A polyamide poly(phenylene oxide) resin composition and a preparing method thereof
A technology of polyphenylene ether resin and composition, which is applied in the field of polyamide polyphenylene ether resin composition and its preparation, can solve the problems of incompatibility of flow performance and impact performance, and solve the problem of incompatibility of processing performance and impact performance Excellent impact performance, the effect of reducing dosage
- Summary
- Abstract
- Description
- Claims
- Application Information
AI Technical Summary
Problems solved by technology
Method used
Image
Examples
Embodiment 1~4
[0029] The polyamide polyphenylene ether resin composition having both fluidity and impact properties in this embodiment includes the components shown in Table 1 in parts by weight. Its preparation method comprises the following steps:
[0030] (1) Take the raw material according to the parts by weight in Table 1;
[0031] (2) The raw materials are mixed in a high-speed mixer;
[0032] (3) All the mixed raw materials mentioned above are thrown into the twin-screw extruder from the main feeding port at one time, and the composition is obtained through melt extrusion, cooling and granulation.
[0033] In the above preparation method, the barrel temperature of the extruder is set to 260, 260, 265, 265, 270, 270, 275, 275, 280, and 275° C. from the feeding port to the die in ten zones.
Embodiment 5
[0046] A polyamide polyphenylene ether resin composition prepared by using the following components and raw materials in parts by weight: bifunctional polyamide 30, monofunctional polyamide 30, polyphenylene ether 25, elastic block copolymer 5, functional elastic Polyolefin1. Wherein, the bifunctional polyamide is a polyamide obtained by polycondensation of a diamine and a dibasic acid, and polyamide 66 is used in this embodiment. The monofunctional polyamide is a polyamide obtained by ring-opening polymerization of lactam, and polyamide 6 is used in this embodiment. The polyphenylene ether is poly(2,6-dimethyl-1,4-phenylene) ether. The elastomeric block copolymer is a styrene-butadiene-styrene triblock copolymer. The functional elastic polyolefin is an ethylene-octene copolymer grafted with maleic anhydride.
[0047] The preparation method of polyamide polyphenylene ether resin composition adopts the following steps:
[0048] (1) prepare materials according to the formula...
Embodiment 6
[0051]A polyamide polyphenylene ether resin composition prepared by using the following components and raw materials in parts by weight: bifunctional polyamide 40, monofunctional polyamide 20, polyphenylene ether 15, elastic block copolymer 8, functional elastic Polyolefin 4. Wherein, the bifunctional polyamide is a polyamide obtained by polycondensation of a diamine and a dibasic acid, and polyamide 66 is used in this embodiment. The monofunctional polyamide is a polyamide obtained by ring-opening polymerization of lactam, and polyamide 6 is used in this embodiment. The polyphenylene ether is poly(2,6-dimethyl-1,4-phenylene) ether. The elastomeric block copolymer is a styrene-butadiene-styrene triblock copolymer. The functional elastic polyolefin is an ethylene-octene copolymer grafted with maleic anhydride.
[0052] The preparation method of polyamide polyphenylene ether resin composition adopts the following steps:
[0053] (1) prepare materials according to the formula...
PUM
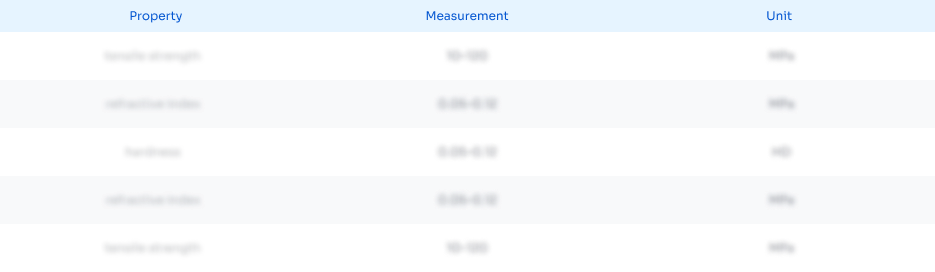
Abstract
Description
Claims
Application Information

- R&D Engineer
- R&D Manager
- IP Professional
- Industry Leading Data Capabilities
- Powerful AI technology
- Patent DNA Extraction
Browse by: Latest US Patents, China's latest patents, Technical Efficacy Thesaurus, Application Domain, Technology Topic, Popular Technical Reports.
© 2024 PatSnap. All rights reserved.Legal|Privacy policy|Modern Slavery Act Transparency Statement|Sitemap|About US| Contact US: help@patsnap.com