Wear-resisting nylon PA66 (Polyamide) composite material and preparation method thereof as well as application of composite material in automobile
A technology of PA66 and composite materials, which is applied in the field of modifying a wear-resistant nylon PA66 composite material and its preparation, can solve problems such as insufficient strength, toughness, corrosion resistance, unstable product quality, and poor processing performance, and achieve Strong wear resistance, stable injection molding process, and good fluidity
- Summary
- Abstract
- Description
- Claims
- Application Information
AI Technical Summary
Problems solved by technology
Method used
Examples
Embodiment 1
[0033] Prepare wear-resistant nylon PA66 composite material, the specific steps are:
[0034] The first step: prepare material A (kg):
[0035] Weigh nylon PA66 30, ACS resin 40, polycarbonate 15, aminopropyltriethoxysilane 0.2, methyltriethoxysilane 0.4, antioxidant 1010 0.2, graphite 7, polycaprolactone 2, Polyethylene wax 1.5, modified nano powder 6,
[0036] Among them, the modified nano powder is prepared by the following method: after mixing calcium carbonate, lapis lazuli powder, and potassium feldspar powder in equal proportions, burning at 600-700°C for 4-5 hours, then grinding into nano powder, mixing into Stir evenly with 3-5% bis(dioctyloxypyrophosphate) ethylene titanate by weight of the powder, dry and pulverize into powder,
[0037] Mix the weighed raw materials evenly, inhale into a drying barrel, and dry at 90-100°C for 4-6 hours;
[0038] When the water content of the mixture is less than 0.15%, the drying ends;
[0039] The dried mixed material is extrud...
Embodiment 2
[0048] With the wear-resistant nylon PA66 composite material that embodiment 1 makes, prepare the connector blade type plug sheath DJ7095-3-11 on the automobile, comprise the following steps:
[0049] (1) After mixing 25kg of wear-resistant nylon PA66 composite material and 1.5g of yellow-green powder evenly, add it to the dryer and dry it at 100-120°C for 6 hours.
[0050](2) Set the temperature of the heating section of the injection molding machine: the first section is 275±5°C, the second section is 270±5°C, the third section is 265±5°C, the fourth section is 260±5°C, the fifth section is 255±5°C ℃;
[0051] (3) Add the dried raw materials into the injection molding machine, and set the molding process parameters of the injection molding section:
[0052] a. The first section adopts medium and low pressure of 35-40 Mpa and medium speed injection of 45-55m / s, the injection time is 1.0-1.5 seconds, and the amount of glue injected is 78-80% of the product;
[0053] b. The s...
PUM
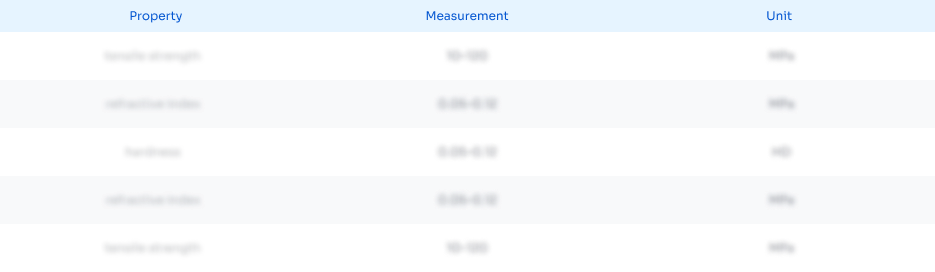
Abstract
Description
Claims
Application Information

- Generate Ideas
- Intellectual Property
- Life Sciences
- Materials
- Tech Scout
- Unparalleled Data Quality
- Higher Quality Content
- 60% Fewer Hallucinations
Browse by: Latest US Patents, China's latest patents, Technical Efficacy Thesaurus, Application Domain, Technology Topic, Popular Technical Reports.
© 2025 PatSnap. All rights reserved.Legal|Privacy policy|Modern Slavery Act Transparency Statement|Sitemap|About US| Contact US: help@patsnap.com