A kind of water-based self-emulsifying carbon fiber sizing agent suitable for thermoplastic resin and preparation method thereof
A thermoplastic resin, self-emulsification technology, applied in carbon fiber, fiber treatment, textiles and papermaking, etc., can solve the problems of difficulty in fully exerting the mechanical properties of carbon fiber reinforcement, low interface bonding strength, poor matching, etc., to achieve low cost and high performance The effect of stabilization and improvement of bond strength
- Summary
- Abstract
- Description
- Claims
- Application Information
AI Technical Summary
Problems solved by technology
Method used
Image
Examples
Embodiment 1
[0024] Synthesis of maleic anhydride-dodecene random copolymer (polymer A1): under nitrogen protection conditions, first dissolve 0.12mol maleic anhydride in 100mL xylene and add it to a three-necked reaction flask, stir and heat up to 80°C, then add 0.2mol of dodecene, stirred for a period of time at constant temperature, added an appropriate amount of initiator benzoyl peroxide (BPO), heated to 120 o C. React at constant temperature for 1.5 hours. After the reaction is stopped, it is naturally lowered to room temperature. Part of the xylene is removed by rotary evaporation to obtain a concentrated solution of polymer A1. Multiple precipitation methods are used to remove unreacted monomers and small molecular weight polymers. After vacuum drying Polymer A1 was obtained. The chemical structure of the polymer adopts 1 The structure was confirmed by HNMR and FTIR, and the molecular weight and molecular weight distribution of the polymer were determined by gel chromatography (GP...
Embodiment 2-8
[0028] The synthesis of series maleic anhydride-dodecene random copolymer (polymer A2-polymer A8), its synthetic method is identical with embodiment 1, and the raw material ratio of maleic anhydride and dodecene in each polymkeric substance is listed in in FIG. 1. The results of polymer molecular weight and molecular weight distribution of polymers A1-A8 are listed in Table 1.
[0029] Table 1 Raw material ratio, polymer molecular weight and molecular weight distribution of a series of maleic anhydride-dodecene random copolymers
[0030]
Embodiment 9
[0032] Synthesis of maleic anhydride-dodecene block copolymer (polymer A9): 0.2mol dodecene, 0.02mol maleic anhydride, 60mL xylene and appropriate amount of initiator azobisisobutyronitrile AIBN and RAFT reagent two Thiobenzoic acid (2-ethoxycarbonyl)-2-propyl ester (EPDB) is added in the reaction flask equipped with magnetic stirring, wherein the mol ratio of AIBN and EPDB is 1.0:3.0, nitrogen deoxygenation after 1 hour sealing, warm up to 80 o C carries out the polymerization reaction 8h, and after the reaction finishes, the polymerization solution is poured into precipitation in the cold sherwood oil, repeats the process of dissolving and settling for many times, obtains poly(maleic anhydride-alt-dodecene)-b-polydodecene after filtration block copolymers. Data molecular weight M of polymer A9n 7600g / mol, weight average molecular weight M w 9196g / mol, molecular weight dispersion M w / M n is 1.21.
PUM
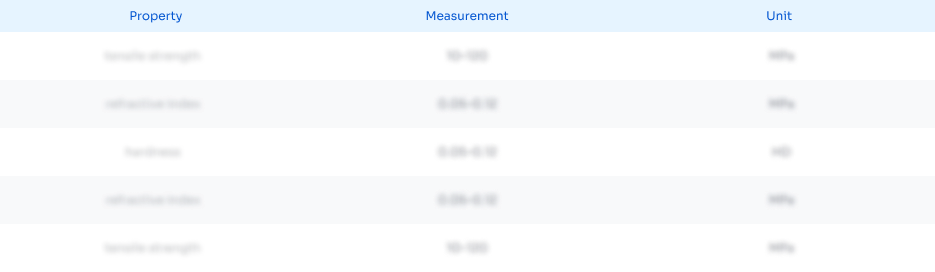
Abstract
Description
Claims
Application Information

- Generate Ideas
- Intellectual Property
- Life Sciences
- Materials
- Tech Scout
- Unparalleled Data Quality
- Higher Quality Content
- 60% Fewer Hallucinations
Browse by: Latest US Patents, China's latest patents, Technical Efficacy Thesaurus, Application Domain, Technology Topic, Popular Technical Reports.
© 2025 PatSnap. All rights reserved.Legal|Privacy policy|Modern Slavery Act Transparency Statement|Sitemap|About US| Contact US: help@patsnap.com