Method for pressurized induction smelting of high nitrogen stainless steel through pressure control in stages
A high-nitrogen stainless steel, pressure induction technology, applied in the direction of electric furnace, furnace, furnace type, etc., can solve the problems of accelerating the gas phase nitriding process, excessive nitrogen content of high-nitrogen stainless steel, increasing the difficulty of nitrogen content control, etc., to reduce Production cost, the effect of solving the problem of nitrogen pores
- Summary
- Abstract
- Description
- Claims
- Application Information
AI Technical Summary
Problems solved by technology
Method used
Image
Examples
Embodiment 1
[0050] The target steel grade is 18Cr18Mn2Mo0.9N, and its composition control range and smelting control target are shown in Table 2.
[0051] Table 2 18Cr18Mn2Mo0.9N composition control range and control target (wt%)
[0052]
[0053] Specific steps are as follows:
[0054] (1) Determination of batching and pressure parameters: According to the elemental composition of the target steel grade and formula ①, formula ②, and formula ③, the smelting pressure P 1 0.18MPa, casting pressure P 2 is 0.99MPa, the actual weight percentage (wt%) of the nitrogen content in the smelting raw materials 1 0.65%; based on this combination of raw material composition shown in Table 1 to prepare smelting raw materials, add 1.5kg / t electrolytic aluminum for deoxidation, wherein smelting raw materials include: 12044g industrial pure iron, 2683g metallic chromium, 400g metallic molybdenum, 3954g metallic Manganese, 92g industrial silicon, 1154g chromium nitride, 17.21g graphite.
[0055] (2) ...
Embodiment 2
[0063] The target steel grade is 18Cr14Mn3Mo0.9N, and its composition control range and smelting control target are shown in Table 4.
[0064] Table 4 18Cr14Mn3Mo0.9N composition control range and control target (wt%)
[0065]
[0066] Specific steps are as follows:
[0067] (1) Determination of batching and pressure parameters: According to the elemental composition of the target steel grade and formula ①, formula ②, and formula ③, the smelting pressure P 1 0.28MPa, casting pressure P 2 is 1.15MPa, the actual weight percentage (wt%) of the nitrogen content in the smelting raw material 1 It is 0.58%; based on this combination of the raw materials shown in Table 1, the smelting raw materials are prepared, and 1.5kg / t electrolytic aluminum is added for deoxidation. The smelting raw materials include: 13285g industrial pure iron, 2931g metal chromium, 630g metal molybdenum, 3230g metal Manganese, 97g industrial silicon, 1082g chromium nitride, 18.56g graphite.
[0068] (2)...
Embodiment 3
[0076] The target steel grade is 18Cr14Mn3Mo1Ni0.7N, and its chemical composition is shown in Table 6.
[0077] Table 6 18Cr14Mn3Mo1Ni0.7N composition control range and control target (wt%)
[0078]
[0079] Specific steps are as follows:
[0080] (1) Determination of batching and pressure parameters: According to the elemental composition of the target steel grade and formula ①, formula ②, and formula ③, the smelting pressure P 1 0.16MPa, casting pressure P 2 is 0.92MPa, the actual weight percentage (wt%) of the nitrogen content in the smelting raw materials 1 It is 0.48%; combined with the raw material composition shown in Table 1 to prepare smelting raw materials, adding 1.5kg / t electrolytic aluminum for deoxidation, wherein the smelting raw materials include: 13177g industrial pure iron, 3035g metal chromium, 2943g metal manganese, 210g metal Nickel, 631g metal molybdenum, 105g industrial silicon, 851g chromium nitride, 21.02g graphite.
[0081] (2) Charging: put in...
PUM
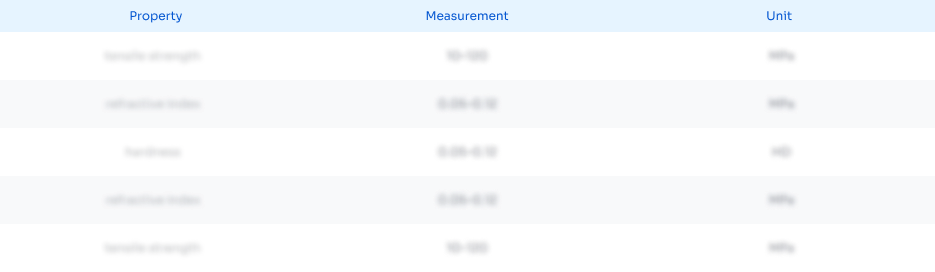
Abstract
Description
Claims
Application Information

- R&D
- Intellectual Property
- Life Sciences
- Materials
- Tech Scout
- Unparalleled Data Quality
- Higher Quality Content
- 60% Fewer Hallucinations
Browse by: Latest US Patents, China's latest patents, Technical Efficacy Thesaurus, Application Domain, Technology Topic, Popular Technical Reports.
© 2025 PatSnap. All rights reserved.Legal|Privacy policy|Modern Slavery Act Transparency Statement|Sitemap|About US| Contact US: help@patsnap.com