Ni-based corrosion resistant alloy for high-acidity oil-gas field and manufacturing method of oil casing of Ni-based corrosion resistant alloy for high-acidity oil-gas field
A corrosion-resistant alloy and technology for oil and gas fields, applied in the manufacture of nickel-based corrosion-resistant alloy casings for high-acid oil and gas fields, and nickel-based corrosion-resistant alloys for high-acid oil and gas fields, can solve the problem that extrusion molding is easy to crack, and the structure and properties are difficult to meet. Standard requirements, narrow processing temperature range, etc., to achieve the effect of reasonable production process parameters, excellent comprehensive mechanical properties, and reasonable grain size control
- Summary
- Abstract
- Description
- Claims
- Application Information
AI Technical Summary
Problems solved by technology
Method used
Examples
Embodiment 2
[0064] The chemical composition weight percent of this nickel base corrosion-resistant alloy embodiment is:
[0065] C: 0.014%; Si: 0.32%; Mn: 0.43%; P: 0.016%; S: 0.0025%; Cr: 22.83%; Fe: 19.54%; Mo: 7.37%; W: 1.56%; N: 0.0085%; Ti=0.22%; the rest is Ni and unavoidable impurities. Mo+0.5×W=8.15%, (Ti / 6) / (C+N)=1.63.
[0066] Embodiment 2 of the manufacturing method of the oil casing pipe
[0067] The manufacturing method of nickel-based corrosion-resistant alloy oil casing for high-acid oil and gas fields in this embodiment includes the following sequential steps:
[0068] 1. Smelting
[0069] The nickel-based corrosion-resistant alloy is smelted by VIM+ESR method to obtain electroslag ingot, and its composition mass percentage is:
[0070] C: 0.014%; Si: 0.32%; Mn: 0.43%; P: 0.016%; S: 0.0025%; Cr: 22.83%; Fe: 19.54%; Mo: 7.37%; W: 1.56%; N: 0.0085%; Ti=0.22%; the rest is Ni and unavoidable impurities. Mo+0.5×W=8.15%, (Ti / 6) / (C+N)=1.63.
[0071] 2. Tube blank process...
PUM
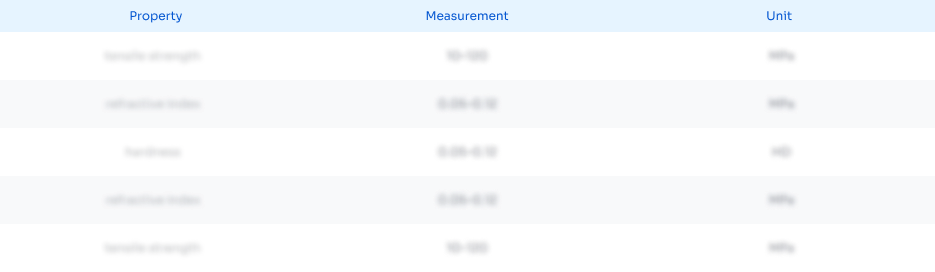
Abstract
Description
Claims
Application Information

- R&D Engineer
- R&D Manager
- IP Professional
- Industry Leading Data Capabilities
- Powerful AI technology
- Patent DNA Extraction
Browse by: Latest US Patents, China's latest patents, Technical Efficacy Thesaurus, Application Domain, Technology Topic, Popular Technical Reports.
© 2024 PatSnap. All rights reserved.Legal|Privacy policy|Modern Slavery Act Transparency Statement|Sitemap|About US| Contact US: help@patsnap.com