Method for preparing anti-scratch coating material for solar cell backplanes
A technology of solar cells and coating materials, applied in the direction of coating, etc., can solve the problems of poor film adhesion or interlayer bonding, increase coating cost, peeling, etc., achieve good weather resistance and scratch resistance, reduce Effect of surface energy, good hydrophobicity
- Summary
- Abstract
- Description
- Claims
- Application Information
AI Technical Summary
Problems solved by technology
Method used
Examples
Embodiment 1
[0016] Add the mixed solution made of styrene 20g, butyl acrylate 18g, hydroxypropyl acrylate 25g, undecylenic acid 8g, benzoyl peroxide 3g and 30g toluene solvent into a four-necked flask with stirrer, thermometer and reflux tube In the medium, stir under normal pressure and heat up to 82°C, then add 30g of dodecafluoroheptyl methacrylate, 20g of tetrafluoropropyl methacrylate, 10g of low molecular weight bisphenol A epoxy resin and 35g of toluene dropwise at a constant speed. The mixed solution was added in 40 minutes. After the addition, 1 g of benzoyl peroxide was added after the heat preservation reaction for 2 hours, and the heat preservation reaction was continued for 3 hours. The reaction was stopped, and the product P1 was obtained after cooling to room temperature and discharging.
Embodiment 2
[0018] Add 16g of styrene, 14g of butyl acrylate, 16g of hydroxypropyl acrylate, 10g of 2-ethylhexyl acrylate, 5g of acrylic acid, 3g of benzoyl peroxide and 40g of toluene into a mixed solution with a stirrer, a thermometer, In the four-necked flask of the reflux tube, stir under normal pressure and heat up to 85 ° C, then add 25 g of dodecafluoroheptyl methacrylate, 12 g of tetrafluoropropyl methacrylate, and low molecular weight bisphenol A epoxy resin dropwise at a constant speed. Add the mixed solution of 8g and 50g toluene in 40 minutes, add 1g of benzoyl peroxide after 2 hours of heat preservation reaction, keep heat temperature for 3 hours, stop the reaction, cool to room temperature and discharge to obtain product P2.
Embodiment 3
[0020] Add 12g of styrene, 20g of 2-ethylhexyl acrylate, 22g of hydroxypropyl acrylate, 6g of methacrylic acid, 2g of azobisisobutyronitrile and 45g of propylene glycol propyl ether into a mixed solution with a stirrer, a thermometer, In the four-necked flask of the reflux tube, stir under normal pressure and heat up to 80 ° C, then add 20 g of dodecafluoroheptyl methacrylate, 16 g of tetrafluoropropyl methacrylate, and 6 g of low molecular weight bisphenol A epoxy resin dropwise at a constant speed. The mixed solution made with 50g propylene glycol propyl ether was added in 40 minutes. After the addition, 1g of azobisisobutyronitrile was added after the heat preservation reaction for 2 hours, and the heat preservation reaction was continued for 3 hours. The reaction was stopped, and the product P3 was obtained after cooling to room temperature.
[0021]
PUM
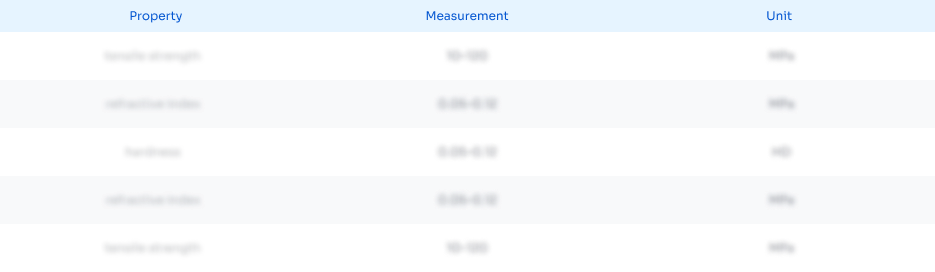
Abstract
Description
Claims
Application Information

- Generate Ideas
- Intellectual Property
- Life Sciences
- Materials
- Tech Scout
- Unparalleled Data Quality
- Higher Quality Content
- 60% Fewer Hallucinations
Browse by: Latest US Patents, China's latest patents, Technical Efficacy Thesaurus, Application Domain, Technology Topic, Popular Technical Reports.
© 2025 PatSnap. All rights reserved.Legal|Privacy policy|Modern Slavery Act Transparency Statement|Sitemap|About US| Contact US: help@patsnap.com