Method for smelting magnesium and co-producing ferrochrome-containing liquid with ferrosilicon bath stair reduction silicothermic method
A technology of ferrochromium and silicon thermal method, which is applied in the field of silicon thermal magnesium smelting and co-production of chromium-containing ferroalloy liquid, which can solve problems such as low efficiency, excessive ferrosilicon, and large heat loss, so as to improve production efficiency, realize mechanization, and facilitate mechanized effect
- Summary
- Abstract
- Description
- Claims
- Application Information
AI Technical Summary
Problems solved by technology
Method used
Image
Examples
no. 1 example
[0133] A: 48 tons of 65% ferrosilicon liquid smelted from the submerged arc furnace, keep the temperature at 1600°C, prepare 20 tons of calcined dolomite containing 40% MgO at the same time, keep the temperature at 800°C, and prepare 3.5 tons of calcined bauxite , 1.3 tons of fluorite as a flux.
[0134] The B ferrosilicon liquid is blended into the liquid material container 102 above the magnesium smelting furnace, and is intermittently injected into the magnesium smelting furnace from the liquid material container 102, and the calcined white 101 is also intermittently added into the furnace from the top of the furnace, and makes the furnace Mix ferrosilicon liquid with calcined white and flux evenly.
[0135] C. When half of the ferrosilicon liquid is added and half of the solid charge is also added, the furnace starts to be powered, and at the same time, the vacuum is evacuated to 3000Pa, and argon is introduced for bottom blowing and stirring. Magnesium vapor begins to ent...
no. 2 example
[0143] The preparation of raw materials is basically the same as that of the first embodiment. When smelting each furnace, 2 tons of silicon-aluminum ferroalloy containing 20% aluminum and 40% silicon are added to the ferrosilicon liquid, and the rest of the operations remain unchanged. Aluminum preferentially reduces magnesium to silicon, which becomes alumina and enters the slag. The reducing agent alloy liquid can still produce magnesium metal and ferrochrome alloy liquid stably. In the second embodiment, the smelting principle of reducing chromium by aluminum and silicon and the source and destination of chromium and iron elements are as follows Figure 6 shown.
no. 3 example
[0145] The initial raw material is 48 tons of nickel-containing ferrosilicon liquid, of which the silicon content is still 65%, the nickel content is 7%, and the rest is iron. Ferrosilicon is not added in the middle, and other operations remain unchanged. The reducing agent alloy solution can still produce magnesium metal stably. After the total amount of ferrosilicon drops below 35 tons, the addition of calcined dolomite will be halved for each furnace, and the addition of flux and auxiliary materials will also be halved in proportion. When the silicon content is 30% The quality of the alloy liquid is 24 tons, which is transferred to smelting ferrochrome, and mixed with chromium ore and iron oxide scale. During the chromium smelting process, nickel remains in the alloy liquid, and finally 36 tons of stainless steel mother liquid containing 20% chromium and 8.6% nickel are obtained. In the third embodiment, the smelting principle of silicon reduction of chromium and the sourc...
PUM
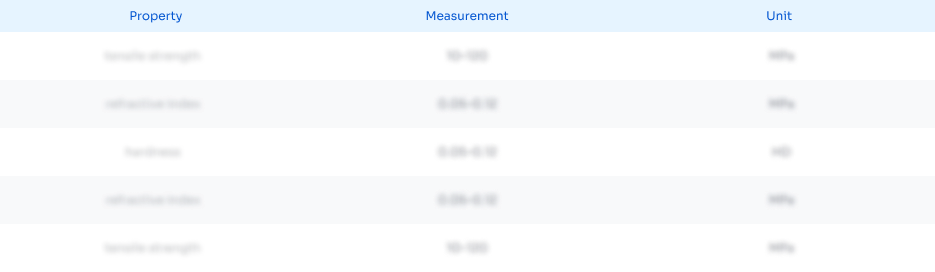
Abstract
Description
Claims
Application Information

- R&D Engineer
- R&D Manager
- IP Professional
- Industry Leading Data Capabilities
- Powerful AI technology
- Patent DNA Extraction
Browse by: Latest US Patents, China's latest patents, Technical Efficacy Thesaurus, Application Domain, Technology Topic, Popular Technical Reports.
© 2024 PatSnap. All rights reserved.Legal|Privacy policy|Modern Slavery Act Transparency Statement|Sitemap|About US| Contact US: help@patsnap.com