodium fluoride 2g / L, lithium fluoride 8g / L; ammonia water to adjust the pH value to 8.5, the electroplating process is cat...
Embodiment 3
[0032]A zinc alloy zipper sprocket, the sprocket is a European tooth type, including a meshing end and a mounting end; the zipper sprocket is made of 5# zinc alloy die-casting, and the two ends are formed by one-time die-casting of 5# zinc alloy Integral structure, sprocket length 10mm, width 8rmm, thickness 3.5mm, the surface of the sprocket has a coating; wherein, the coating is formed by the following process:
[0033] (1) Pre-plating treatment: including surface degreasing and degreasing, pickling and rust removal, and activation treatment process to improve the bonding force of the coating;
[0034] (2) Cyanide-free pre-plating of copper: the composition of the plating solution is copper pyrophosphate 110g / L; sodium pyrophosphate 45g / L, trisodium citrate 290g / L, potassium sodium tartrate 28g / L, HEDP40g / L, ethylenediamine 270g / L; ammonium bifluoride 2.5g / L; sodium fluoride 2.5g / L, lithium fluoride 7g / L; ammonia water to adjust the pH value to 9.0, the electroplating proces...
PUM
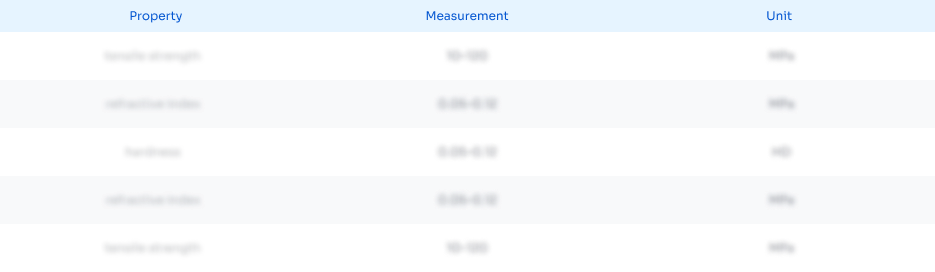
Abstract
Description
Claims
Application Information

- R&D
- Intellectual Property
- Life Sciences
- Materials
- Tech Scout
- Unparalleled Data Quality
- Higher Quality Content
- 60% Fewer Hallucinations
Browse by: Latest US Patents, China's latest patents, Technical Efficacy Thesaurus, Application Domain, Technology Topic, Popular Technical Reports.
© 2025 PatSnap. All rights reserved.Legal|Privacy policy|Modern Slavery Act Transparency Statement|Sitemap|About US| Contact US: help@patsnap.com