Mg-Cu grain boundary modified high-magnetism sintered Nd-Fe-B magnet and preparation process thereof
A grain boundary modification, NdFeB technology, applied in the direction of magnetic objects, inductance/transformer/magnet manufacturing, magnetic materials, etc., can solve unsatisfactory problems, achieve low material cost, clear grain boundaries, and high comprehensive magnetic properties Effect
- Summary
- Abstract
- Description
- Claims
- Application Information
AI Technical Summary
Problems solved by technology
Method used
Image
Examples
Embodiment 1
[0018] (1) Smelting: the main alloy and auxiliary alloy are prepared separately, the main alloy Nd 11.2 PR 2.3 Fe 80.6 B 5.9 After batching according to the chemical ratio, put it into the vacuum melting furnace, and pump the air in the furnace to 10 -3 After Pa, start heating and smelting, and carry out quick-setting flakes through a copper roller (surface linear velocity 1.8m / s), to obtain 0.25-0.35mm thick flakes; auxiliary alloy Mg 85.5 Cu 14.5 Put the ingredients into the vacuum induction furnace after proportioning, and pump the air in the furnace to 10 -3 After Pa, start heating and smelting. When the ingredients in the furnace are red, close the vacuum valve, fill with argon, and pour after the materials are melted to prepare auxiliary alloy ingots.
[0019] (2) Milling and powder mixing: the main alloy and the auxiliary alloy are milled separately, and the main alloy Nd 11.2 PR 2.3 Fe 80.6 B 5.9 The quick-setting flakes, after the hydrogen explosion (HD) proc...
Embodiment 2
[0029] (1) Smelting: the main alloy and auxiliary alloy are prepared separately, the main phase alloy Nd 12.2 La 1.0 Fe 80.7 B 6.1 After batching according to the chemical ratio, put it into the vacuum melting furnace, and pump the air in the furnace to 10 -3 After Pa, start heating and smelting, and carry out quick-setting flakes through copper rollers (surface line speed 1.8m / s), to obtain flakes with a thickness of 0.25-0.35mm; auxiliary alloy Mg 83.5 Cu 16.5 Put the ingredients into the vacuum induction furnace after proportioning, and pump the air in the furnace to 10 -3 After Pa, start heating and smelting. When the ingredients in the furnace are red, close the vacuum valve, fill with argon, and pour after the materials are melted to prepare auxiliary alloy ingots.
[0030] (2) Milling and powder mixing: the main alloy and the auxiliary alloy are milled separately, and the main alloy Nd 12.2 La 1.0 Fe 80.7 B 6.1 The quick-setting flakes, after the hydrogen explo...
Embodiment 3
[0040] (1) Smelting: the main alloy and auxiliary alloy are prepared separately, the main phase alloy Nd 12.1 PR 1.7 La 1.0 Fe 79.2 B 6.0 After batching according to the chemical ratio, put it into the vacuum melting furnace, and pump the air in the furnace to 10 -3 After Pa, start heating and smelting, and carry out quick-setting flakes through copper rollers (surface line speed 1.8m / s), to obtain flakes with a thickness of 0.25-0.35mm; auxiliary alloy Mg 80.0 Cu 20.0 Put the ingredients into the vacuum induction furnace after proportioning, and pump the air in the furnace to 10 -3 After Pa, start heating and smelting. When the ingredients in the furnace are red, close the vacuum valve, fill with argon, and pour after the materials are melted to prepare auxiliary alloy ingots.
[0041] (2) Milling and powder mixing: the main alloy and the auxiliary alloy are milled separately, and the main alloy Nd 12.1 PR 1.7 La 1.0 Fe 79.2 B 6.0 The quick-setting flakes, after th...
PUM
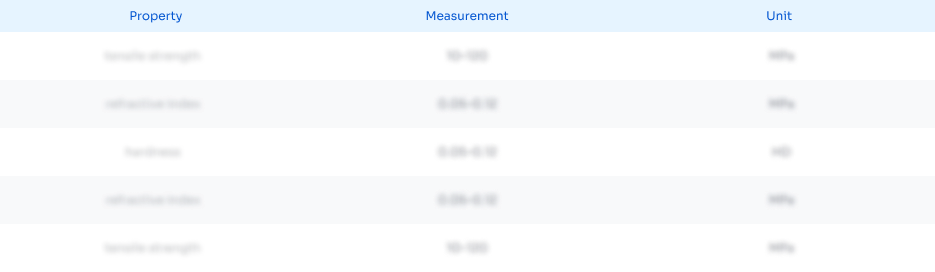
Abstract
Description
Claims
Application Information

- Generate Ideas
- Intellectual Property
- Life Sciences
- Materials
- Tech Scout
- Unparalleled Data Quality
- Higher Quality Content
- 60% Fewer Hallucinations
Browse by: Latest US Patents, China's latest patents, Technical Efficacy Thesaurus, Application Domain, Technology Topic, Popular Technical Reports.
© 2025 PatSnap. All rights reserved.Legal|Privacy policy|Modern Slavery Act Transparency Statement|Sitemap|About US| Contact US: help@patsnap.com