Preparation method for short carbon fiber/silicon carbide composites
A technology of chopped carbon fiber and composite material, which is applied in the field of fiber-reinforced composite material preparation, can solve the problems of difficult to widely use composite materials, complex preparation process, high technical difficulty, etc., and achieves high hardness, simple preparation process, and operability. strong effect
- Summary
- Abstract
- Description
- Claims
- Application Information
AI Technical Summary
Problems solved by technology
Method used
Image
Examples
Embodiment 1
[0023] 1. First, heat the heat treatment furnace to 400°C, put 0.5mm chopped carbon fiber in it, keep it warm for 30 minutes, take it out and cool it to room temperature, and then use the coarsening solution consisting of nitric acid, potassium dichromate, hydrogen peroxide and ammonium persulfate to soak After 24 hours of coarsening, wash and dry with deionized water for later use;
[0024] 2. According to 100 parts by mass, weigh 10 parts of chopped carbon fiber, 80 parts of silicon carbide micropowder, and 10 parts of sintering aid into the nylon ball ink tank, add silicon carbide grinding balls according to the ratio of 2:1 ball to material, and add Anhydrous ethanol is used as the dispersion medium, and the total volume of balls, materials and ethanol accounts for 2 / 3 of the volume of the ball mill tank;
[0025] 3. Seal the ball mill pot and place it on a high-energy ball mill for ball milling, the ball milling speed is 300r / min, and the time is 2h;
[0026] 4. After th...
Embodiment 2
[0029] 1. First, heat the heat treatment furnace to 400°C, put 1mm chopped carbon fiber in it, keep it warm for 30 minutes, take it out and cool it to room temperature, and then use the coarsening solution consisting of nitric acid, potassium dichromate, hydrogen peroxide and ammonium persulfate to soak for 24 hours After coarsening, wash and dry with deionized water for later use;
[0030] 2. According to 100 parts by mass, weigh 20 parts of chopped carbon fiber, 70 parts of silicon carbide micropowder, and 10 parts of sintering aid into the nylon ball ink tank, add silicon carbide grinding balls according to the ball-to-material ratio of 3:1, and add Anhydrous ethanol is used as the dispersion medium, and the total volume of balls, materials and ethanol accounts for 2 / 3 of the volume of the ball mill tank;
[0031] 3. Seal the ball mill pot and place it on a high-energy ball mill for ball milling, the ball milling speed is 300r / min, and the time is 2h;
[0032] 4. After the...
Embodiment 3
[0035] 1. First, heat the heat treatment furnace to 400°C, put 2mm chopped carbon fibers in it, keep it warm for 30 minutes, take it out and cool it to room temperature, and then use the coarsening solution consisting of nitric acid, potassium dichromate, hydrogen peroxide and ammonium persulfate to soak for 24 hours After coarsening, wash and dry with deionized water for later use;
[0036] 2. According to 100 parts by mass, weigh 30 parts of chopped carbon fiber, 60 parts of silicon carbide micropowder, and 10 parts of sintering aid into the nylon ball ink tank, add silicon carbide grinding balls according to the ratio of 4:1 ball to material, and add Anhydrous ethanol is used as the dispersion medium, and the total volume of balls, materials and ethanol accounts for 2 / 3 of the volume of the ball mill tank;
[0037] 3. Seal the ball mill pot and place it on a high-energy ball mill for ball milling, the ball milling speed is 300r / min, and the time is 4h;
[0038] 4. After th...
PUM
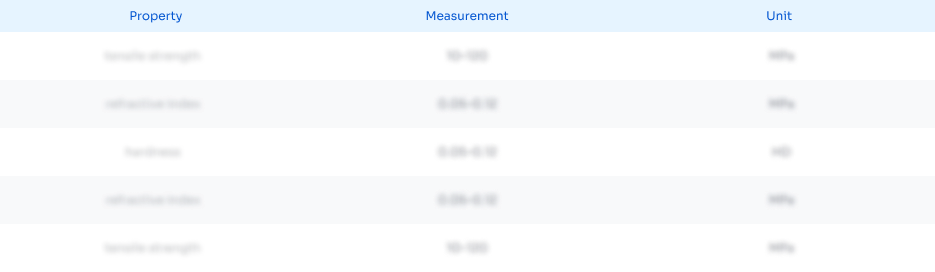
Abstract
Description
Claims
Application Information

- Generate Ideas
- Intellectual Property
- Life Sciences
- Materials
- Tech Scout
- Unparalleled Data Quality
- Higher Quality Content
- 60% Fewer Hallucinations
Browse by: Latest US Patents, China's latest patents, Technical Efficacy Thesaurus, Application Domain, Technology Topic, Popular Technical Reports.
© 2025 PatSnap. All rights reserved.Legal|Privacy policy|Modern Slavery Act Transparency Statement|Sitemap|About US| Contact US: help@patsnap.com