Modified alcohol-base foundry coating and preparation method thereof
A casting coating, alcohol-based technology, applied in casting molding equipment, coatings, molds, etc., can solve the problems of poor suspension of attapulgite and low suspension of alcohol-based coatings, and improve the suspension and bond strength. No hardening, smooth and dense coating
- Summary
- Abstract
- Description
- Claims
- Application Information
AI Technical Summary
Problems solved by technology
Method used
Examples
preparation example Construction
[0018] A preparation method for a modified alcohol-based casting coating, comprising the steps of:
[0019] 1) Prepare the above-mentioned modified alcohol-based casting coating;
[0020] 2) Disperse the gas-phase nano additives, phenolic resin, polyvinyl butyrate and additives into the zircon powder, add water to fully dissolve the solution, then disperse the suspending agent into the solution, and finally add the defoamer to carry out Stir to form a colloid; the dispersion time of the suspending agent is 15 minutes to ensure good thixotropy and suspension; the stirring speed is 1000r / min, and the stirring time is 1h;
[0021] 3) Put the colloid in the drum of the ball mill, and discharge it after grinding.
Embodiment 1
[0023] A modified alcohol-based casting coating, which comprises 75% zircon powder by weight, 1% gas-phase nano additives, 2% polyvinyl butyrate, 4% suspending agent, and 1% phenolic resin , and the rest are additives, and then take 0.01% of the mass percentage of the modified alcohol-based casting coating as a defoamer for preparation, and the defoamer is n-butanol. In the present invention, the suspending agent is uniformly mixed with 40% TM-MA composite reagent and 10% alcohol by weight ratio, and 50% attapulgite is added to the ultrasonic generator, stirred and shaken for 1h and left to stand for 30min, after 70 °C dried. In the modified alcohol-based casting coating prepared above, disperse the gas-phase nano additives, phenolic resin, polyvinyl butyrate and additives into the zircon powder, add water to fully dissolve to obtain a solution, and then disperse the suspending agent into the solution After dispersing for 15 minutes, finally add defoamer and stir to form a co...
Embodiment 2
[0025] A modified alcohol-based casting coating, which comprises 85% zircon powder by weight, 2% gas-phase nano additives, 3% polyvinyl butyrate, 6% suspending agent, and 2% phenolic resin , and the rest are additives, and then take 0.02% of the mass percentage of the modified alcohol-based casting coating as a defoamer for preparation, and the defoamer is n-amyl alcohol. In the present invention, the suspending agent is uniformly mixed with 40% TM-MA composite reagent and 10% alcohol by weight ratio, and 50% attapulgite is added to the ultrasonic generator, stirred and shaken for 1h and left to stand for 30min, after 70 °C dried. In the modified alcohol-based casting coating prepared above, disperse the gas-phase nano additives, phenolic resin, polyvinyl butyrate and additives into the zircon powder, add water to fully dissolve to obtain a solution, and then disperse the suspending agent into the solution After dispersing for 15 minutes, finally add defoamer and stir to form...
PUM
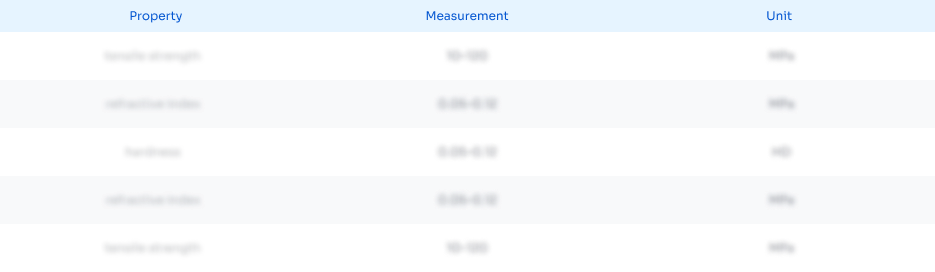
Abstract
Description
Claims
Application Information

- R&D
- Intellectual Property
- Life Sciences
- Materials
- Tech Scout
- Unparalleled Data Quality
- Higher Quality Content
- 60% Fewer Hallucinations
Browse by: Latest US Patents, China's latest patents, Technical Efficacy Thesaurus, Application Domain, Technology Topic, Popular Technical Reports.
© 2025 PatSnap. All rights reserved.Legal|Privacy policy|Modern Slavery Act Transparency Statement|Sitemap|About US| Contact US: help@patsnap.com