InAlN/AlGaN enhanced-type high-electron mobility transistor and manufacturing method thereof
A technology of high electron mobility and manufacturing method, applied in the field of InAlN/AlGaN enhanced high electron mobility transistor and its manufacturing, can solve the problem of reducing the ohmic contact resistance of the source and drain regions and the reverse leakage current of the gate, and growing an insulating gate dielectric It is difficult to control the process precision and cannot effectively realize the modulation of the 2DEG surface density, so as to simplify the manufacturing process steps and control difficulty, reduce the surface density of the two-dimensional electron gas, and improve the switching characteristics of the device.
- Summary
- Abstract
- Description
- Claims
- Application Information
AI Technical Summary
Problems solved by technology
Method used
Image
Examples
Embodiment 1
[0040] Embodiment 1, an enhanced high electron mobility transistor whose substrate is sapphire is manufactured.
[0041] Step 1, epitaxial AlN nucleation layer.
[0042] Using metal-organic chemical vapor deposition technology on the sapphire substrate, first epitaxy a low-temperature AlN nucleation layer with a thickness of 20nm; then deposit a high-temperature AlN nucleation layer with a thickness of 60nm on the low-temperature AlN nucleation layer;
[0043] The process conditions used for the low-temperature AlN material of the epitaxial layer are as follows: temperature is 610°C, pressure is 40Torr, ammonia gas flow rate is 1500 sccm, aluminum source flow rate is 4 sccm, and hydrogen gas flow rate is 2500 sccm;
[0044] The process conditions for depositing the upper layer high-temperature AlN material are as follows: temperature is 1050°C, pressure is 40 Torr, ammonia gas flow is 1500 sccm, aluminum source flow is 13 sccm, and hydrogen gas flow is 2500 sccm.
[0045] Ste...
Embodiment 2
[0063] In the second embodiment, an enhanced high electron mobility transistor whose substrate is silicon is manufactured.
[0064] In step 1, the AlN nucleation layer is epitaxially formed by metal-organic chemical vapor deposition technology.
[0065] (1a) Under the process conditions of temperature being 630° C., pressure being 40 Torr, ammonia gas flow rate being 1500 sccm, aluminum source flow rate being 4 sccm, and hydrogen gas flow rate being 2500 sccm, a low-temperature AlN nucleation layer with a thickness of 40 nm is epitaxially formed on a silicon substrate;
[0066] (1b) Deposit high temperature AlN nucleation with a thickness of 200nm on the low temperature AlN nucleation layer under the process conditions of temperature 1080°C, pressure 40 Torr, ammonia gas flow rate 1500 sccm, aluminum source flow rate 13 sccm, hydrogen gas flow rate 2500 sccm layer.
[0067] Step 2, Deposit Al using MOCVD 0.2 Ga 0.8 N-channel layer.
[0068] Under the process conditions of ...
Embodiment 3
[0085] Embodiment 3, fabricating an enhanced high electron mobility transistor whose substrate is silicon carbide.
[0086] Step A, epitaxial AlN nucleation layer.
[0087] A1) Using metal-organic chemical vapor deposition technology, the temperature is 620°C, the pressure is 40Torr, the flow rate of ammonia gas is 1500 sccm, the flow rate of aluminum source is 4 sccm, and the flow rate of hydrogen gas is 2500 sccm. Low temperature AlN nucleation layer;
[0088] A2) Using metal-organic chemical vapor deposition technology, the temperature is 1070°C, the pressure is 40Torr, the flow rate of ammonia gas is 1500 sccm, the flow rate of aluminum source is 13 sccm, and the flow rate of hydrogen gas is 2500 sccm. 100nm high temperature AlN nucleation layer.
[0089] Step B, Deposit Al 0.14 Ga 0.86 N-channel layer.
[0090] Al with a thickness of 700nm and an aluminum composition of 0.14 was deposited on the AlN nucleation layer by metal-organic chemical vapor deposition 0.14 Ga...
PUM
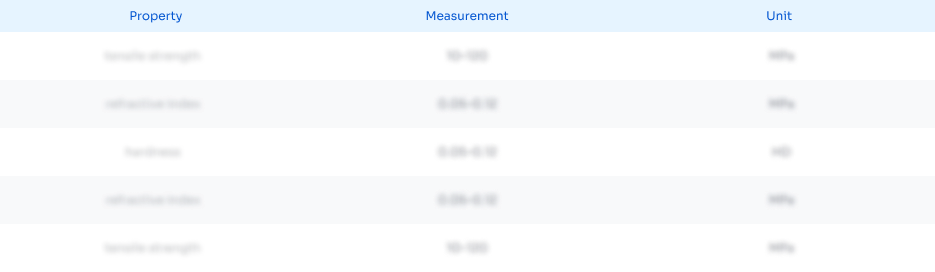
Abstract
Description
Claims
Application Information

- Generate Ideas
- Intellectual Property
- Life Sciences
- Materials
- Tech Scout
- Unparalleled Data Quality
- Higher Quality Content
- 60% Fewer Hallucinations
Browse by: Latest US Patents, China's latest patents, Technical Efficacy Thesaurus, Application Domain, Technology Topic, Popular Technical Reports.
© 2025 PatSnap. All rights reserved.Legal|Privacy policy|Modern Slavery Act Transparency Statement|Sitemap|About US| Contact US: help@patsnap.com