Copper and iron alloy for producing soldering bit and production technology thereof
A technology of copper-iron alloy and soldering iron tip, which is applied in the field of copper-iron alloy and its production process, can solve the problems of poor thermal conductivity of soldering iron tip, reduce work efficiency, increase production cost, etc., achieve smooth soldering, improve work efficiency, and prolong service life Effect
- Summary
- Abstract
- Description
- Claims
- Application Information
AI Technical Summary
Problems solved by technology
Method used
Image
Examples
Embodiment 1
[0050] Test items Soldering iron tip made of copper-iron alloy material (copper 47.35%, iron 52.65%) without electroplating Soldering iron tip made of traditional copper material plus electroplating method set temperature / actual temperature 360 degrees / 385 degrees 360 degrees / 352 degrees Oxidation time in 380-degree standby state 38 hours 2 hours Service life (number of solder joints under the same working conditions) 86,000 solder joints 35,000 solder joints Productivity 3216 welding spots / hour 1500 welding points / hour
[0051] The table shows that the weight percentages of copper and pure iron powder are 47.35%:52.65%, and the oxidation time of the finished soldering iron tip is 38 hours at 380°C.
[0052]
Embodiment 2
[0054] Test items Soldering iron tip made of copper-iron alloy material (copper 55.05%, iron 44.95%) without electroplating Soldering iron tip made of traditional copper material plus electroplating method set temperature / actual temperature 360 degrees / 405 degrees 360 degrees / 352 degrees Oxidation time in 380-degree standby state 43 hours 2 hours Service life (number of solder joints) 89,000 solder joints 35,000 solder joints Productivity 3511 solder joints / hour 1500 welding points / hour
[0055] The table shows that the weight percentages of copper and pure iron powder are 55.05%: 44.95%, and the oxidation time of the finished soldering iron tip is 43 hours at 380°C.
[0056]
Embodiment 3
[0058] Test items Soldering iron tip made of copper-iron alloy material (copper 63.15%, iron 36.85%) without electroplating Soldering iron tip made of traditional copper material plus electroplating method set temperature / actual temperature 360 degrees / 412 degrees 360 degrees / 352 degrees Oxidation time in 380-degree standby state 48 hours 2 hours Service life (number of solder joints) 92,000 solder joints 35,000 solder joints Productivity 3827 solder joints / hour 1500 welding points / hour
[0059] The table shows that the weight percentages of copper and pure iron powder are 63.15%: 36.85%, and the oxidation time of the finished soldering iron tip is 48 hours at 380°C.
[0060] According to the above three sets of experimental data, the soldering iron tip made of copper-iron alloy material without electroplating has improved thermal conductivity and prolonged oxidation time in standby state compared with the soldering iron tip ...
PUM
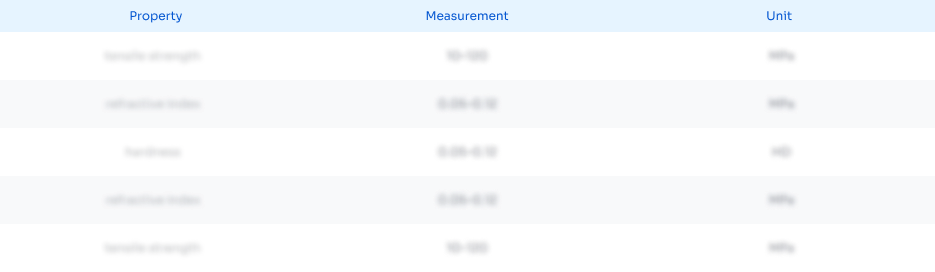
Abstract
Description
Claims
Application Information

- R&D
- Intellectual Property
- Life Sciences
- Materials
- Tech Scout
- Unparalleled Data Quality
- Higher Quality Content
- 60% Fewer Hallucinations
Browse by: Latest US Patents, China's latest patents, Technical Efficacy Thesaurus, Application Domain, Technology Topic, Popular Technical Reports.
© 2025 PatSnap. All rights reserved.Legal|Privacy policy|Modern Slavery Act Transparency Statement|Sitemap|About US| Contact US: help@patsnap.com