Preparation method of foam glass using waste glass, and prediction method of foaming range of glass using dilatometer
A foam glass and waste glass technology, applied in glass manufacturing equipment, glass molding, manufacturing tools, etc., can solve the problem that the glass foaming range cannot be accurately predicted, achieve process control and production method optimization, simplify the process, The effect of foaming temperature optimization
- Summary
- Abstract
- Description
- Claims
- Application Information
AI Technical Summary
Problems solved by technology
Method used
Image
Examples
Embodiment 1 to 4
[0080] Examples 1 to 4: Manufacturing cellular glass using waste glass
[0081] The waste glass having a sodium silicate component was first ground using a disc mill. Grinding was performed up to three times using the recirculation method. The primary milled powder thus obtained (average particle size 120 μm) was subjected to secondary wet milling (average particle size 2 μm) for 1 hour to 72 hours using a planetary mill in distilled water as a solvent at a speed of 100 rpm to 400 rpm.
[0082] The secondary ground powder was dried in an oven at 60°C for 24 hours. The dried powder was sifted through a 200 mesh sieve. The sieved powder thus obtained was placed in a forming mold as an unexpanded precursor, which was molded by pressing to prepare an unexpanded precursor. The unfoamed precursor was heated from room temperature to 700°C using an electric furnace at various heating rates of 1°C / min, 5°C / min, 10°C / min, and 20°C / min, and subjected to calcination and foaming proce...
Embodiment 5 to 8
[0086] Examples 5 to 8: Manufacturing of aesthetically pleasing cellular glass using waste glass
[0087] Examples 5 to 8 relate to colored foam glass obtained by coloring the foam glass of Examples 1 to 4 in a predetermined color. Specifically, waste glass having a sodium silicate component was primarily ground in the same manner as in Examples 1 to 4 using a disk grinder. 1wt% or 2wt% cobalt oxide (Co 3 o 4 ) or manganese oxide (MnO 3 ) was added to the primary ground powder thus obtained (average particle size of 120 μm), and then the mixture thus obtained was wet-milled for the second time in distilled water as a solvent at a speed of 200 rpm for 8 hours (average particle size of 2 μm) .
[0088] The secondary ground powder was dried in an oven at 60°C for 24 hours. The dried powder was sifted through a 200 mesh sieve. The sieved powder thus obtained was placed in a forming mold as an unexpanded precursor, which was molded by pressing to prepare an unexpanded precu...
Embodiment 9 to 12
[0095] Examples 9 to 12: Prediction of the expansion range of glass using a dilatometer
[0096] In order to predict the foaming range of foamed glass using a glass having a sodium silicate component, an unfoamed precursor was prepared by sieving powder and molding the powder using a forming die. The prepared unfoamed precursor was introduced into the dilatometer at various ramp rates of 1°C / min, 5°C / min, 10°C / min and 20°C / min as set forth in Table 3 (Example 9 To 12), the behavior of the cellular glass was observed in real time when a load of 25 cN was applied.
[0097] table 3
[0098]
Example 9
Example 10
Example 11
Example 12
Heating rate (℃ / min)
1
5
10
20
Load change (cN)
25
25
25
25
Cooling rate (℃ / min)
-
-
-
-
Hold time (min)
-
-
-
-
[0099] Figure 6 Shape change curves showing the shrinkage and expansion behavior of the unfoamed precursor a...
PUM
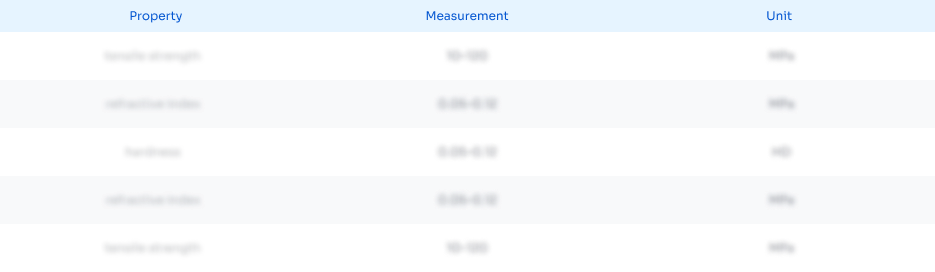
Abstract
Description
Claims
Application Information

- R&D
- Intellectual Property
- Life Sciences
- Materials
- Tech Scout
- Unparalleled Data Quality
- Higher Quality Content
- 60% Fewer Hallucinations
Browse by: Latest US Patents, China's latest patents, Technical Efficacy Thesaurus, Application Domain, Technology Topic, Popular Technical Reports.
© 2025 PatSnap. All rights reserved.Legal|Privacy policy|Modern Slavery Act Transparency Statement|Sitemap|About US| Contact US: help@patsnap.com