Continuous and direct compression molding forming method for thermoplastic plastic thin-wall melt
A thin-walled plastic compression molding technology, applied in the field of plastic molding processing, can solve problems such as low efficiency, limitation of compression molding processing, complex mold manufacturing, etc., and achieve simple production process, easy flow and stretching, and complex equipment and molds Effect
- Summary
- Abstract
- Description
- Claims
- Application Information
AI Technical Summary
Problems solved by technology
Method used
Image
Examples
Embodiment Construction
[0031] Attached below Figure 1-2 and specific examples to further illustrate the present invention, but not as a limitation to the present invention.
[0032] In the product of the present invention, its material is a composite material made of the following components in percentage by weight, thermoplastic 50% polyvinyl chloride resin, wood flour 15%, thermal conductive material 10%, filler 15% and auxiliary agent 10%, wherein Thermoplastics include one or more of polyethylene, polypropylene, polyvinyl chloride, ABS, polystyrene polyester, polycarbonate, nylon, etc. Resin powder with a density of 700. The wood powder is pure wood powder with a coupling treatment of more than 100 meshes. The thermal conductive material includes aluminum powder, iron powder, copper powder and other metal monomers or aluminum oxide, magnesium oxide, silicon nitride, nitrogen, etc. Metal or non-metal chemical compounds such as boron oxide, 400-mesh alumina is used as the heat-conducting materia...
PUM
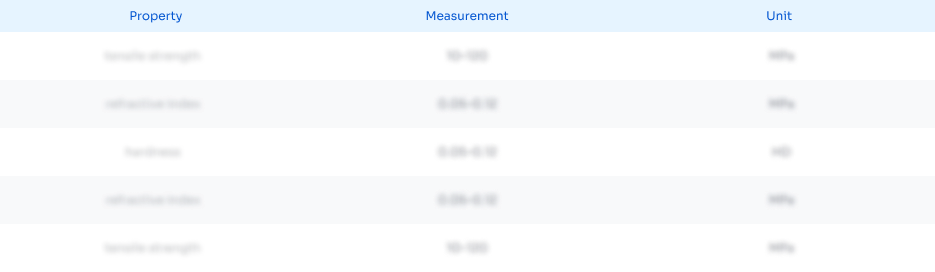
Abstract
Description
Claims
Application Information

- R&D
- Intellectual Property
- Life Sciences
- Materials
- Tech Scout
- Unparalleled Data Quality
- Higher Quality Content
- 60% Fewer Hallucinations
Browse by: Latest US Patents, China's latest patents, Technical Efficacy Thesaurus, Application Domain, Technology Topic, Popular Technical Reports.
© 2025 PatSnap. All rights reserved.Legal|Privacy policy|Modern Slavery Act Transparency Statement|Sitemap|About US| Contact US: help@patsnap.com