Wear-resistant halogen-free flame-retardant cable material
A flame-retardant cable material, wear-resistant technology, used in plastic/resin/wax insulators, organic insulators, etc., can solve the problem of poor weather resistance, affecting the physical and mechanical properties and processing performance of cable materials, and low temperature resistance. and other problems to achieve the effect of improving wear resistance
- Summary
- Abstract
- Description
- Claims
- Application Information
AI Technical Summary
Problems solved by technology
Method used
Image
Examples
Embodiment Construction
[0012] Wear-resistant halogen-free flame-retardant cable compound, made of raw materials with the following weight (kg):
[0013] 25 parts of polyurethane, 70 parts of methyl vinyl silicone rubber, 15 parts of nitrile rubber, 9 parts of magnesium hydroxide, 0.6 parts of butyl stearate, 2 parts of barium stearate, triethylene glycol diisocaprylate 10 parts, 5 parts of copper oxide, 0.8 parts of molybdenum trioxide, 40 parts of fumed silica, 12 parts of nano-calcium carbonate, 0.8 parts of anti-aging agent, 0.2 parts of anti-aging agent AW, 0.8 parts of accelerator NOBS, vulcanizing agent DCBP0 .4. Triphenyl phosphate 9, antimony trioxide 14, zinc borate hydrate 7.
[0014] Preparation:
[0015] Weigh the raw materials of each component according to the proportion of the formula, stir the weighed raw materials in a high-speed mixer, and then banbury with an internal mixer at a temperature range of 142-168 ° C, extrude with twin-screws, and grind the surface eagerly Granulating...
PUM
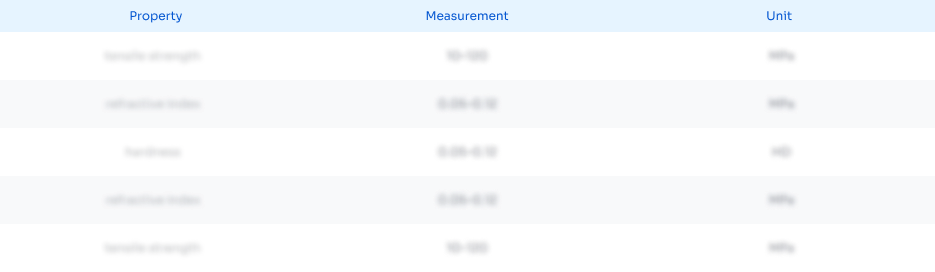
Abstract
Description
Claims
Application Information

- Generate Ideas
- Intellectual Property
- Life Sciences
- Materials
- Tech Scout
- Unparalleled Data Quality
- Higher Quality Content
- 60% Fewer Hallucinations
Browse by: Latest US Patents, China's latest patents, Technical Efficacy Thesaurus, Application Domain, Technology Topic, Popular Technical Reports.
© 2025 PatSnap. All rights reserved.Legal|Privacy policy|Modern Slavery Act Transparency Statement|Sitemap|About US| Contact US: help@patsnap.com