Preparation technology for gradient composite wear-resistant conical liner plate
A preparation process and cone technology, which is applied in the field of preparation technology of gradient composite wear-resistant conical lining plates, can solve the problems of limited wear resistance, insufficient hardening ability, limited application scope, etc., so as to improve wear performance, ensure overall mechanical properties, simple craftsmanship
- Summary
- Abstract
- Description
- Claims
- Application Information
AI Technical Summary
Problems solved by technology
Method used
Examples
preparation example Construction
[0023] A preparation process for a gradient composite wear-resistant conical liner, said process comprising the following steps:
[0024] (1) Preparation of composite metal particle coating
[0025] a. Preparation of inner composite metal particle coating: 5% to 40% ferrochrome, 10% to 30% ferrovanadium, 35% to 75% iron powder, 1% to 3% carbon powder, 0% ~5% ferromolybdenum and 0%~10% ferro-tungsten are crushed separately, mixed and passed through a 200-300 mesh sieve to obtain the inner layer mixed powder, then add borax and NaF to the inner layer mixed powder for mechanical blending 8-12 hours, after fully mixing, add resin, make a slurry to get the inner layer composite metal particle coating, and set aside;
[0026] Wherein, the add-on of borax is 2~4% of inner layer mixed powder weight, the add-on of NaF is 1~3% of inner layer mixed powder weight, the add-on of resin is 5~4% of inner layer mixed powder weight. 10%;
[0027] b. Preparation of interlayer composite metal ...
Embodiment 1
[0041] A preparation process for a gradient composite wear-resistant conical liner, said process comprising the following steps:
[0042] (1) Preparation of composite metal particle coating
[0043] a. Preparation of inner layer composite metal particle coating: take 5% ferrochromium, 10% ferrovanadium, 72% iron powder, 1% carbon powder, 2% ferromolybdenum and 10% ferrotungsten according to mass percentage, and pulverize them respectively Mix and pass through a 200-300 mesh sieve to obtain a mixed powder, then add borax with a weight of 2% of the mixed powder and NaF with a weight of 1% of the mixed powder to the mixed powder, and perform mechanical blending for 8 hours. Add the furan resin of 8% by weight of the mixed powder, adjust it into a slurry to obtain the inner layer composite metal particle coating, and set aside;
[0044] b. Preparation of interlayer composite metal particle coating: take 5% ferrochrome, 30% ferrovanadium, 50% iron powder, 3% carbon powder, 2% ferr...
Embodiment 2
[0054] A preparation process for a gradient composite wear-resistant conical liner, said process comprising the following steps:
[0055] (1) Preparation of composite metal particle coating
[0056] a. Preparation of inner layer composite metal particle coating: take 25% ferrochromium, 15% ferrovanadium, 55% iron powder, 2% carbon powder and 3% ferromolybdenum according to the mass percentage, grind them respectively and mix them for 200~ 300 mesh sieves to obtain the mixed powder, then add borax with 2% mixed powder weight and 1% NaF with mixed powder weight in the mixed powder, carry out mechanical blending for 8 hours, add mixed powder weight after fully mixing 8% furan resin is adjusted into a slurry to obtain the inner layer composite metal particle coating, which is for subsequent use;
[0057] b. Preparation of interlayer composite metal particle coating: Take 25% ferrochromium, 25% ferrovanadium, 36.5% iron powder, 3.5% carbon powder, 5% ferromolybdenum and 5% ferrotu...
PUM
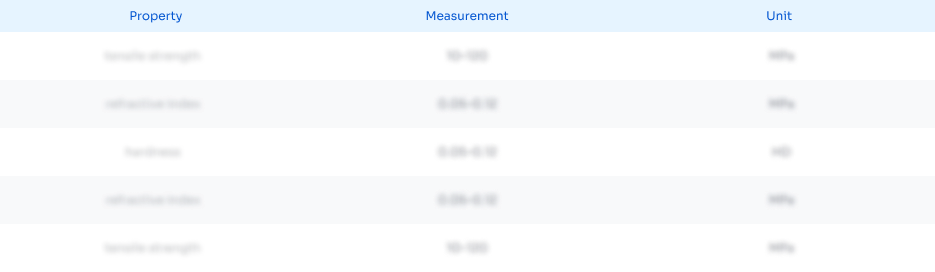
Abstract
Description
Claims
Application Information

- R&D Engineer
- R&D Manager
- IP Professional
- Industry Leading Data Capabilities
- Powerful AI technology
- Patent DNA Extraction
Browse by: Latest US Patents, China's latest patents, Technical Efficacy Thesaurus, Application Domain, Technology Topic, Popular Technical Reports.
© 2024 PatSnap. All rights reserved.Legal|Privacy policy|Modern Slavery Act Transparency Statement|Sitemap|About US| Contact US: help@patsnap.com