Austenite corrosion-resisting nickel-based casting alloy and manufacturing process thereof
A manufacturing process and casting alloy technology, which is applied in the field of austenitic corrosion-resistant nickel-based casting alloys and its manufacturing process, can solve the problems of small weight and size of castings and cannot be applied to large castings, etc., and achieve the goal of maintaining strength and corrosion resistance Effect
- Summary
- Abstract
- Description
- Claims
- Application Information
AI Technical Summary
Problems solved by technology
Method used
Image
Examples
Embodiment Construction
[0033] The present invention will be further described in detail below in combination with specific embodiments.
[0034] (1) Melt scrap steel and ferrochrome in a non-vacuum electric arc furnace, add nickel plate, ferrotungsten, ferromolybdenum, ferrocobalt, ferrosilicon, and ferromanganese after the molten steel is melted, control the carbon content to meet the requirements, and adjust the composition before the furnace After passing the test, raise the melt temperature to 1560-1620°C, add silicon-calcium alloy for pre-deoxidation, add aluminum for final deoxidation, and then add ferro-titanium and ferro-boron in sequence to melt;
[0035] (2) When ferro-titanium and ferro-boron are all melted, wrap the composite modification inoculant composed of granular ferroniobium, zirconium, lanthanum (La) or rare earth element (Re) rare earth magnesium alloy less than 12mm in thin iron sheet After being baked at a temperature of 160-200°C, it is placed at the bottom of the ladle, and ...
PUM
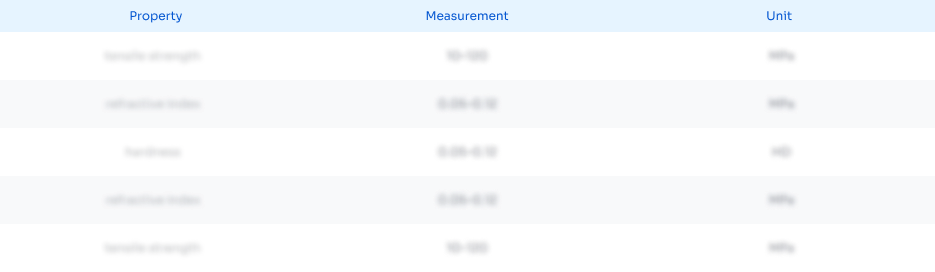
Abstract
Description
Claims
Application Information

- R&D
- Intellectual Property
- Life Sciences
- Materials
- Tech Scout
- Unparalleled Data Quality
- Higher Quality Content
- 60% Fewer Hallucinations
Browse by: Latest US Patents, China's latest patents, Technical Efficacy Thesaurus, Application Domain, Technology Topic, Popular Technical Reports.
© 2025 PatSnap. All rights reserved.Legal|Privacy policy|Modern Slavery Act Transparency Statement|Sitemap|About US| Contact US: help@patsnap.com