A high-temperature wear-resistant coating at a high temperature of 800 degrees and its preparation method
A high-temperature wear-resistant and coating technology, applied in the field of coatings, can solve the problems of insufficient temperature and corrosion resistance, large friction coefficient, etc., and achieve the effects of uniform particle size dispersion, increased high temperature resistance, and high whiteness.
- Summary
- Abstract
- Description
- Claims
- Application Information
AI Technical Summary
Problems solved by technology
Method used
Examples
Embodiment 1
[0041] This example provides a high-temperature wear-resistant coating at a high temperature of 800 degrees, which includes two components, A and B. A two-component composition is composed of components A and B mixed in a ratio of A:B=2:1. , A and B comprise the following components in parts by mass:
[0042] Component A in component A includes the following components in parts by mass: black silicon carbide: 30 parts, fine-grained alumina: 30 parts, hydrophobically modified carboxylic acid sodium salt: 6 parts, zinc oxide: 4 parts , epoxy acrylic resin: 15 parts, modified polyester acrylate: 5 parts, diluent: 10 parts, diluent generally choose ethyl acetate;
[0043] Component B in component A includes the following components in parts by mass: silicone modified epoxy resin: 50 parts, filler: graphite: 12 parts, molybdenum disulfide: 8 parts, talcum powder: 4 parts, three Antimony oxide: 10 parts, lauryl alcohol ester: 3 parts, dipropylene glycol butyl ether: 3 parts, diatom...
Embodiment 2
[0056] This example provides a high-temperature wear-resistant coating at a high temperature of 800 degrees, which includes two components, A and B. A two-component composition is composed of components A and B mixed in a ratio of A:B=2:1. , A and B comprise the following components in parts by mass:
[0057] Component A in component A includes the following components in parts by mass: black silicon carbide: 35 parts, fine-grained alumina: 23 parts, polyacrylic acid sodium salt: 10 parts, zinc oxide: 5 parts, bisphenol A Type epoxy resin: 13 parts, modified polyester acrylate: 6 parts, diluent: 8 parts, diluent generally choose ethyl acetate;
[0058] Component B in component A includes the following components in parts by mass: silicone modified epoxy resin: 51 parts, filler: graphite: 15 parts, molybdenum disulfide: 10 parts, talcum powder: 5 parts, three Antimony oxide: 5 parts, lauryl alcohol ester: 4 parts, dipropylene glycol butyl ether: 4 parts, diatomaceous earth: 3 ...
Embodiment 3
[0071] This example provides a high-temperature wear-resistant coating at a high temperature of 800 degrees, which includes two components, A and B. A two-component composition is composed of components A and B mixed in a ratio of A:B=2:1. , A and B comprise the following components in parts by mass:
[0072] Component A in component A includes the following components in parts by mass: black silicon carbide: 33 parts, fine-grained alumina: 28 parts, polyacrylic acid sodium salt: 9 parts, zinc oxide: 3 parts, bisphenol A Type epoxy resin: 14 parts, modified polyester acrylate: 4 parts, diluent: 9 parts, diluent generally choose ethyl acetate;
[0073] Component B in component A includes the following components in parts by mass: silicone modified epoxy resin: 51 parts, filler: graphite: 13.5 parts, molybdenum disulfide: 9 parts, talcum powder: 4.5 parts, three Antimony oxide: 6 parts, lauryl alcohol ester: 4 parts, dipropylene glycol butyl ether: 4 parts, diatomaceous earth: ...
PUM
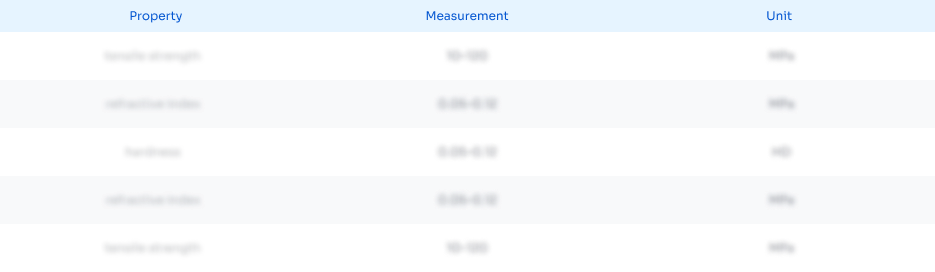
Abstract
Description
Claims
Application Information

- Generate Ideas
- Intellectual Property
- Life Sciences
- Materials
- Tech Scout
- Unparalleled Data Quality
- Higher Quality Content
- 60% Fewer Hallucinations
Browse by: Latest US Patents, China's latest patents, Technical Efficacy Thesaurus, Application Domain, Technology Topic, Popular Technical Reports.
© 2025 PatSnap. All rights reserved.Legal|Privacy policy|Modern Slavery Act Transparency Statement|Sitemap|About US| Contact US: help@patsnap.com