Cutting tool forging method
A technology of cutting knives and blanks, which is applied in the field of wood recycling, can solve the problems of unavailability of waste materials, and achieve the effect of improving processing efficiency and meeting processing needs.
- Summary
- Abstract
- Description
- Claims
- Application Information
AI Technical Summary
Problems solved by technology
Method used
Image
Examples
Embodiment 1
[0033] Such as Figure 1 to Figure 2 As shown, the present invention provides a waste wood recycling device, comprising: a drying chamber 1, a cutting chamber connected to the drying chamber 1, a feed inlet 11 provided on the side of the drying chamber 1, and a side of the cutting chamber 2 The outlet 29; the drying chamber 1 includes a heater 15 located at the bottom, two pulleys 13 located above the heater 15, and a conveyor belt 14 connected to the two pulleys 13, and a fan 12 located above the conveyor belt 14 ; A cutting mechanism 20 is provided in the cutting chamber 2. The cutting mechanism 20 includes a cutting platform 24 located at the bottom and connected to the conveyor belt 14, and a cutting device provided above the cutting platform 24; the cutting device includes a telescopic arm 21 located at the top of the cutting chamber 2 and a knife cover provided at the end of the telescopic arm 21 22. The cutter 23 arranged in the cutter cover 22; the cutting platform 24 ...
Embodiment 2
[0036] The forming material of the cutter, the element composition is: C: 1%, Mn: 3%, Co: 3%, Cr: 2%, Zr: 0.5%, W: 5%, Zr: 0.5%, Ga: 0.05%, Ni: 0.5%, S: ≤0.020%, P: ≤0.020%, and the balance is Fe.
[0037] The forging method of the cutter is as follows:
[0038] ① Prepare billets by melting according to the following elemental composition
[0039] C: 1%, Mn: 3%, Co: 3%, Cr: 2%, Zr: 0.5%, W: 5%, Zr: 0.5%, Ga: 0.05%, Ni: 0.5%, S: ≤0.020% , P: ≤0.020%, the balance is Fe;
[0040] ②. Anneal the billet with a holding temperature of 600°C, holding time for 5 hours, and then cooling to 450°C for 5 hours;
[0041] ③. Machining the blank car into a cutter;
[0042] ④ Heat treatment of the cutter;
[0043] ⑤ For the knife immersion treatment, the treatment liquid consists of: 5 parts of chrysin, 15 parts of ethanol, 5 parts of DMF, 5 parts of acrylate emulsion, 5 parts of citric acid, and the processing method of the treatment liquid is conventional mixing and stirring;
[0044] ⑥ Tempering and fi...
Embodiment 3
[0046] The cutting mechanism of the waste wood recycling device includes a cutting platform located at the bottom and connected to the conveyor belt, and a cutting device arranged above the cutting platform; the cutting device includes a telescopic arm located at the top of the cutting chamber, The knife cover at the end of the arm, the cutting knife arranged in the knife cover; the cutting platform is provided with a knife groove corresponding to the cutting knife; the cutting knife is forged from the cutting knife molding material (prepared in Example 2) to make.
[0047] The manufacturing method of the cutting mechanism of the waste wood recycling device, the steps are as follows:
[0048] ①. Forging the forming material of the cutter to form a cutter (the process is the same as that in Example 2);
[0049] ② Install a telescopic arm in the upper part of the cutting chamber, and install a knife cover and a cutter in the lower part of the telescopic arm;
[0050] ③. Install a cutti...
PUM
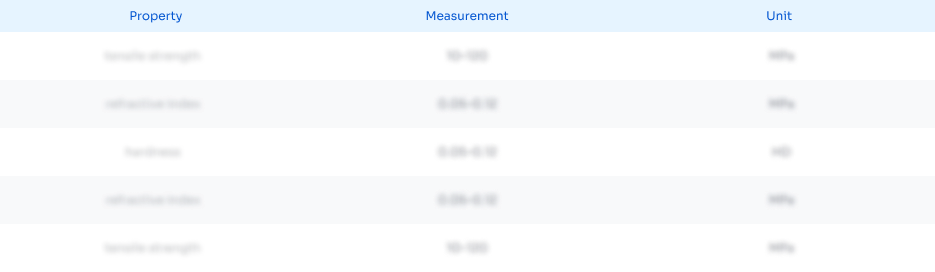
Abstract
Description
Claims
Application Information

- R&D
- Intellectual Property
- Life Sciences
- Materials
- Tech Scout
- Unparalleled Data Quality
- Higher Quality Content
- 60% Fewer Hallucinations
Browse by: Latest US Patents, China's latest patents, Technical Efficacy Thesaurus, Application Domain, Technology Topic, Popular Technical Reports.
© 2025 PatSnap. All rights reserved.Legal|Privacy policy|Modern Slavery Act Transparency Statement|Sitemap|About US| Contact US: help@patsnap.com