Micro-crystal muscovite/polybutylene terephthalate composite material
A polybutylene terephthalate and microcrystalline muscovite technology, which is applied in the field of polymer materials, can solve the problems of large molding shrinkage, low thermal deformation temperature, and small improvement range, and achieves low shrinkage and thermal High deformation temperature and good heat resistance
- Summary
- Abstract
- Description
- Claims
- Application Information
AI Technical Summary
Problems solved by technology
Method used
Image
Examples
Embodiment 1
[0029] Weigh 100 parts of PBT, 10 parts of microcrystalline muscovite, 2 parts of anti-1010, 2 parts of anti-168, 5 parts of POE-g-MAH, and 1 part of lubricant silicone oil and mix them in a high-speed mixer for 3 minutes, and mix the uniform material Extrude and granulate in a twin-screw extruder.
[0030] The temperature setting of the extruder is: 200°C in zone I, 220°C in zone II, 230°C in zone III, 240°C in zone IV, 245°C in zone V, 250°C in zone VI, and 250°C at the head. After the material is extruded, it is cooled by water, Cut into pellets to obtain the product of the present invention, and the performance test results are shown in Table 2.
[0031]
Embodiment 2
[0040] Weigh 100 parts of PBT, 30 parts of microcrystalline muscovite, 2 parts of anti-1098, 2 parts of anti-168, 10 parts of POE-g-MAH, 3 parts of lubricant stearic acid, and 3 parts of silane coupling agent KH550 in a high-speed mixer Mix in the medium for 3 minutes, and extrude and granulate the uniformly mixed material in a twin-screw extruder.
[0041] The temperature setting of the extruder is: 200°C in zone I, 220°C in zone II, 230°C in zone III, 240°C in zone IV, 245°C in zone V, 250°C in zone VI, and 250°C at the head. After the material is extruded, it is cooled by water, Cut into pellets to obtain the product of the present invention, and the performance test results are shown in Table 2.
[0042]
Embodiment 3
[0052] Weigh 100 parts of PBT, 60 parts of microcrystalline muscovite, 3 parts of anti-1010, 3 parts of anti-1098, 15 parts of EPDM rubber, 3 parts of lubricant liquid paraffin, 6 parts of silane coupling agent KH550 in a high-speed mixer Mix for 3 minutes, and extrude and granulate the homogeneously mixed material in a twin-screw extruder.
[0053] The temperature setting of the extruder is: 200°C in zone I, 220°C in zone II, 230°C in zone III, 240°C in zone IV, 245°C in zone V, 250°C in zone VI, and 250°C at the head. After the material is extruded, it is cooled by water, Cut into pellets to obtain the product of the present invention, and the performance test results are shown in Table 2.
[0054]
PUM
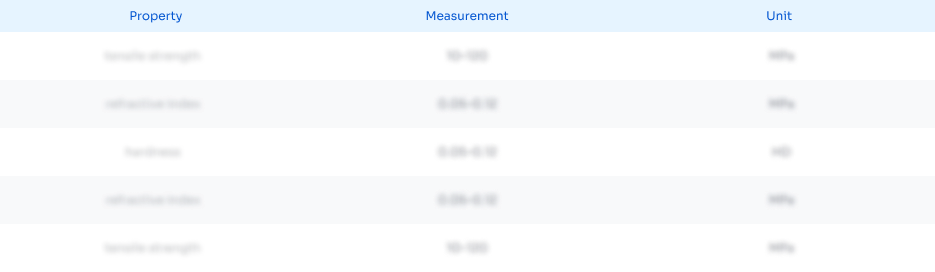
Abstract
Description
Claims
Application Information

- Generate Ideas
- Intellectual Property
- Life Sciences
- Materials
- Tech Scout
- Unparalleled Data Quality
- Higher Quality Content
- 60% Fewer Hallucinations
Browse by: Latest US Patents, China's latest patents, Technical Efficacy Thesaurus, Application Domain, Technology Topic, Popular Technical Reports.
© 2025 PatSnap. All rights reserved.Legal|Privacy policy|Modern Slavery Act Transparency Statement|Sitemap|About US| Contact US: help@patsnap.com