Preparation method of ultrafine alpha-Al2O3 powder
A technology of ultra-fine powder and powder, which is applied in the direction of alumina/hydroxide, etc., can solve the problems of low concentration of reaction materials, poor powder dispersibility, wide particle size distribution, etc., to achieve the suppression of particle agglomeration, increase in production, Strengthen the effect of steric hindrance effect
- Summary
- Abstract
- Description
- Claims
- Application Information
AI Technical Summary
Problems solved by technology
Method used
Image
Examples
Embodiment 1
[0039] an α-Al 2 o 3 The preparation method of superfine powder, comprises steps as follows:
[0040] (1) Preparation of Basic Aluminum Ammonium Carbonate Precursor
[0041] 1. Get 13.254kg of ammonium bicarbonate solid particles and 17.764kg of aluminum ammonium sulfate solid particles as raw materials, fully mix the two raw materials, add 6.204kg of water in the reactor as the reaction bottom liquid, and add 163.98g of polyethylene glycol 600, pass The synergistic effect of high-speed mechanical stirring and ultrasonic dispersion will mix the reaction materials evenly, and generate a suspension of the basic ammonium aluminum carbonate precursor after reacting at -20-20°C for 3 hours;
[0042] ② Hydraulically filter the suspension of the obtained ammonium basic aluminum carbonate precursor, wash the filter cake with water and dry it in a vacuum oven at 80°C for 8 hours to obtain the basic ammonium aluminum carbonate precursor powder;
[0043] The XRD figure and the SEM fig...
Embodiment 2
[0050] an α-Al 2 o 3 The preparation method of superfine powder, comprises steps as follows:
[0051] (1) Preparation of basic ammonium aluminum carbonate precursor: as described in Example 1, the difference is 1.: get 13.195kg ammonium bicarbonate solid particles and 17.823kg aluminum ammonium sulfate solid particles as raw materials, and the reaction time is 4h;
[0052] (2) Calcination of basic ammonium aluminum carbonate precursor: as described in Example 1;
[0053] (3) sanding: same as embodiment 1, the difference is that the sanding time is 2h.
Embodiment 3
[0055] an α-Al 2 o 3 The preparation method of superfine powder, comprises steps as follows:
[0056] (1) Preparation of basic aluminum ammonium carbonate precursor: as described in Example 1, the difference is ①: the addition of polyethylene glycol 600 is 21.86g;
[0057] (2) Calcination of basic aluminum ammonium carbonate precursor: put the basic aluminum ammonium carbonate precursor powder in a high-temperature furnace, raise the temperature to 1250°C at a heating rate of 5°C / min, and keep at this temperature for 50min;
[0058] (3) sanding: same as embodiment 1, the difference is that the sanding time is 2h.
PUM
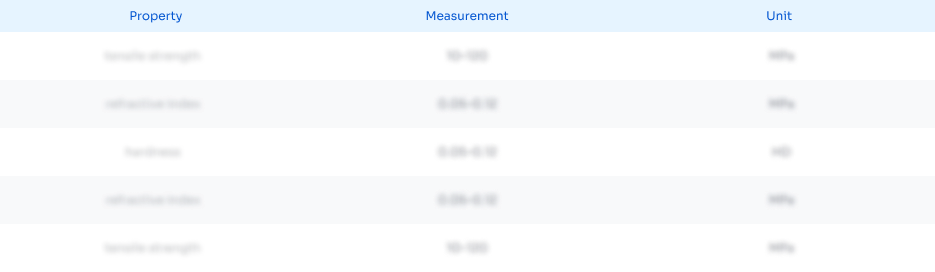
Abstract
Description
Claims
Application Information

- R&D Engineer
- R&D Manager
- IP Professional
- Industry Leading Data Capabilities
- Powerful AI technology
- Patent DNA Extraction
Browse by: Latest US Patents, China's latest patents, Technical Efficacy Thesaurus, Application Domain, Technology Topic, Popular Technical Reports.
© 2024 PatSnap. All rights reserved.Legal|Privacy policy|Modern Slavery Act Transparency Statement|Sitemap|About US| Contact US: help@patsnap.com