Electrolytic Copper Foil Copper-Based Polymer Material Composite Plating Process
A polymer material and electrolytic copper foil technology, applied in electrolytic organic material coating, etc., can solve the problems of increased production difficulty, yield restriction, low roughness, etc., and achieve high product yield, good consistency, and high Tg value Effect
- Summary
- Abstract
- Description
- Claims
- Application Information
AI Technical Summary
Problems solved by technology
Method used
Examples
Embodiment 1
[0070] Cu 2+ Concentration: 18~20g / l
[0071] h 2 SO 4 Concentration: 50~55g / l
[0072] A concentration: 0.35g / l, 3,5-dimethyl-octene
[0073] B concentration: 20mg / l, ethylenediamine; 35mg / l, alkyl dithioamino acid ester
[0074] Temperature: 27°C
[0075] Current density: 270A / m 2
[0076] Auxiliary pulse power supply: current density 50A / m 2 , pulse frequency 20Hz, one-way half-wave positive pulse
[0077] Solution flow: 2m 3 / h
[0078] Processing time: 25 seconds
[0079] According to the above settings in this embodiment, the whole process takes a long time, the current density is small, the crystallization of the coating is fine, and better adhesion between organic matter and copper foil can be obtained, and the concentration and composition of A or B can be accurately controlled according to user needs. Peel strength of copper foil and smooth surface roughness of copper foil.
Embodiment 2
[0081] Cu 2+ Concentration: 40~45g / l
[0082] h 2 SO 4 Concentration: 80~90g / l
[0083] A concentration: 0.7~0.8g / l, polyacrylamide, molecular weight 300~500
[0084] B concentration: 20mg / l, ethylenediamine; 35mg / l, alkyl dithioamino acid ester
[0085] Temperature: 50~55℃
[0086] Current density: 750A / m 2
[0087] Auxiliary pulse power supply: current density 100A / m 2 , pulse frequency 50Hz, positive full wave, negative half wave pulse
[0088] Solution flow: 5m 3 / h
[0089] Processing time: 5 seconds
[0090] In this embodiment, according to the above settings, the whole processing time is short and the speed is fast, which can not only obtain an ideal coating but also meet the actual production requirements of copper foil.
PUM
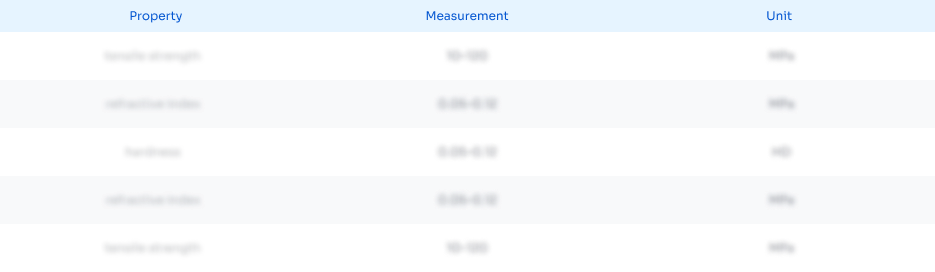
Abstract
Description
Claims
Application Information

- R&D
- Intellectual Property
- Life Sciences
- Materials
- Tech Scout
- Unparalleled Data Quality
- Higher Quality Content
- 60% Fewer Hallucinations
Browse by: Latest US Patents, China's latest patents, Technical Efficacy Thesaurus, Application Domain, Technology Topic, Popular Technical Reports.
© 2025 PatSnap. All rights reserved.Legal|Privacy policy|Modern Slavery Act Transparency Statement|Sitemap|About US| Contact US: help@patsnap.com