Preparation method of metal magnesium by magnesium-containing mineral and equipment adopted by preparation method
A technology of metal magnesium and minerals, applied in the field of metal materials, can solve the problems of high energy consumption and low efficiency, and achieve the effects of low energy consumption, high efficiency and fast chlorination speed
- Summary
- Abstract
- Description
- Claims
- Application Information
AI Technical Summary
Problems solved by technology
Method used
Image
Examples
Embodiment 1
[0031] Embodiment 1: certain magnesite test ore sample chemical multi-element analysis result is as follows:
[0032] element MgO SiO 2 CaO Fe 2 o 3 Loss on ignition content 42.95 6.08 1.15 0.29 48.27
[0033] The ore sample was crushed to -2mm by a hammer crusher, and the ore sample was lightly burned in a fluidized bed at a controlled temperature of 900°C for 1 hour, and then ground to -100 mesh by a ball mill. Take 500 g of the lightly burned product, add 800 mL of 10% HCl to react for 25 minutes, and then filter. The filtrate is adjusted to pH 4.5 with freshly digested milk of lime and filtered to remove impurities to obtain a pure filtrate. Fresh milk of lime was added to the purified filtrate at a rate of 10 mL / min, and the amount added was C Ca 2+ : C Mg 2+ = 0.9, the temperature of the water bath was 80°C under the condition of stirring for 1 h, and aging for 2 h. Mg(OH) obtained by filtration after aging 2 With 1mol / mL MgCl ...
Embodiment 2
[0035] Embodiment 2: adopting Qinghai Province Chaerhan Salt Lake bicholorite as raw material, its composition is as follows:
[0036] element Mg Cl - Ca K Na content 11.5 35.08 0.032 0.094 0.079
[0037] Take 500 grams of bischofite and add a certain amount of water to prepare a solution containing about 100 g / L of magnesium ions, filter to remove insoluble impurities, then add a certain amount of ammonia water and 10% seed crystals, in a water bath at 80 °C Make it fully react to form magnesium hydroxide precipitate, separate the magnesium hydroxide by vacuum filtration, put it into the muffle furnace for calcination, the calcination temperature is 900°C, and calcine for 1 hour, the magnesium oxide content of the product obtained is greater than 99.28%.
[0038] Under the situation of not adding catalytic reaction intermediate, carry out following steps with embodiment 1, it finally obtains metal magnesium 18.68 grams, and purity is 99.56...
Embodiment 3
[0039] Embodiment 3: certain iron tailings composition is as follows:
[0040] Element Fe 2 o 3 MgO SiO 2 CaO Al 2 o 3 MnO K 2 o Na 2 o content% 28.36 31.28 35.63 4.68 1.22 0.36 0.28 0.32
[0041] Grind 500 grams of iron tailings through a corundum ball mill to -100 mesh, and use 20% sulfuric acid for acid leaching reaction. The reaction temperature is 90 ° C, and the reaction time is 2 hours. After the reaction is completed, filter to obtain a crude magnesium sulfate solution. Add a certain concentration of sodium hydroxide to the solution and pass through chlorine gas to remove impurities in the form of precipitation to obtain a pure magnesium sulfate solution, and then use ammonium bicarbonate as a precipitant at a reaction temperature of 60 ° C to obtain Magnesium carbonate was precipitated, and after separation by suction filtration, the filter cake was calcined at 900°C for 2 hours to obtain magnesium oxide with a purit...
PUM
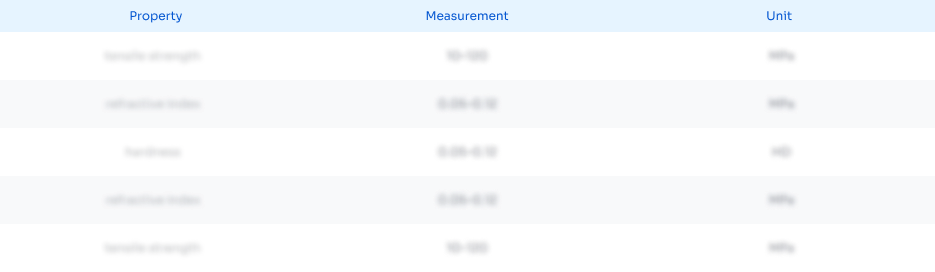
Abstract
Description
Claims
Application Information

- R&D Engineer
- R&D Manager
- IP Professional
- Industry Leading Data Capabilities
- Powerful AI technology
- Patent DNA Extraction
Browse by: Latest US Patents, China's latest patents, Technical Efficacy Thesaurus, Application Domain, Technology Topic, Popular Technical Reports.
© 2024 PatSnap. All rights reserved.Legal|Privacy policy|Modern Slavery Act Transparency Statement|Sitemap|About US| Contact US: help@patsnap.com