Anti-oxidation and anti-thermal fatigue hot working die steel and manufacturing method thereof
A hot work die steel, thermal fatigue resistance technology, applied in the field of metal materials, can solve the problems of poor anti-oxidation and thermal fatigue resistance, reduce the surface quality of the formed parts, reduce the service life of the mold and other problems, achieve high high temperature strength, high critical The effect of temperature, corrosion resistance and oxidation resistance improvement
- Summary
- Abstract
- Description
- Claims
- Application Information
AI Technical Summary
Problems solved by technology
Method used
Image
Examples
Embodiment Construction
[0018] Table 1 lists the chemical composition of 22 hot work die steels whose composition is within the scope of the present invention. After smelting and forging, a φ16mm hot work die steel bar is prepared, and then kept at 800-850°C for 1 hour, after air-cooling annealing treatment, heat treatment is performed according to the final heat treatment method of the present invention. The heat treatment process parameters are shown in Table 2. The steel bars after the final heat treatment were processed into standard tensile specimens and were subjected to instantaneous tensile tests at different temperatures on the electronic universal testing machine. The test results are listed in Table 2. In addition, differential thermal analysis technology is used to determine the critical temperature A of the steel of the present invention. c1 The measurement was performed and the results are also listed in Table 2. For comparison, the high temperature instantaneous tensile properties and c...
PUM
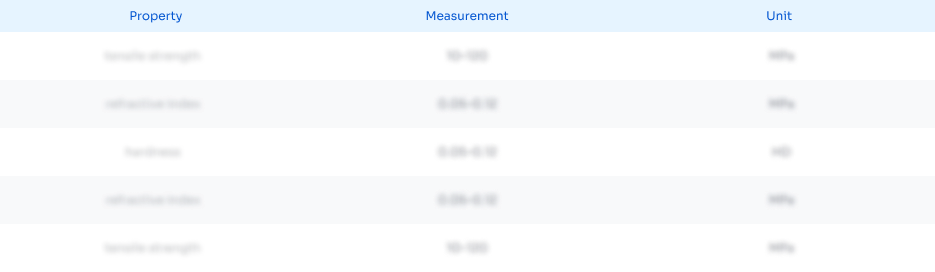
Abstract
Description
Claims
Application Information

- R&D Engineer
- R&D Manager
- IP Professional
- Industry Leading Data Capabilities
- Powerful AI technology
- Patent DNA Extraction
Browse by: Latest US Patents, China's latest patents, Technical Efficacy Thesaurus, Application Domain, Technology Topic, Popular Technical Reports.
© 2024 PatSnap. All rights reserved.Legal|Privacy policy|Modern Slavery Act Transparency Statement|Sitemap|About US| Contact US: help@patsnap.com