Preparation method of efficient deemulsifier for naphthenic extra heavy oil and product thereof
A technology of demulsifier and extra heavy oil, which is applied in the field of preparation of extra heavy oil demulsifier. It can solve the problems of insignificant gradient change in the demulsification process, large dosage of demulsifier, and unsatisfactory dehydration speed, etc., to achieve efficient and rapid demulsification, Good demulsification effect, convenient for industrial production
- Summary
- Abstract
- Description
- Claims
- Application Information
AI Technical Summary
Problems solved by technology
Method used
Image
Examples
Embodiment 1
[0036] Put 100kg of phenol, 550kg of tetraethylenepentamine, and 200kg of xylene into the reaction kettle, raise the temperature to 60°C under stirring, slowly add 210kg of 37% formaldehyde solution dropwise, continue heating and keep the temperature at 90-95°C, and after the reaction reaches the end point, Dehydrate at a temperature of 120°C and a vacuum of -0.08 to -0.09 MPa to obtain a phenolic amine resin. Add 50kg of phenolamine resin and 15kg of catalyst to the autoclave, compounded by potassium hydroxide and glacial acetic acid in a 1:1 weight ratio, add 750kg of propylene oxide to control the temperature to 135-155°C, add 200kg of ethylene oxide Control the temperature at 120°C to control the pressure of the kettle to 0.2-0.4 MPa, and polymerize to obtain a block polyether polymer compound. Put 700kg of synthetic block polyether, 200kg of acrylic acid, and 5kg of catalyst p-toluenesulfonic acid into the reactor, stir and raise the temperature at 130-145°C to reflux for...
Embodiment 2
[0038] 150kg of bisphenol A, 650kg of triethylenetetramine, and 300kg of xylene were heated up to 65°C under stirring, and 300kg of 36.5% formaldehyde solution was slowly added dropwise, and continued heating to keep the temperature at 90-105°C. Dehydration at -0.08~-0.09MPa at a vacuum degree of ℃ to obtain phenolic amine resin. Add 70kg of phenolamine resin to the autoclave, 18.5kg of catalyst is compounded by calcium hydroxide and sodium acetate at a weight ratio of 1:1, heat up to 140°C, adjust the pressure range to 0.2-0.5MPa, and add 800kg of propylene oxide , Add 350kg of ethylene oxide at 120°C to polymerize to obtain a block polyether polymer. Add 290kg of ethylene oxide to control the temperature at 120°C. Put 900kg of synthetic block polyether, 260kg of fumaric acid, and 5kg of catalyst p-toluenesulfonic acid into the reactor, stir and raise the temperature at 140-150°C to reflux for 50-60 minutes, until the separated water no longer increases, then cool down to 60-...
Embodiment 5
[0040]Put 1500kg of bisphenol A, 600kg of tetraethylenepentamine, and 600kg of xylene into the reaction kettle, raise the temperature to 70°C under stirring, slowly add 160kg of 37% formaldehyde solution dropwise, continue heating and keep the temperature at 90-95°C, and react to the end Finally, it is dehydrated at a temperature of 120°C and a vacuum degree of -0.08~-0.09MPa to obtain a phenolic amine resin. Add 100kg of phenolamine resin and 18kg of catalyst to the autoclave and mix calcium hydroxide and glacial acetic acid in a weight ratio of 1:1, add 900kg of propylene oxide to control the temperature to 135-155°C, add 200kg of ethylene oxide to control the temperature at 120 The pressure of the kettle is controlled to be 0.2-0.4 MPa at ℃, and the block polyether macromolecular compound is obtained by polymerization. Put 800kg of synthetic block polyether, 260kg of methacrylic acid, and 5kg of catalyst p-toluenesulfonic acid into the reactor, stir and raise the temperatur...
PUM
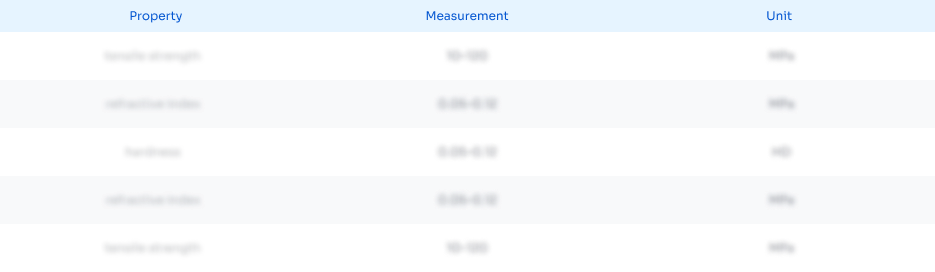
Abstract
Description
Claims
Application Information

- Generate Ideas
- Intellectual Property
- Life Sciences
- Materials
- Tech Scout
- Unparalleled Data Quality
- Higher Quality Content
- 60% Fewer Hallucinations
Browse by: Latest US Patents, China's latest patents, Technical Efficacy Thesaurus, Application Domain, Technology Topic, Popular Technical Reports.
© 2025 PatSnap. All rights reserved.Legal|Privacy policy|Modern Slavery Act Transparency Statement|Sitemap|About US| Contact US: help@patsnap.com