Ceramic polyolefin cable material and preparation method thereof
A technology for ceramizing polyolefin and cable materials, which is applied in circuits, electrical components, plastic/resin/wax insulators, etc., can solve the problems of high processing temperature, low residual strength, complex process, etc., to meet the requirements of flexible laying and preparation. The method is concise and the preparation cost is low
- Summary
- Abstract
- Description
- Claims
- Application Information
AI Technical Summary
Problems solved by technology
Method used
Image
Examples
Embodiment 1
[0018] 100 parts of ethylene-α-propylene copolymer weighed in parts by weight, porcelain powder A is attapulgite 180 parts, porcelain powder B is 15 parts of borax and ammonium borate 15 parts, lubricant is 12 parts of stearic acid and 10100.3 parts of antioxidant are put into the internal mixer for mixing (also known as internal mixing), when the temperature is 100°C, the material is discharged and introduced into the twin-screw extruder through the conical feeding hopper for melt extrusion, and the twin-screw The temperature of zone 1 to zone 9 of the extruder is 60°C for zone 1, 70°C for zone 2, 80°C for zone 3, 85°C for zone 4, 90°C for zone 5, 90°C for zone 6, 90°C for zone 7, and 90°C for zone 8. 95°C, nine zone 95°C, head temperature 100°C, after exiting the twin-screw extruder, cold cut to obtain ceramic polyolefin cable material.
Embodiment 2
[0020] 50 parts of ethylene-alpha-butene copolymer, 25 parts of ethylene-alpha-octene copolymer, 25 parts of ethylene-alpha-hexene copolymer, 50 parts of vitrified powder A, namely glass fiber, weighed in parts by weight , 50 parts of alumina nanotubes and 50 parts of calcium carbonate whiskers, 60 parts of vitrified powder B, namely borax, 10 parts of lubricants, namely calcium stearate and zinc stearate, 168 parts of antioxidant and 300 parts of antioxidant Put 0.5 parts into the internal mixer for mixing (also known as internal mixing), when the temperature reaches 115°C, the material is discharged and introduced into the twin-screw extruder through the conical feeding hopper for melting and extrusion. One part of the twin-screw extruder The temperature in Zone 1 to Zone 9 is 50°C for Zone 1, 65°C for Zone 2, 70°C for Zone 3, 80°C for Zone 4, 95°C for Zone 5, 95°C for Zone 6, 95°C for Zone 7, 95°C for Zone 8, and 95°C for Zone 9. 90°C, head temperature 95°C, after exiting t...
Embodiment 3
[0022]100 parts of ethylene-α-octene copolymer weighed in parts by weight, porcelain powder A is 50 parts of sericite, 25 parts of muscovite and 25 parts of phlogopite, porcelain powder B is low-melting phosphate glass powder Or 100 parts of low-melting point borate glass powder, 7.5 parts of lubricant, namely octyl stearate, 7.5 parts of liquid paraffin and 10760.3 parts of antioxidant are put into the internal mixer for mixing (also called banburying). When the temperature is 105°C, the material is discharged and introduced into the twin-screw extruder through the conical feeding hopper for melt extrusion. The temperatures of the first zone to the ninth zone of the twin-screw extruder are respectively 55°C for the first zone, 60°C for the second zone, and 75°C for the third zone. ℃, the fourth zone is 90°C, the fifth zone is 92°C, the sixth zone is 92°C, the seventh zone is 92°C, the eighth zone is 92°C, the ninth zone is 92°C, the head temperature is 98°C, after exiting the ...
PUM
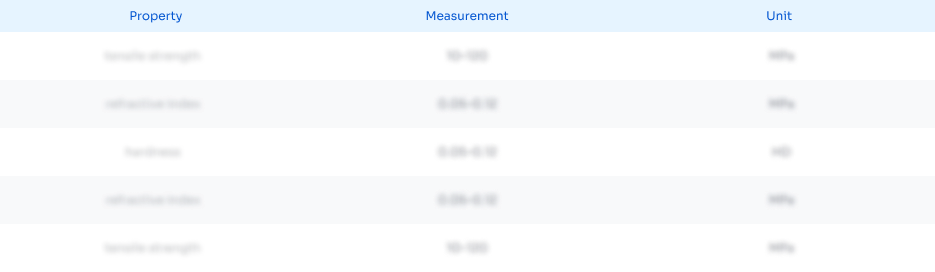
Abstract
Description
Claims
Application Information

- R&D
- Intellectual Property
- Life Sciences
- Materials
- Tech Scout
- Unparalleled Data Quality
- Higher Quality Content
- 60% Fewer Hallucinations
Browse by: Latest US Patents, China's latest patents, Technical Efficacy Thesaurus, Application Domain, Technology Topic, Popular Technical Reports.
© 2025 PatSnap. All rights reserved.Legal|Privacy policy|Modern Slavery Act Transparency Statement|Sitemap|About US| Contact US: help@patsnap.com