Processing net forming integrated method for amorphous alloy workpiece
A technology of amorphous alloy and amorphous master alloy, which is applied in the field of preparation of amorphous alloy workpieces, can solve problems such as the difficulty in realizing precise and complex amorphous alloy workpieces, the poor machinability of amorphous alloy materials, and the inability to apply amorphous alloys. Achieve the effect of saving manpower, material resources and time, reducing procedures, and promoting the application
- Summary
- Abstract
- Description
- Claims
- Application Information
AI Technical Summary
Problems solved by technology
Method used
Image
Examples
Embodiment 1
[0022] The lanthanum-based alloy is evenly melted in a vacuum electric arc furnace, coarsely crushed and put into a quartz tube, and the amorphous alloy jewelry is prepared by spray casting, and gypsum is used as a collapsible mold material. The specific steps are as follows:
[0023] 1) Put the lanthanum-based alloy into a quartz tube with a circular nozzle, put the quartz tube together with the master alloy in a vacuum high-frequency induction furnace, place the plaster mold at the injection position, and evacuate to 5×10 -3 Pa.
[0024] 2) After the vacuum reaches the required level, turn off the vacuum equipment and fill the furnace with argon as a melting protective gas, and close the gas charging device when the pressure in the furnace is close to 0.5 atmospheres.
[0025] 3) Turn on the high-frequency induction power supply. After the alloy is completely melted, keep it warm at 50-80°C higher than the melting temperature of the alloy for 2-5 minutes. Turn off the induct...
Embodiment 2
[0028] The difference from Example 1 is:
[0029] The zirconium-based master alloy is evenly smelted according to the method in Example 1, and the gypsum mold is pre-cooled with dry ice as a coolant before being placed in the high-frequency induction furnace. inside the furnace. The master alloy smelting and spray casting process is as in Example 1. After the alloy is poured into the gypsum mold, the gypsum mold is quickly taken out from the furnace and water quenched. Other cleaning procedures are as embodiment 1. The purpose of this embodiment is to increase the cooling rate of the alloy, which is beneficial to the preparation of large-volume amorphous alloy workpieces.
Embodiment 3
[0031] The difference from Example 2 is:
[0032] Preparation of amorphous alloy springs. Copper powder and shavings are used as mold molding materials, organic resin binders are used as molding material binders, and the mass ratio of copper powder and binder is 10:1. Zirconium-based alloy melting and casting, cooling process as in Example 2. After the casting process is over, the mold is soaked in the organic solvent acetone for 20 minutes, and then the soaked container is placed in an ultrasonic generator for ultrasonic cleaning until a complete amorphous alloy workpiece is taken out. Compared with the mold prepared by copper powder, the heat conduction speed is higher, which is beneficial to the formation of amorphous alloy and the preparation of larger size amorphous alloy.
PUM
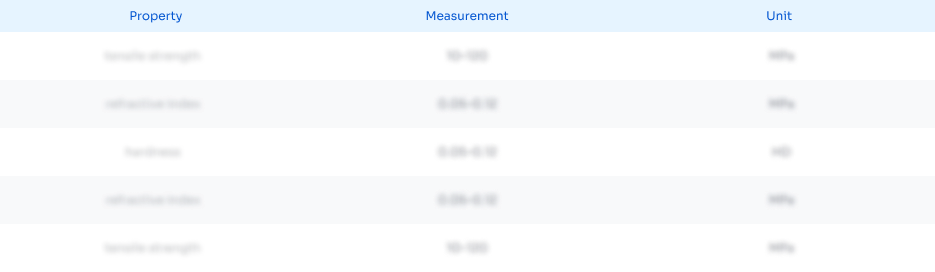
Abstract
Description
Claims
Application Information

- R&D
- Intellectual Property
- Life Sciences
- Materials
- Tech Scout
- Unparalleled Data Quality
- Higher Quality Content
- 60% Fewer Hallucinations
Browse by: Latest US Patents, China's latest patents, Technical Efficacy Thesaurus, Application Domain, Technology Topic, Popular Technical Reports.
© 2025 PatSnap. All rights reserved.Legal|Privacy policy|Modern Slavery Act Transparency Statement|Sitemap|About US| Contact US: help@patsnap.com