Waterborne epoxy impregnating insulating varnish and preparation method thereof
A technology of impregnating insulation and water-based epoxy, which is applied in the field of paint making, can solve the problems of high curing temperature, low mechanical strength, and lower emulsification temperature, and achieve good storage stability, good dilution stability, and low curing temperature.
- Summary
- Abstract
- Description
- Claims
- Application Information
AI Technical Summary
Problems solved by technology
Method used
Image
Examples
Embodiment 1
[0042] 1) Preparation of epoxy emulsifier
[0043] Add 2 parts of E51, 4 parts of E44 epoxy resin and 44 parts of polyethylene glycol 4000 into the reaction kettle, raise the temperature to 70°C to melt the polyethylene glycol and mix well with the epoxy resin, then drop 0.1 part of boron trifluoride ethyl ether, continue to stir for 0.5h after the dropwise addition, then raise the temperature to 75°C, and continue the reaction at this temperature for about 3h, take a small amount of product dropwise into water, if turbidity occurs, it means that the reaction has not reached the end, continue React until the product is completely dissolved in water and is transparent. After the product reaches the end point, it is diluted with water to form an emulsifier with a solid content of 50%.
[0044] (2) Preparation of polyvinyl alcohol aqueous solution with 10% solid content
[0045] Add 9 parts of polyvinyl alcohol particles PVA17-88 and 1 part of VA17-99 to 90 parts of water at 75...
Embodiment 2
[0049] 1) Preparation of epoxy emulsifier
[0050] Add 5 parts of E44, 3 parts of E20, 35 parts of Polyethylene Glycol 4000, 10 parts of Polyethylene Glycol 6000 into the reaction kettle, heat up to 70°C to melt the Polyethylene Glycol and fully mix it with the epoxy resin, Then add 0.15 parts of boron trifluoride ethyl ether dropwise, continue to stir for 0.5h after the dropwise addition, then raise the temperature to 85°C, and continue the reaction at this temperature for about 2h, take a small amount of product dropwise into water, if turbidity occurs, it means that the reaction has not yet reached At the end point, continue to react until the product is completely dissolved in water and becomes transparent. After the product reached the end point, it was diluted with water to obtain 47% solid emulsifier.
[0051] (2) Preparation of 13% polyvinyl alcohol aqueous solution
[0052] Add 6 parts of PVA24-88, 4 parts of PVA20-88, and 3 parts of PVA17-99 particles into 87 parts...
Embodiment 3
[0056] 1) Preparation of epoxy emulsifier
[0057] Add 5 parts of E44, 3 parts of E20 epoxy resin, 0.5 parts of E12 and 40 parts of polyethylene glycol 4000, 10 parts of polyethylene glycol 6000 into the reaction kettle, heat up to 70 °C to melt polyethylene glycol and mix with Mix the epoxy resin well, then add 0.2 parts of boron trifluoride diethyl ether dropwise, continue to stir for 0.5h after the dropwise addition, then raise the temperature to 90°C, and continue to react at this temperature for about 2h, take a small amount of product dropwise into water , if turbidity appears, it means that the reaction has not reached the end, continue to react until the product is completely dissolved in water and becomes transparent. After the product reached the end point, it was diluted with water to obtain 54% solid emulsifier.
[0058] (2) Preparation of 8% polyvinyl alcohol aqueous solution
[0059] Add 1 part of PVA24-88, 3 parts of PVA20-88, 3 parts of PVA17-88, and 1 part o...
PUM
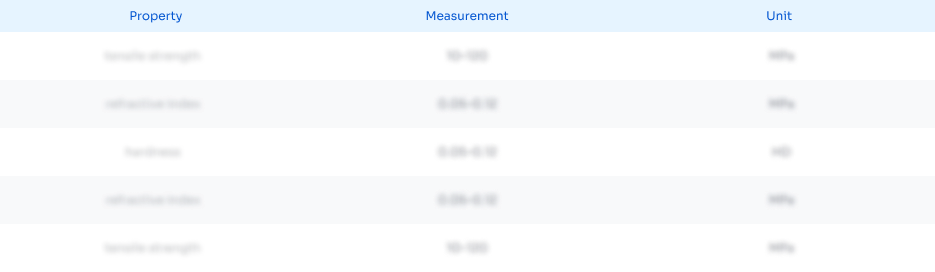
Abstract
Description
Claims
Application Information

- R&D
- Intellectual Property
- Life Sciences
- Materials
- Tech Scout
- Unparalleled Data Quality
- Higher Quality Content
- 60% Fewer Hallucinations
Browse by: Latest US Patents, China's latest patents, Technical Efficacy Thesaurus, Application Domain, Technology Topic, Popular Technical Reports.
© 2025 PatSnap. All rights reserved.Legal|Privacy policy|Modern Slavery Act Transparency Statement|Sitemap|About US| Contact US: help@patsnap.com