Method for producing bevel gear with ratchet on end face through powder metallurgy warm forming
A technology of powder metallurgy and helical gears, which is applied in the direction of metal material coating process, coating, furnace type, etc., can solve the problems of material performance not meeting the requirements, poor gear consistency, low material utilization rate, etc., and achieve product Good consistency, suitable for mass production, high material strength
- Summary
- Abstract
- Description
- Claims
- Application Information
AI Technical Summary
Problems solved by technology
Method used
Examples
Embodiment 2
[0016] Example 2. Take 93.0kg of iron powder, 1.5kg of copper powder, 0.5kg of molybdenum powder, 3.8kg of nickel powder, 0.6kg of natural graphite powder with a purity of 99.80%, 0.6kg of special lubricant for -325 mesh temperature mold obtained by chemical method, and put it into After mixing and stirring in a double-cone high-efficiency mixer for 60 minutes, put it into a mold cavity heated to 75°C, and press it at a unit pressure of 7.0T / cm 2 Under certain conditions, rotary pressing to a density of 7.2-7.3 g / cm 3 , to make compacts; the compacts were placed in a RST-110 mesh belt sintering furnace, and sintered at 1120° for 40 minutes in a protective atmosphere of hydrogen and nitrogen mixed gas. In the mixed gas of hydrogen and nitrogen, hydrogen accounts for 5% of the volume of the mixed gas, and nitrogen accounts for 95% of the volume of the mixed gas. Carbonitriding at 850°C for 60 minutes in a controlled atmosphere heat treatment furnace, quenching at 850°C, oil co...
PUM
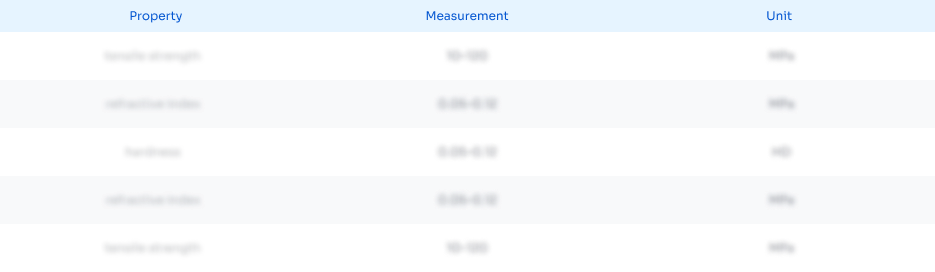
Abstract
Description
Claims
Application Information

- R&D
- Intellectual Property
- Life Sciences
- Materials
- Tech Scout
- Unparalleled Data Quality
- Higher Quality Content
- 60% Fewer Hallucinations
Browse by: Latest US Patents, China's latest patents, Technical Efficacy Thesaurus, Application Domain, Technology Topic, Popular Technical Reports.
© 2025 PatSnap. All rights reserved.Legal|Privacy policy|Modern Slavery Act Transparency Statement|Sitemap|About US| Contact US: help@patsnap.com