A method for removing cyanide-containing waste gas
A waste gas and removal technology, which is applied in the field of removal of cyanide-containing waste gas and catalytic combustion method to remove cyanide-containing waste gas, can solve the problems of low specific surface area of alumina carrier, poor dispersion of active components, and higher requirements for removal conditions , to achieve the effect of good low temperature activity, improved dispersion, and no by-products
- Summary
- Abstract
- Description
- Claims
- Application Information
AI Technical Summary
Problems solved by technology
Method used
Image
Examples
Embodiment 1
[0026] Embodiment 1: take by weighing 0.0756gCu (NO 3 ) 2 ·3H 2 O (chemically pure reagent), and dissolve it in water to form an impregnating solution, then weigh 1g of SBA-15 mesoporous molecular sieve and add it to the impregnating solution, stir in a water bath at 40°C for 24 hours, and then use a rotary evaporator to remove the impregnating solution. Finally, the above-mentioned supported catalyst was placed in an air atmosphere at a rate of 2 °C / min to 550 °C for 10 hours to obtain a Cu / SBA-15 catalyst with a mass fraction of 5% copper. The prepared catalyst was placed in a miniature fixed-bed quartz reactor, and then the reactor was heated to 450°C, and a CH 3 CN(1vol%), O 2 (5vol%) and N 2 (As a balance gas) mixed gas, the air velocity of the mixed gas is 20000h -1, using an American Nicolet Nexus 470 infrared spectrometer with a 2.4m optical path gas analysis cell for online gas quantitative analysis, so as to obtain the conversion rate of acetonitrile and the yie...
Embodiment 2
[0027] Embodiment 2: take by weighing 0.1538gCr (NO 3 ) 3 9H 2 O, and dissolve it in water to make an impregnating liquid, then weigh 1g of SBA-16 mesoporous molecular sieve and add it to the impregnating liquid, stir in a water bath at 40°C for 24 hours, then use a rotary evaporator to remove the water in the impregnating liquid, and finally The above-mentioned supported catalyst was placed in an air atmosphere at a rate of 2 °C / min to 550 °C and calcined for 10 hours to obtain a Cr / SBA-15 catalyst with a mass fraction of 2% chromium supported. Put the prepared catalyst in a miniature fixed-bed quartz reactor, then raise the temperature of the reactor to 500°C, and pass through the reactor containing CH 3 CN(1vol%), O 2 (5vol%) and N 2 (As a balance gas) mixed gas, the air velocity of the mixed gas is 20000h -1 , using an American Nicolet Nexus 470 infrared spectrometer with a 2.4m optical path gas analysis cell for online gas quantitative analysis, so as to obtain the c...
Embodiment 3
[0028] Embodiment 3: take by weighing 0.0986gCo(NO 3 ) 2 ·6H 2 O, and dissolve it in water to form an impregnating liquid, then weigh 1g of KIT-5 mesoporous molecular sieve and add it to the impregnating liquid, stir in a water bath at 40°C for 24 hours, then use a rotary evaporator to remove the water in the impregnating liquid, and finally The above-mentioned supported catalyst was placed in an air atmosphere at a rate of 2 °C / min to 550 °C and calcined for 10 hours to obtain a Co / KIT-5 catalyst with a mass fraction of 2% cobalt. The prepared catalyst was placed in a miniature fixed-bed quartz reactor, and then the reactor was heated to 400°C, and a CH 3 CN(1vol%), O 2 (5vol%) and N 2 (As a balance gas) mixed gas, the air velocity of the mixed gas is 20000h -1 , using an American NicoletNexus 470 infrared spectrometer with a 2.4m optical path gas analysis cell for online gas quantitative analysis, so as to obtain the conversion rate of acetonitrile and the yield of each...
PUM
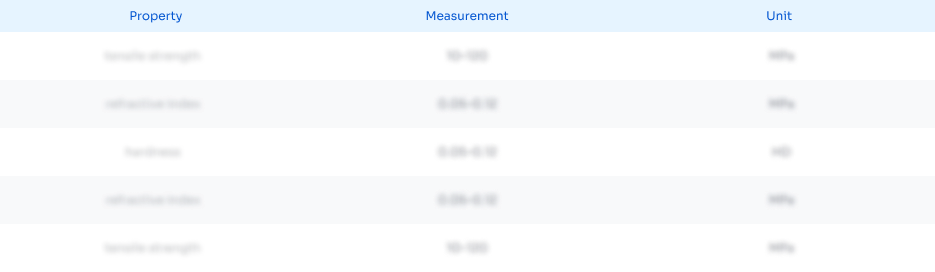
Abstract
Description
Claims
Application Information

- R&D
- Intellectual Property
- Life Sciences
- Materials
- Tech Scout
- Unparalleled Data Quality
- Higher Quality Content
- 60% Fewer Hallucinations
Browse by: Latest US Patents, China's latest patents, Technical Efficacy Thesaurus, Application Domain, Technology Topic, Popular Technical Reports.
© 2025 PatSnap. All rights reserved.Legal|Privacy policy|Modern Slavery Act Transparency Statement|Sitemap|About US| Contact US: help@patsnap.com