Improved method for processing high-iron and high-magnesium laterite and obtaining hematite product
A technology for laterite ore and hematite, applied in the field of nickel ore smelting, can solve the problems of acid consumption, energy consumption and low equipment investment cost, and achieve the effect of realizing no acid discharge, avoiding environmental pollution, and avoiding excessive acidity
- Summary
- Abstract
- Description
- Claims
- Application Information
AI Technical Summary
Problems solved by technology
Method used
Image
Examples
Embodiment 1
[0038] (1) the ore sample 1 # The aqueous pulp (solid-to-liquid mass ratio is 1:10) is added to the first leaching tank, 98% (w / w) sulfuric acid (acid ore mass ratio is 1.7:1) is added, the temperature is raised to 100°C, and the leaching is carried out for 1.5h. The pulp is filtered to obtain leach slag A and leach solution B;
[0039] (2) sending leach solution B into the second leaching kettle;
[0040] (3) According to ore sample 1 # and sample 3 # Composition, free acid content of leaching solution B and the amount of acid that can be released by iron deposition in leaching solution B, determine that ore sample 3 # The addition amount is ore sample 1 # 2 times; according to 10g air / g ore (including ore sample 1 # and sample 3 # ) and 0.05g hematite / g ore (including ore sample 1 # and sample 3 # ) in the amount of adding air and seed crystals (hematite) respectively in the second leaching kettle; ore sample 3 # The water-based pulp (solid-liquid mass ratio is 1:10...
Embodiment 2
[0047] (1) the ore sample 1 # The aqueous pulp (solid-to-liquid mass ratio is 1:10) is added to the first leaching tank, 98% (w / w) sulfuric acid (acid-mineral mass ratio is 2.5:1) is added, the temperature is raised to 95°C, and the leaching is carried out for 2.5h. The pulp is filtered to obtain leach slag A and leach solution B;
[0048] (2) sending leach solution B into the second leaching kettle;
[0049] (3) According to ore sample 1 # and sample 3 # Composition, free acid content of leaching solution B and the amount of acid that can be released by iron deposition in leaching solution B, determine that ore sample 3 # The addition amount is ore sample 1 # 3 times; the ore sample 3 # The aqueous pulp (solid-to-liquid mass ratio is 1:10) is divided into 4 shares and added to the second leaching tank for leaching, and the addition and leaching are performed according to the following conditions: first add the first strand of pulp (mine sample 3 # 50% of the total volum...
Embodiment 3
[0056] (1) the ore sample 2 # The aqueous pulp (solid-to-liquid mass ratio is 1:10) is added to the first leaching tank, 98% (w / w) sulfuric acid (acid-mine mass ratio is 1.5:1) is added, the temperature is raised to 90°C, and the leaching is carried out for 3 hours. The obtained pulp After filtering, leach residue A and leach solution B are obtained;
[0057] (2) sending leach solution B into the second leaching kettle;
[0058] (3) According to ore sample 2 # and sample 4 # The composition of the leaching solution B, the free acid content of the leaching solution B and the amount of acid that can be released by iron deposition in the leaching solution B, determine the # The addition amount is ore sample 2 # 1.5 times; the ore sample 4 # The water-based pulp (solid-to-liquid mass ratio is 1:10) is divided into 3 shares and added to the second leaching tank for leaching, and the addition and leaching are performed according to the following conditions: first add the first ...
PUM
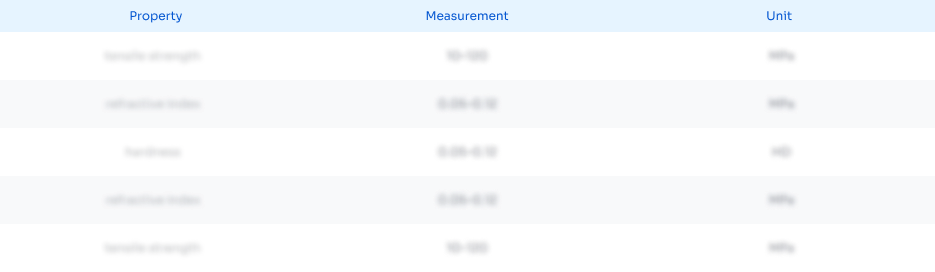
Abstract
Description
Claims
Application Information

- R&D
- Intellectual Property
- Life Sciences
- Materials
- Tech Scout
- Unparalleled Data Quality
- Higher Quality Content
- 60% Fewer Hallucinations
Browse by: Latest US Patents, China's latest patents, Technical Efficacy Thesaurus, Application Domain, Technology Topic, Popular Technical Reports.
© 2025 PatSnap. All rights reserved.Legal|Privacy policy|Modern Slavery Act Transparency Statement|Sitemap|About US| Contact US: help@patsnap.com