Metal oxide ceramic inert anode and preparation method and application thereof
A technology of oxide ceramics and inert anodes, which is applied in the field of oxide cermet inert anodes and its preparation, can solve problems such as inability to produce aluminum products, achieve low cost, good resistance to high temperature medium corrosion and oxidation, and good toughness and plasticity Effect
- Summary
- Abstract
- Description
- Claims
- Application Information
AI Technical Summary
Problems solved by technology
Method used
Image
Examples
Embodiment 1
[0043] The percentage composition of the inert anodic oxide ceramic phase is: Fe 2 o 3 : NiO : ZrO 2 :V 2 o 5 : CeO 2 : MgO=58.65wt% : 28.35wt% : 7wt% : 2wt% : 2wt% : 2wt%. The weight percent of oxide phase and metal phase is oxide: metal=75wt%: 25wt%. The metal phase is composed of five elements: Fe, Ni, Cu, Mn, and Y. The percentages of the five metals in the metal phase are Fe: Ni: Cu: Mn: Y=40wt%: 12.5wt%: 40.0wt%: 6wt %: 1.5wt%;
[0044] The preparation of the anode is carried out in the following seven steps,
[0045] Step 1: Weigh Fe in proportion (67.4wt%: 32.6wt%) 2 o 3 NiO powder and NiO powder are mixed evenly, put into a ceramic container and calcined at 960°C for 4 hours to form NiFe 2 o 3 Complex;
[0046] The second step: the calcined and cooled NiFe 2 o 3 Take out and weigh 7wt%ZrO by percentage 2 , 2wt%V 2 o 5 , 2wt%CeO 2 Mix with 2wt%MgO four kinds of powders, and then put it into a horizontal stirring high-energy ball mill for 20 hours ...
Embodiment 2
[0054] The percentage of inert anodic oxide ceramic phase is: Fe 2 o 3 : NiO : ZrO 2 :V 2 o 5 : CeO 2 : MgO=58.65wt% : 28.35wt% : 6.0wt% : 1.0wt% : 3.0wt% : 3.0wt%. The percentage composition of metal phase and oxide phase is: oxide: metal=80wt%: 20wt%. The metal phase is composed of Cu, Ni, Fe, Co, and Zn. The weight percentage of the five metal elements is: Cu: Fe: Ni: Co: Zn=42wt%: 35wt%: 12wt%: 6wt%: 5wt%;
[0055] The method and steps for preparing an inert anode are basically the same as in Example 1, except for the following three points: the first is that when calcination synthesizes spinel, the calcination temperature is 920 ° C, and the holding time is 6 hours; the second is pressing Figure 1 When the process flow is conventional ball milling for 12 hours, the modifier added is primary alcohol HO-R, and the addition amount is 0.5wt% of the material; in the last 2 hours of conventional ball milling, the binder added to the ball mill is polyethylene Acetat...
Embodiment 3
[0058] The percentage of the oxide ceramic phase and the total amount of metal in the inert anode is: ∑ oxide: ∑ metal=85wt%: 15wt%; the weight percentage of each oxide in the oxide phase is: Fe 2 o 3 : NiO : ZrO 2 :V 2 o 5 : CeO 2 : MgO=58.65wt% : 28.35wt% : 6.5wt% : 1.5wt% : 2.5wt% : 2.5wt%. The metal phase is composed of Fe, Cu, Ni, Cr, Ti, V six components. The weight percentage of each metal component is composed of: Fe: Cu: Ni: Cr: Ti: V=38wt%: 40wt%: 10wt%: 5wt%: 5wt%: 2wt%. All oxides and metals added are industrial grade micron coarse powder. The particle size of the powder is between 100 and 250 mesh;
[0059] The method and steps for preparing an inert anode are basically the same as in Example 1. The only difference is the following three points: first, when calcining synthetic spinel, the calcining temperature is 940°C, and the holding time is 5 hours; Figure 1 When the process is conventionally ball milled for 12 hours, the added nano-powder surface...
PUM
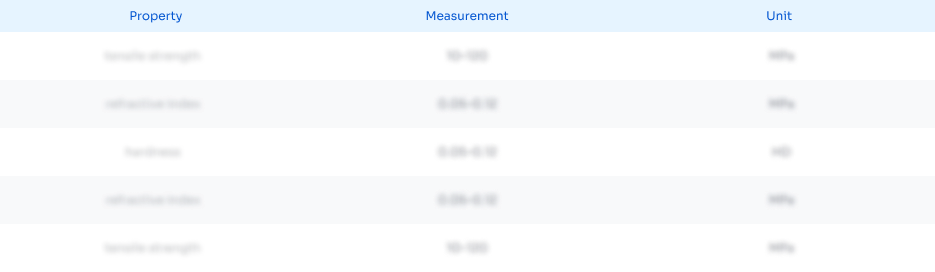
Abstract
Description
Claims
Application Information

- R&D Engineer
- R&D Manager
- IP Professional
- Industry Leading Data Capabilities
- Powerful AI technology
- Patent DNA Extraction
Browse by: Latest US Patents, China's latest patents, Technical Efficacy Thesaurus, Application Domain, Technology Topic, Popular Technical Reports.
© 2024 PatSnap. All rights reserved.Legal|Privacy policy|Modern Slavery Act Transparency Statement|Sitemap|About US| Contact US: help@patsnap.com