Silane crosslinked halogen-free flame-retardant polyolefin composite material and preparation method thereof
A technology of silane cross-linking and composite materials, which is applied in the field of silane cross-linking halogen-free flame-retardant polyolefin composite materials and its preparation, which can solve the difficulties in the application of intumescent flame retardants, deterioration of polymer physical properties, and low flame-retardant efficiency, etc. problems, achieve excellent mechanical properties, good surface properties, and improve water resistance
- Summary
- Abstract
- Description
- Claims
- Application Information
AI Technical Summary
Problems solved by technology
Method used
Image
Examples
preparation example Construction
[0030] The preparation method of the silane crosslinked halogen-free flame-retardant polyolefin composite material of the present invention comprises the following steps:
[0031] (1) Preparation of base material: Mix the dry-treated polyolefin resin, silane, initiator, lubricant, antioxidant and anti-crosslinking agent in a high-speed mixer at a low speed, and then force feed the In the twin-screw extruder, the processing temperature is controlled at 180°C~220°C, extruded and granulated, and dried at 70°C~80°C for 2~4 hours to obtain the base material;
[0032] (2) Preparation of flame retardant masterbatch: Mix the dry-processed polyolefin resin, flame retardant, flame retardant synergist, lubricant and antioxidant in a banbury mixer evenly, and pass Double-cone forced feeding in a twin-screw extruder, the processing temperature is controlled at 120°C~170°C, extruded and granulated, and dried at 70°C~80°C for 2~4 hours to obtain flame retardant masterbatch;
[0033] (3) Pre...
Embodiment 1
[0041] The silane crosslinked halogen-free flame-retardant polyolefin composite material of this embodiment is prepared as follows:
[0042] (1) Preparation of base material: dry treated 98.3 parts of polyethylene, 1.5 parts of vinyltrimethoxysilane, 0.06 parts of initiator dicumyl peroxide, 0.02 parts of perfluoropolyether oil, 0.02 parts of antioxidant 1010 and 0.1 part of anti-crosslinking agent caprolactam are mixed evenly in a high-speed mixer at a low speed, and then forced to feed in a twin-screw extruder at 180°C~220°C, extruded and granulated, and dried at 80°C for 4 hours to obtain Binder.
[0043] (2) Preparation of flame retardant masterbatch: Dry 50 parts of polyethylene, 4 parts of maleic anhydride grafted polyethylene resin, 8.8 parts of triazine hyperbranched charcoal agent, 35.2 parts of silicone gel (siloxane ) Microencapsulated ammonium polyphosphate, 1 part of flame retardant synergist zeolite powder, 0.5 part of lubricant zinc stearate and 0.5 part of ant...
Embodiment 2
[0050] The silane crosslinked halogen-free flame-retardant polyolefin composite material of this embodiment is prepared as follows:
[0051] (1) Preparation of base material: 94.8 parts of ethylene-vinyl acetate copolymer, 4 parts of vinyltriethoxysilane, 0.2 part of initiator tert-butyl peroxyacetate, 0.2 part of lubricant stearic acid Zinc, 0.2 parts of antioxidant 168 and 0.6 parts of anti-crosslinking agent aniline are mixed uniformly in a high-speed mixer at a low speed, and then forced to feed in a twin-screw extruder at 180 ° C ~ 220 ° C, extruded and granulated, at 70 ° C Under drying for 4 hours to obtain the base material.
[0052] (2) Preparation of flame retardant masterbatch: dry treated 20 parts of ethylene-vinyl acetate copolymer, 7 parts of maleic anhydride grafted ethylene-vinyl acetate copolymer, 32.5 parts of triazine hyperbranched carbon former, 32.5 parts Melamine resin microencapsulated melamine polyphosphate, 5 parts of flame retardant synergist magnesi...
PUM
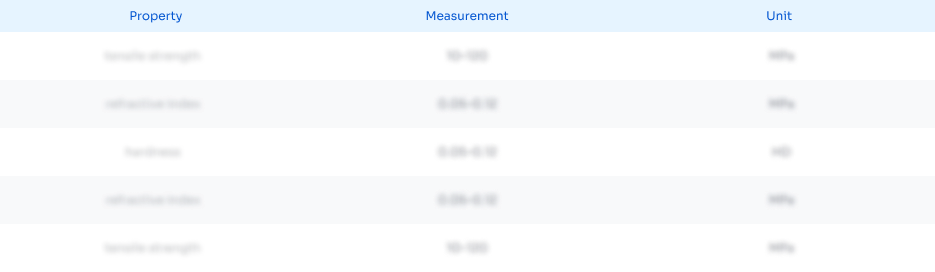
Abstract
Description
Claims
Application Information

- R&D
- Intellectual Property
- Life Sciences
- Materials
- Tech Scout
- Unparalleled Data Quality
- Higher Quality Content
- 60% Fewer Hallucinations
Browse by: Latest US Patents, China's latest patents, Technical Efficacy Thesaurus, Application Domain, Technology Topic, Popular Technical Reports.
© 2025 PatSnap. All rights reserved.Legal|Privacy policy|Modern Slavery Act Transparency Statement|Sitemap|About US| Contact US: help@patsnap.com