A kind of high-strength aluminum alloy treated with nickel carbide and its preparation method
A high-strength, nickel carbide technology, applied in the field of aluminum alloy materials and their high-quality treatment
- Summary
- Abstract
- Description
- Claims
- Application Information
AI Technical Summary
Problems solved by technology
Method used
Examples
Embodiment 1
[0021] Step one, select a group of elements according to the formula, by weight ratio: the alloy composition is Cu: 3.0%, Mg: 0.45%, Zn: 1.25%, modifier NiC- 3 0.1% of the total mass of the charge, the rest is Al and inevitable trace impurities, of which the inevitable trace impurities, Si and Fe are all impurities brought from the raw materials, and Si: ≤0.5%, Fe: ≤0.5% ; The total amount of the alloy prepared is 1000kg, then the weight of each substance required is calculated as: Cu: 300kg, Mg: 4.5kg, Zn: 12.5kg, NiC- modifier 3 : 1kg, Al: 982.0kg;
[0022] Step 2: First add aluminum ingot or molten aluminum to the smelting furnace, heat to melt it completely, add the alloy elements selected in step 1 according to the formula ratio, to completely dissolve and melt them, after refining, at 700~1000℃ Insulation; the melting process is completed in a closed environment;
[0023] Step 3: Use a mixed gas of nitrogen and argon (V / V1:1), add a small amount of chlorine (volume ratio: 1%)...
Embodiment 2
[0025] Step one, select a group of elements according to the formula, in terms of weight ratio: the alloy composition is Cu: 3.1%, Mn: 0.05%, Mg: 0.475, Cr: 0.005%, Zn: 1.25%, Ti: 0.05%, deterioration NiC- 3 0.075% of the total mass of the charge, the rest is Al and inevitable trace impurities, of which the inevitable trace impurities, Si and Fe are all impurities brought from the raw materials, and Si: ≤0.5%, Fe: ≤0.5% ; The total amount of the prepared alloy is 1000kg, and the weight of each substance required is calculated as: Cu: 31kg, Mn: 0.5kg, Mg: 4.75kg, Cr: 0.05kg, Zn: 12.5kg, Ti: 0.5kg , Modifier NiC- 3 : 0.75kg, Al: 950.0kg;;
[0026] Step 2: First add aluminum ingot or molten aluminum to the smelting furnace, heat to melt it completely, add the alloy elements selected in step 1 according to the formula ratio, to completely dissolve and melt them, after refining, at 700~1000℃ Insulation; the melting process is completed in a closed environment;
[0027] Step 3: Use a m...
Embodiment 3
[0029] Step one, select a group of elements according to the formula, by weight ratio: the alloy composition is Cu: 3.2%, Mn: 0.1%, Mg: 0.5%, Cr: 0.01%, Zn: 1.5%, Ti: 0.1%, Modifier NiC- 3 0.1% of the total mass of the charge, the rest is Al and inevitable trace impurities, of which the inevitable trace impurities, Si and Fe are all impurities brought from the raw materials, and Si: ≤0.5%, Fe: ≤0.5% ; The total amount of the alloy prepared is 1000kg, and the weight of each substance required is calculated as: Cu: 32kg, Mn: 1kg, Mg: 5kg, Cr: 0.1kg, Zn: 15kg, Ti: 1kg, NiC- 3 :1kg, Al: 944.9kg;
[0030] Step 2: First add aluminum ingot or molten aluminum to the smelting furnace, heat to melt it completely, add the alloy elements selected in step 1 according to the formula ratio, to completely dissolve and melt them, after refining, at 700~1000℃ Insulation; the melting process is completed in a closed environment;
[0031] Step 3: Use a mixed gas of nitrogen and argon (V / V1:1), add a ...
PUM
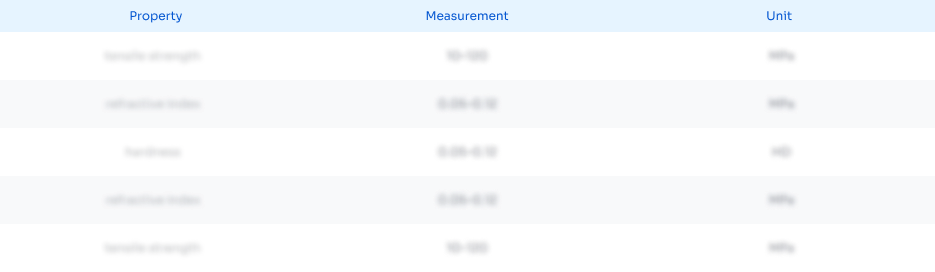
Abstract
Description
Claims
Application Information

- R&D Engineer
- R&D Manager
- IP Professional
- Industry Leading Data Capabilities
- Powerful AI technology
- Patent DNA Extraction
Browse by: Latest US Patents, China's latest patents, Technical Efficacy Thesaurus, Application Domain, Technology Topic, Popular Technical Reports.
© 2024 PatSnap. All rights reserved.Legal|Privacy policy|Modern Slavery Act Transparency Statement|Sitemap|About US| Contact US: help@patsnap.com