A processing technology of building thermal insulation aluminum alloy foil
A technology of aluminum alloy foil and processing technology, which is applied in the field of processing technology of aluminum alloy foil, can solve the problems that the corrosion resistance is difficult to reach the service life of buildings, the heat absorption capacity of aluminum metal foil is limited, and waste of energy and time is achieved. Improve heat treatment efficiency, improve toughness and corrosion resistance, and save energy
- Summary
- Abstract
- Description
- Claims
- Application Information
AI Technical Summary
Problems solved by technology
Method used
Examples
preparation example Construction
[0024] Below the preparation method of the present invention is described in further detail, and it comprises the following steps:
[0025] First, the raw material components are sent into the electric melting furnace according to the proportion, the heating temperature in the furnace is 750--800°C, and the heating time is 2--3h, so that the components become a melt, and the mass ratio of the raw material components is : 0.5%-0.6% magnesium, 0.3%-0.4% silicon, 0.6%-0.8% manganese, 0.01%-0.05% copper, 0.01%-0.05% chromium, and the rest is aluminum; In the implementation process, although the temperature has not reached the melting point of chromium, due to the small amount of addition, it will not affect its performance; then the melt is emulsified by an emulsifier at a constant temperature for 1-2 hours, and the temperature is best kept at 700 ° C , so as to form a uniform mixture; then the mixture is cast and rolled into a green body, and the green body is pre-annealed at a t...
Embodiment 1
[0028] Send 0.5% magnesium, 0.3% silicon, 0.6% manganese, 0.01% copper, 0.01% chromium, and 98.58% aluminum into the electric melting furnace, and adjust the temperature in the electric melting furnace to 750°C. After keeping warm for 2 hours, the raw material in the electric melting furnace becomes a melt, and then the melt is kept warm and sent to an emulsifier at 700°C for emulsification. After about 1 hour, the mixture is cast and rolled into a green body, and the green body is heated at a temperature of 450 Annealing treatment under the condition of ℃, cold rolling the annealed green body, using the cold rolling temperature of 250 ℃ to obtain a 3.5mm aluminum alloy strip, pressing and winding the strip foil, and then rolling the obtained aluminum alloy foil Put it in the annealing furnace, and conduct heat treatment in the preheating zone with a temperature of 100°C, the heating zone with a heating rate of 50°C / h, the holding zone at a temperature of 400°C, and the cooling...
Embodiment 2
[0030] Feed 0.55% magnesium, 0.35% silicon, 0.7% manganese, 0.02% copper, 0.03% chromium, and 98.35% aluminum into the electric melting furnace, and adjust the temperature in the electric melting furnace to 780°C. After 2.5 hours of heat preservation, the raw material in the electric melting furnace becomes a melt, and then the melt is kept warm and sent to an emulsifier at 700°C for emulsification. After about 1.5 hours, the mixture is cast and rolled into a green body, and the green body is heated at temperature For annealing treatment at 470°C, cold-roll the annealed billet at a temperature of 250-350°C to obtain aluminum alloy strips of 3.5-4.5 mm, and foil-press and coil the strips. Then put the obtained aluminum alloy foil coil in the annealing furnace, and successively in the preheating zone with a temperature of 150°C, the heating zone with a heating rate of 100°C / h, the holding zone with a temperature of 420°C and the cooling zone with a cooling rate of 100°C / h. Heat ...
PUM
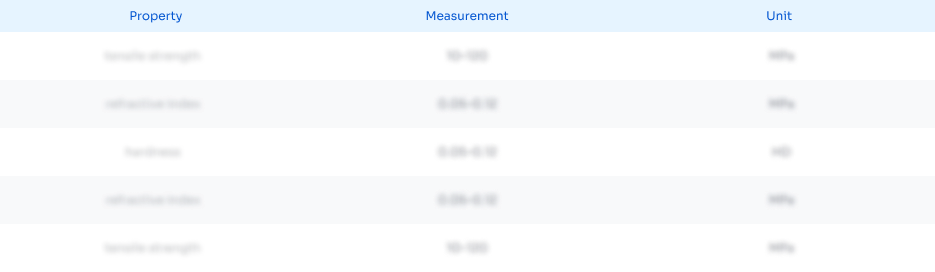
Abstract
Description
Claims
Application Information

- R&D
- Intellectual Property
- Life Sciences
- Materials
- Tech Scout
- Unparalleled Data Quality
- Higher Quality Content
- 60% Fewer Hallucinations
Browse by: Latest US Patents, China's latest patents, Technical Efficacy Thesaurus, Application Domain, Technology Topic, Popular Technical Reports.
© 2025 PatSnap. All rights reserved.Legal|Privacy policy|Modern Slavery Act Transparency Statement|Sitemap|About US| Contact US: help@patsnap.com