Method for coating aluminum alloy by using micro-arc oxidation green film layer
A technology of micro-arc oxidation and aluminum alloy, which is applied in the direction of anodic oxidation, etc., can solve the problems of corrosion resistance to be improved, micro-arc oxidation film stain resistance, scratch resistance and poor compactness, etc., to achieve low porosity and high hardness , the effect of uniform film layer
- Summary
- Abstract
- Description
- Claims
- Application Information
AI Technical Summary
Problems solved by technology
Method used
Image
Examples
Embodiment 1
[0049] The present invention selects 6063 aluminum alloy as the base material, its chemical composition is shown in Table 1, and the chemical reagents used in the test are shown in Table 2.
[0050] Table 1 Composition of 6063 aluminum alloy (wt%)
[0051]
[0052] Table 2 Chemical reagents used in the test
[0053]
[0054] In the present invention, the 6063 aluminum plate is cut into 7mm * 7mm * 12mm cuboid fritters on the wire electric discharge machine, drills a hole (Ф2.5mm) on one side of it with a drilling machine, taps with the tap corresponding to the hole, In order to facilitate the tight connection with the tapped aluminum wire during the micro-arc oxidation reaction process, it is ensured that the sample will not fall off during the reaction process. The sample was polished on SiC sandpaper of different thicknesses, starting from 400# coarse sandpaper, and then polished 5 times until fine 1000#. Soak the sample in alcohol to get rid of the grease on its sur...
Embodiment 2
[0057] Changing the concentration of ammonium metavanadate in Example 1 to 5 g / L, and keeping other parameters unchanged, the color of the obtained film layer A1 is very uneven, and many parts appear black.
Embodiment 3
[0059] Changing the concentration of ammonium metavanadate in Example 1 to 7g / L, and keeping other parameters unchanged, the color of the obtained film layer A3 is dark green and the surface is relatively smooth.
PUM
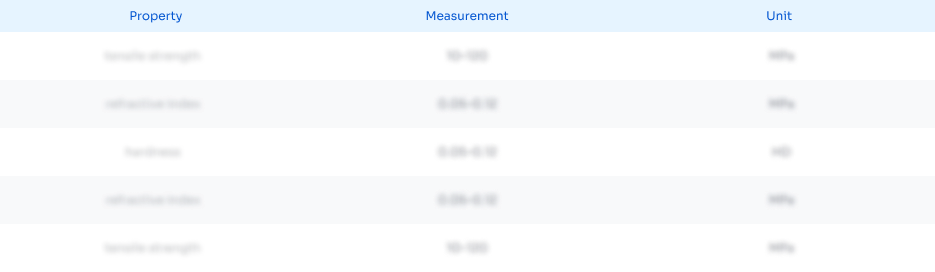
Abstract
Description
Claims
Application Information

- R&D Engineer
- R&D Manager
- IP Professional
- Industry Leading Data Capabilities
- Powerful AI technology
- Patent DNA Extraction
Browse by: Latest US Patents, China's latest patents, Technical Efficacy Thesaurus, Application Domain, Technology Topic, Popular Technical Reports.
© 2024 PatSnap. All rights reserved.Legal|Privacy policy|Modern Slavery Act Transparency Statement|Sitemap|About US| Contact US: help@patsnap.com