Recovery process of complex multi-metal ores difficult to treat
A polymetallic ore, refractory technology, applied in non-metallic elements, process efficiency improvement, inorganic chemistry and other directions, can solve the problems of low recovery rate of valuable elements, environmental pollution, high equipment requirements, and achieve clean process without pollution, The effect of less process hazard and less investment
- Summary
- Abstract
- Description
- Claims
- Application Information
AI Technical Summary
Problems solved by technology
Method used
Image
Examples
Embodiment 1
[0030] A recovery process for refractory complex polymetallic ores, such as figure 1 shown, including the following steps:
[0031] Step (1), oxygen pressure leaching of polymetallic minerals: after ball milling polymetallic minerals, passing through a 320-mesh sieve, adding acid solution to a pressure vessel, adding materials according to the mass ratio of acid solution to polymetallic minerals at 4.5:1, then sealing and passing Add oxygen and heat and stir for leaching. Control the leaching conditions: 150~160°C, oxygen partial pressure 0.8MPa, leaching time 4h, solution pH 1-3; filter after leaching, and analyze the filter residue. Wherein, the acid solution is a zinc extraction raffinate, wherein the concentration of sulfuric acid is 80g / L;
[0032] The comprehensive leaching rates of valuable metals are: Cu96.7%, Zn95.3%, Fe13.4%, and gold, silver, lead, arsenic, and sulfur are basically retained in the leaching residue. The main element contents (%) of the leach slag ...
Embodiment 2
[0046] A recovery process for refractory complex polymetallic ores, such as figure 1 shown, including the following steps:
[0047] Step (1), oxygen pressure leaching of polymetallic ore: after ball milling polymetallic ore, pass through a 320 mesh sieve, add acid solution into the pressure vessel, add material according to the mass ratio of acid solution to polymetallic ore at 4:1, then seal and pass through Add oxygen and heat and stir for leaching. Control the leaching conditions: 170~180°C, oxygen partial pressure 0.5MPa, leaching time 6h, solution pH 1-3; filter after leaching, and analyze the filter residue. Wherein, the acid solution is a zinc extraction raffinate, wherein the concentration of sulfuric acid is 75g / L;
[0048] The comprehensive leaching rates of valuable metals are: Cu96.2%, Zn95.1%, Fe13.0%, and gold, silver, lead, arsenic, and sulfur are basically retained in the leaching residue. The main element contents (%) of the leach slag are: Au11.5g / t, Ag816...
Embodiment 3
[0062] A recovery process for refractory complex polymetallic ores, such as figure 1 shown, including the following steps:
[0063] Step (1), oxygen pressure leaching of polymetallic ore: after ball milling polymetallic ore, pass through a 320-mesh sieve, add acid solution to the pressure vessel, add materials according to the mass ratio of acid solution to polymetallic ore at 5:1, then seal and pass through Add oxygen and heat and stir for leaching. Control the leaching conditions: 160~170°C, oxygen partial pressure 0.2MPa, leaching time 1h, solution pH 1-3; filter after leaching, and analyze the filter residue. Wherein, described acid solution is sulfuric acid aqueous solution, wherein sulfuric acid concentration 80g / L;
[0064] The comprehensive leaching rates of valuable metals are: Cu97.5%, Zn95.8%, Fe14.1%, and gold, silver, lead, arsenic, and sulfur are basically retained in the leaching residue. The main element contents (%) of the leach slag are: Au11.6g / t, Ag817.5...
PUM
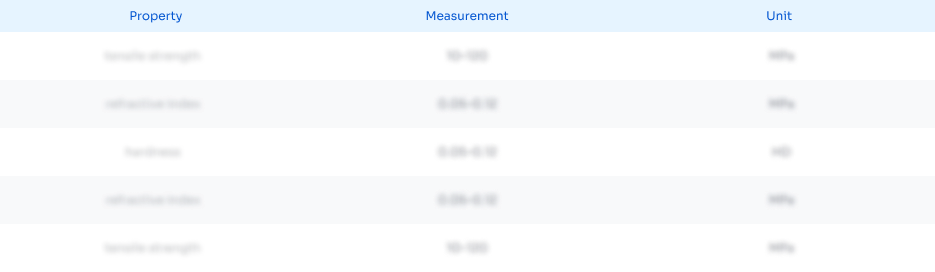
Abstract
Description
Claims
Application Information

- R&D
- Intellectual Property
- Life Sciences
- Materials
- Tech Scout
- Unparalleled Data Quality
- Higher Quality Content
- 60% Fewer Hallucinations
Browse by: Latest US Patents, China's latest patents, Technical Efficacy Thesaurus, Application Domain, Technology Topic, Popular Technical Reports.
© 2025 PatSnap. All rights reserved.Legal|Privacy policy|Modern Slavery Act Transparency Statement|Sitemap|About US| Contact US: help@patsnap.com