Method for preparing carbon quantum dot-doped sodium borosilicate glass material
A technology of sodium borosilicate glass and carbon quantum dots, which is applied in the field of preparation of sodium borosilicate glass materials, can solve the problems of complicated operation, long experiment cycle, carbonization failure of carbon quantum dots, etc., and achieve simple operation, low cost, and broaden the practical Applied effect
- Summary
- Abstract
- Description
- Claims
- Application Information
AI Technical Summary
Problems solved by technology
Method used
Image
Examples
Embodiment 1
[0030] Dissolve 26ml of TEOS in 30ml of a mixed solution of absolute ethanol, deionized water, and dilute nitric acid, stir for 1 hour, and fully hydrolyze (solution 1).
[0031] 4.441g H 3 BO 3 Dissolve in 40ml of ethylene glycol methyl ether, and add to solution 1 (solution 2) after it is completely dissolved. Dissolve 0.370g of metal Na in 30ml of absolute ethanol, and add it to solution 2 after it is completely dissolved.
[0032] The resulting mixed solution was stirred for 1 h. Pour it into a plastic box and let it stand for 5d to form a wet gel. Dry at 120°C for 30 days to form a crack-free and complete sodium borosilicate porous dry glue.
[0033] Dry glue in a tube furnace O 2 Heating to 450°C under atmosphere, keeping the temperature for 10 hours, cooling, and taking out the porous sodium borosilicate glass dry glue for use.
[0034] Add 5ml of oleylamine to 5ml of PAA with a mass fraction of 50% and 1ml of 0.5mol / L nitric acid mixed solution, transfer the mixed ...
Embodiment 2
[0040] Dissolve 26ml of TEOS in 30ml of a mixed solution of absolute ethanol, deionized water, and dilute nitric acid, stir for 1 hour, and fully hydrolyze (solution 1).
[0041] 4.441g H 3 BO 3 Dissolve in 40ml of ethylene glycol methyl ether, and add to solution 1 (solution 2) after it is completely dissolved. Dissolve 0.370g of metal Na in 30ml of absolute ethanol, and add it to solution 2 after it is completely dissolved.
[0042] The resulting mixed solution was stirred for 1 h. Pour it into a plastic box and let it stand for 10d to form a wet gel. Dry at 120°C for 50 days to form a crack-free and complete sodium borosilicate porous dry glue.
[0043] Dry glue in a tube furnace O 2 Heating to 450°C under atmosphere, keeping it warm for 30 hours, cooling to room temperature naturally, taking out the porous sodium borosilicate glass dry glue for use.
[0044] Add 10ml of oleylamine to 5ml of PAA with a mass fraction of 50% and 1ml of 0.5mol / L nitric acid mixed solutio...
Embodiment 3
[0050] Dissolve 26ml of TEOS in 30ml of a mixed solution of absolute ethanol, deionized water, and dilute nitric acid, stir for 1 hour, and fully hydrolyze (solution 1).
[0051] 4.441g H 3 BO 3 Dissolve in 40ml of ethylene glycol methyl ether, and add to solution 1 (solution 2) after it is completely dissolved. Dissolve 0.370g of metal Na in 30ml of absolute ethanol, and add it to solution 2 after it is completely dissolved.
[0052] The resulting mixed solution was stirred for 1 h. Pour it into a plastic box and let it stand for 15 days to form a wet gel. Dry at 100°C for 50 days to form a complete dry sodium borosilicate gel without cracks.
[0053] Dry glue in a tube furnace O 2 Heating to 470°C under the atmosphere, keeping the temperature for 10 hours until all the organic matter is removed, cooling, and taking out the porous sodium borosilicate glass dry glue for use.
[0054] Add 15ml of oleylamine to 5ml of 50% PAA and 1ml of 0.5mol / L nitric acid mixed solution,...
PUM
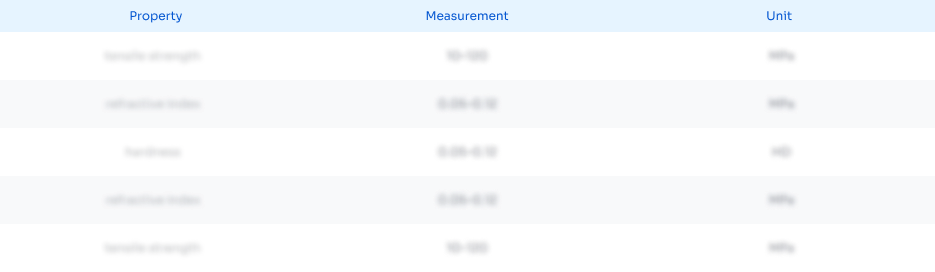
Abstract
Description
Claims
Application Information

- Generate Ideas
- Intellectual Property
- Life Sciences
- Materials
- Tech Scout
- Unparalleled Data Quality
- Higher Quality Content
- 60% Fewer Hallucinations
Browse by: Latest US Patents, China's latest patents, Technical Efficacy Thesaurus, Application Domain, Technology Topic, Popular Technical Reports.
© 2025 PatSnap. All rights reserved.Legal|Privacy policy|Modern Slavery Act Transparency Statement|Sitemap|About US| Contact US: help@patsnap.com