Boron-based metal ceramic material and preparation method thereof
A cermet and weight ratio technology, applied in the field of ceramic materials, can solve the problems of low mechanical strength and achieve the effect of improving strength and service time
- Summary
- Abstract
- Description
- Claims
- Application Information
AI Technical Summary
Problems solved by technology
Method used
Image
Examples
Embodiment 1
[0021] (1) Take molybdenum boride 35Kg, zirconium boride 24Kg, titanium boride 13Kg, tungsten powder 16Kg, nickel oxide 8Kg, manganese silicide 12Kg, chromium powder 13Kg by weight respectively, and above-mentioned each material is mixed to uniform; ( 2) Perform ball milling on the above-mentioned homogeneously mixed mixed materials, put the above-mentioned materials into a ball mill jar, add grinding balls, and carry out ball milling. The ball milling time is 5 hours; (3) After ball milling, press the cermet material in a pressing mold , the pressing pressure is 160MPa, and the pressing time is 5h; (4) high-temperature sintering, the sintering temperature is 940°C, and the sintering time is 3h; it is lowered to room temperature, and the boron-based cermet material is prepared.
Embodiment 2
[0023] (1) Take molybdenum boride 16Kg, zirconium boride 36Kg, titanium boride 7Kg, tungsten powder 6Kg, nickel oxide 15Kg, manganese silicide 5Kg, chromium powder 7Kg by weight respectively, and above-mentioned each material is mixed to uniform; ( 2) The above-mentioned uniformly mixed mixed materials are then ball-milled, and the above-mentioned materials are put into a ball-milling tank, and grinding balls are added to carry out ball-milling. The ball-milling time is 12 hours; (3) After ball-milling, press the cermet material in a pressing mold , the pressing pressure is 130MPa, and the pressing time is 8h; (4) high-temperature sintering, the sintering temperature is 910°C, and the sintering time is 7h; when it is lowered to room temperature, it is the prepared boron-based cermet material.
Embodiment 3
[0025] (1) Take molybdenum boride 30Kg, zirconium boride 28Kg, titanium boride 8Kg, tungsten powder 13Kg, nickel oxide 10Kg, manganese silicide 10Kg, chromium powder 11Kg by weight respectively, and above-mentioned each material is mixed to uniform; ( 2) Perform ball milling on the above-mentioned homogeneously mixed mixed materials, put the above-mentioned materials into a ball mill jar, add grinding balls, and carry out ball milling. The ball milling time is 5 hours; (3) After ball milling, press the cermet material in a pressing mold , the pressing pressure is 160MPa, and the pressing time is 5h; (4) high-temperature sintering, the sintering temperature is 940°C, and the sintering time is 3h; it is lowered to room temperature, and the boron-based cermet material is prepared.
PUM
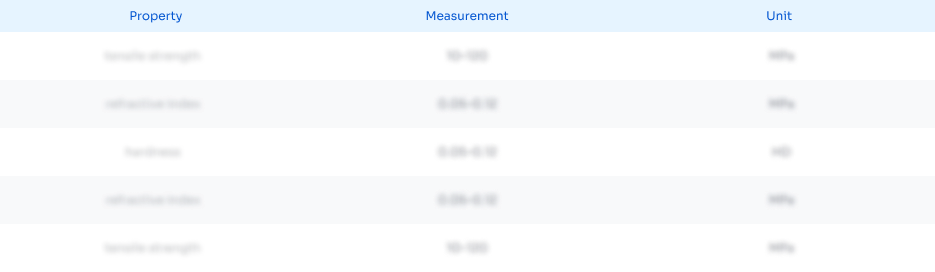
Abstract
Description
Claims
Application Information

- R&D
- Intellectual Property
- Life Sciences
- Materials
- Tech Scout
- Unparalleled Data Quality
- Higher Quality Content
- 60% Fewer Hallucinations
Browse by: Latest US Patents, China's latest patents, Technical Efficacy Thesaurus, Application Domain, Technology Topic, Popular Technical Reports.
© 2025 PatSnap. All rights reserved.Legal|Privacy policy|Modern Slavery Act Transparency Statement|Sitemap|About US| Contact US: help@patsnap.com