Method for measuring content of magnesium oxide in iron ores
A magnesia and iron ore technology, applied in the field of detection, can solve the problems of cumbersome operation, strict requirements, long time consumption, etc., and achieve the effects of low cost, high accuracy and precision, and high accuracy and tightness of results.
- Summary
- Abstract
- Description
- Claims
- Application Information
AI Technical Summary
Problems solved by technology
Method used
Image
Examples
Embodiment 1
[0019] First prepare the main reagents:
[0020] ① 0.02mol / L disodium ethylenediaminetetraacetic acid (EDTA) standard solution: Weigh 8g of AR grade disodium ethylenediaminetetraacetic acid and dissolve it in water, dilute to 1000mL with water, and mix well. Calibration shall be carried out according to GB / T601. ②Sodium hydroxide solution: 200g / L, 20g / L; ethylene glycol diethyl ether diammonium tetraacetic acid (EGTA) solution: 70g / L; phenylglycolic acid solution: 50g / L; triethanolamine solution: 1+1, 1 +4; hydrochloric acid solution: 1+9; ammonia solution: 2+3. ③Acid chrome blue K-naphthol green B indicator: Weigh 0.1g of AR grade acid chrome blue K, weigh 0.1g of AR grade naphthol green B, weigh 20g of AR grade chlorine Potassium chloride is placed in a mortar, thoroughly ground and mixed. ④ pH=10 ammonia water-ammonium chloride buffer solution: Weigh 67.5g of AR grade ammonium chloride, dissolve it in water, add 570mL of AR grade ammonia water, dilute to 1000 mL with wat...
Embodiment 2
[0029] On the basis of the experimental method of embodiment 1,
[0030] Weigh about 0.5g sample, weighed to an accuracy of 0.0001g, and place it in a nickel crucible. Add 5 g of sodium hydroxide solvent and mix well. Put the nickel crucible in a high-temperature furnace from a low temperature to 750°C and keep it warm for 15 minutes, then take out the crucible and cool it down. Put it in a 250mL beaker, add 75mL of boiling water, and immediately cover the watch glass. After the molten material falls off, wash the crucible and cover with hot water and a small amount of nitric acid. Under constant stirring, immediately add 25mL nitric acid to acidify, heat and boil until clear. Cool the solution, transfer it into a 250mL volumetric flask, dilute with water to the mark, and shake well for later use. Draw 25mL of the test solution in the volumetric flask and place it in a 300mL beaker, add 10mL of phenylglycolic acid, stir well, add 12mL of ethylene glycol diethyl ether diammo...
Embodiment 3
[0038] On the basis of the experimental method of embodiment 1,
[0039] Weigh about 0.6g sample, weighed to an accuracy of 0.0001g, and place it in a nickel crucible. Add 6 g of sodium hydroxide solvent and mix well. Put the nickel crucible in a high-temperature furnace from a low temperature to 800°C and keep it warm for 10 minutes, then take out the crucible and cool it down. Put it in a 250mL beaker, add 80mL of boiling water, and immediately cover the watch glass. After the melt falls off, wash the crucible and cover with hot water and a small amount of nitric acid. Under constant stirring, immediately add 30mL nitric acid for acidification, heat and boil until clear. Cool the solution, transfer it into a 250mL volumetric flask, dilute with water to the mark, and shake well for later use. Draw 30mL of the test solution in the volumetric flask and place it in a 300mL beaker, add 15mL of phenylglycolic acid, stir well, add 14mL of ethylene glycol diethyl ether diammonium...
PUM
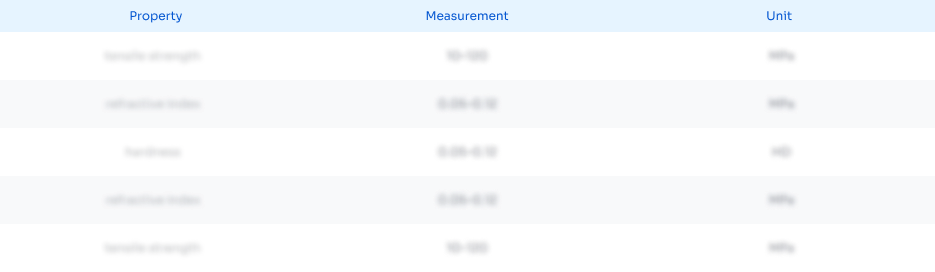
Abstract
Description
Claims
Application Information

- R&D
- Intellectual Property
- Life Sciences
- Materials
- Tech Scout
- Unparalleled Data Quality
- Higher Quality Content
- 60% Fewer Hallucinations
Browse by: Latest US Patents, China's latest patents, Technical Efficacy Thesaurus, Application Domain, Technology Topic, Popular Technical Reports.
© 2025 PatSnap. All rights reserved.Legal|Privacy policy|Modern Slavery Act Transparency Statement|Sitemap|About US| Contact US: help@patsnap.com