Method for manufacturing conducting circuit by additive process
A conductive circuit and process technology, which is applied in the field of conductive circuit preparation by additive process, can solve the problems of the conductivity of nano-copper ink conductive copper paste is not very ideal, which limits the large-scale application of printed electronic technology, and achieves excellent adhesion , Reduce the cost of equipment improvement, the effect of short production cycle
- Summary
- Abstract
- Description
- Claims
- Application Information
AI Technical Summary
Problems solved by technology
Method used
Image
Examples
Embodiment 1
[0033] (1) Take 10g of polyurethane resin, add 5g of nano-calcium carbonate, 0.5g of γ-mercaptopropyltrimethoxysilane, 0.6g of methyltrimethoxysilane, 0.3g of γ-glycidyl etheroxypropyltrimethoxysilane, 10g mixed solvent (0.5g water, 0.2g methanol, 0.3g ethanol, 0.1g acetylacetone, 0.1g acetone, 7.5g butyl acetate, 0.5g ethylene glycol methyl ether, 0.8g ethylene glycol butyl ether), 0.1g Polyvinylpyrrolidone is mixed and stirred at 500 rpm for 24 hours, and the measured viscosity is greater than 6000 centipoise, and the preparation of the film-forming agent is completed;
[0034] (2) Use polyimide as the substrate, soak the substrate in 1mol / L sodium hydroxide solution for 10 minutes before use, and then clean it with deionized water;
[0035] (3) Use a 500-mesh screen film-forming agent to print circuit patterns on the substrate;
[0036] (4) Heat the printed circuit at 80oC for 1 hour;
[0037] (5) Immerse the treated substrate in 0.1mol / L palladium chloride solution for 1...
Embodiment 2
[0046](1) Take 5g of diethylenetriaminopropyltrimethoxysilane, 5g of methyltrimethoxysilane, 15g of mixed solvent (3g of water, 2g of methanol, 1g of ethanol, 1g of acetylacetone, 1g of ethylene glycol methyl ether, ethyl Glycol butyl ether 2g isopropanol 3.5g, acetone 1.5g), mixing and stirring at 500 rpm / min for 24 hours, the measured viscosity is less than 100 centipoise, and the film-forming agent is prepared;
[0047] (2) Use polyethylene terephthalate as the substrate, soak the substrate in 1mol / L sodium hydroxide solution for 10 minutes before use, and then clean it with deionized water;
[0048] (3) Use a 50um nozzle inkjet printer to print out circuit graphics;
[0049] (4) Heat the printed circuit at 70oC for 1 hour;
[0050] (5) Immerse the treated substrate in 0.1mol / L silver nitrate solution for 1 hour;
[0051] (6) Wash off excess catalyst by soaking in deionized water;
[0052] (7) Dry at 50oC for 10 minutes;
[0053] (8) Configure electroless copper plating...
Embodiment 3
[0059] (1) Take 5g of 3-aminopropyltrimethoxysilane, 3g of dimethyldimethoxysilane, 2g of phenyltrimethoxysilane, 15g of mixed solvent (3g of water, 2g of methanol, 1g of ethanol, 1g of acetylacetone, ethyl Glycol methyl ether 1g, ethylene glycol butyl ether 2g isopropanol 3.5g, acetone 1.5g), mixed and stirred at 500 rpm / min for 24 hours, the measured viscosity was less than 100 centipoise, and the film-forming agent was prepared;
[0060] (2) Use polyethylene terephthalate as the substrate, soak the substrate in 1mol / L sodium hydroxide solution for 10 minutes before use, and then clean it with deionized water;
[0061] (3) Use a 50um nozzle inkjet printer to print out circuit graphics;
[0062] (4) heat-treat the printed circuit at 70oC for 1 hour;
[0063] (5) Immerse the treated substrate in 0.1mol / L silver nitrate solution for 1 hour;
[0064] (6) Soak and wash off excess catalyst with deionized water;
[0065] (7) Dry at 50oC for 10 minutes;
[0066] (8) Configure th...
PUM
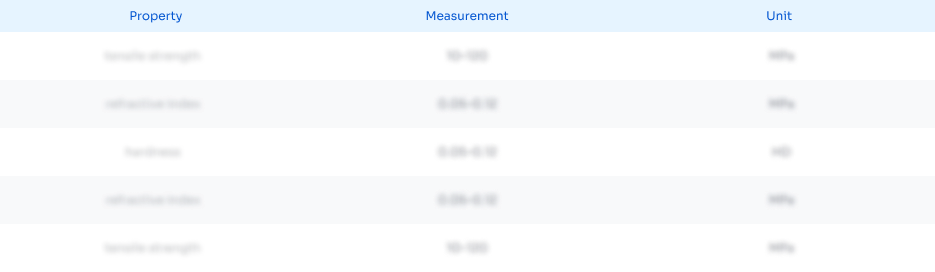
Abstract
Description
Claims
Application Information

- R&D
- Intellectual Property
- Life Sciences
- Materials
- Tech Scout
- Unparalleled Data Quality
- Higher Quality Content
- 60% Fewer Hallucinations
Browse by: Latest US Patents, China's latest patents, Technical Efficacy Thesaurus, Application Domain, Technology Topic, Popular Technical Reports.
© 2025 PatSnap. All rights reserved.Legal|Privacy policy|Modern Slavery Act Transparency Statement|Sitemap|About US| Contact US: help@patsnap.com