Great line energy gas-electric vertical welding flux core wire and production method thereof
A gas-electric vertical welding and flux-cored wire technology, applied in welding equipment, welding media, manufacturing tools, etc., can solve the problems of not meeting the welding effect of large and thick plates with large line energy and coarse metal structure, so as to meet the welding efficiency and The effect of deposited metal properties, improving impact toughness, maintaining continuity and stability
- Summary
- Abstract
- Description
- Claims
- Application Information
AI Technical Summary
Problems solved by technology
Method used
Image
Examples
Embodiment 1
[0016] (1) Take 22kg of reduced iron powder, 18kg of manganese-silicon alloy, 0.4kg of rare earth silicon, 1kg of nickel powder, 1.5kg of sodium fluoride, 3kg of magnesia, 2kg of 45 ferrosilicon, 5kg of aluminum-magnesium powder, 1.8kg of ferromolybdenum, and boron 0.5kg of iron and 3kg of ferro-titanium, weighed separately, mixed, fully stirred, and dried to obtain formula powder for use;
[0017] (2) Steel strip slitting, then ultrasonic cleaning, drying, rolling U-shaped groove, adding the formula powder obtained in step (1) into the U-shaped groove, and then closing, reducing, drawing, and winding to obtain the Welding wire.
Embodiment 2
[0019] (1) Take reduced iron powder FHT100.25: 20kg, manganese silicon alloy FeMn64Si18: 21kg, rare earth silicon 0.1kg, nickel powder 2kg, sodium fluoride 1.3kg, magnesia sand 2kg, 45 silicon iron 2kg, aluminum magnesium powder 6kg, molybdenum Iron FeMo55: 2.3kg, boron iron 0.8kg, titanium iron FeTi30: 4kg, weighed separately, mixed, fully stirred, and dried to obtain formula powder for use;
[0020] (2) The steel strip is slit, then ultrasonically cleaned, dried, rolled into the U-shaped groove, and the formula powder obtained in step (1) is added to the U-shaped groove with a filling factor of 20±0.5%. Then, it is closed, reduced in diameter, polished, coated with metal compound for lubrication, drawn, and taken up to obtain the welding wire.
Embodiment 3
[0022] (1) Take reduced iron powder FHT100.25: 26kg, manganese silicon alloy FeMn64Si18: 15kg, rare earth silicon 0.5kg, nickel powder 0.45kg, sodium fluoride 2.6kg, magnesia sand 5kg, 45 silicon iron 3kg, aluminum magnesium powder 3kg, Ferro-molybdenum FeMo55: 1kg, ferro-boron 0.3kg, and ferro-titanium FeTi30: 1kg, weighed separately, mixed, fully stirred, and dried to obtain formula powder for use;
[0023] (2) The steel strip is slit, then ultrasonically cleaned, dried, rolled into the U-shaped groove, and the formula powder obtained in step (1) is added to the U-shaped groove with a filling factor of 20±0.5%. Then, it is closed, reduced in diameter, polished, coated with metal compound for lubrication, drawn, and taken up to obtain the welding wire.
PUM
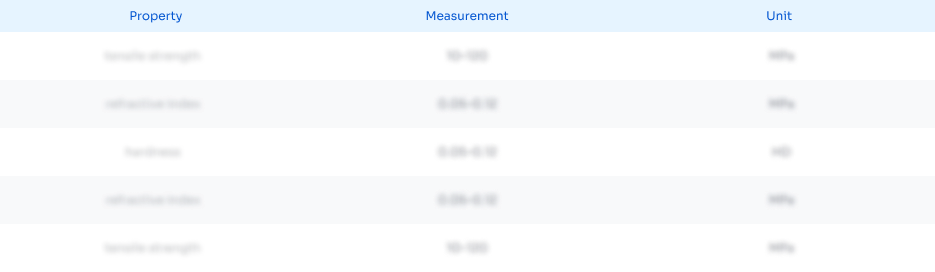
Abstract
Description
Claims
Application Information

- R&D
- Intellectual Property
- Life Sciences
- Materials
- Tech Scout
- Unparalleled Data Quality
- Higher Quality Content
- 60% Fewer Hallucinations
Browse by: Latest US Patents, China's latest patents, Technical Efficacy Thesaurus, Application Domain, Technology Topic, Popular Technical Reports.
© 2025 PatSnap. All rights reserved.Legal|Privacy policy|Modern Slavery Act Transparency Statement|Sitemap|About US| Contact US: help@patsnap.com