Method for producing mullite and calcium silicate by using high-alumina fly ash
A high-alumina fly ash and fly ash technology, which is applied in the direction of aluminum silicate, silicate, alkaline earth metal silicate, etc., can solve the problem of large market and policy influence, high price of industrial grade alumina, bauxite Resource scarcity and other issues, to achieve significant social benefits, reduce production costs, and make full use of resources
- Summary
- Abstract
- Description
- Claims
- Application Information
AI Technical Summary
Problems solved by technology
Method used
Image
Examples
Embodiment 1
[0030] Put the high-alumina fly ash into a ball mill for dry grinding, use alumina ball stone as the grinding medium, grind for 1 hour according to the mass ratio of the grinding medium and fly ash at 3:1, and pass the finely ground fly ash through a 100-mesh sieve. Mix 15% sodium hydroxide solution with finely ground fly ash according to the liquid-solid ratio of 3:1 and move it into the reaction kettle at 600r·min -1 , Reaction at 130°C for 2h. The reacted material is moved into a filter for separation to obtain solid-phase desiliconized fly ash and liquid-phase sodium silicate solution respectively. The process water and desiliconized fly ash are mixed at a liquid-solid ratio of 3:1, and heated at 300r· min -1 , Wash at 80°C for 1h. Mix 20% hydrochloric acid with water-washed desiliconized fly ash at a liquid-solid ratio of 3:1; -1 , Wash at 80°C for 1h. Mix the process water and the desiliconized fly ash after pickling according to the liquid-solid ratio of 3:1, and -...
Embodiment 2
[0032] Put the high-alumina fly ash into a ball mill for dry grinding, use alumina ball stone as the grinding medium, grind for 1 hour according to the mass ratio of the grinding medium and fly ash at 3:1, and pass the ground fly ash through a 200-mesh sieve. Mix 5% sodium hydroxide solution with finely ground fly ash at a liquid-solid ratio of 2:1, and move it into a reaction kettle at 700r min -1 , Reaction at 104°C for 2h. The reacted slurry is moved into a filter for separation to obtain solid-phase desiliconized fly ash and fly ash desiliconized mother liquor respectively. Mix process water and desiliconized fly ash at a liquid-solid ratio of 2:1, and -1 , Wash at 80°C for 1h. Mix 22% hydrochloric acid with water-washed desiliconized fly ash at a liquid-solid ratio of 2:1; -1 , Wash at 80°C for 1h. Mix the process water and the desiliconized fly ash after pickling according to the liquid-solid ratio of 2:1, and -1 , Wash at 80°C for 1h. The washed desiliconized fly ...
Embodiment 3
[0034] Put the high-alumina fly ash into a ball mill for dry grinding, use alumina ball stone as the grinding medium, grind for 1 hour according to the mass ratio of the grinding medium and fly ash at 3:1, and pass the finely ground fly ash through a 200-mesh sieve. Mix 10% sodium hydroxide solution with finely ground fly ash at a liquid-solid ratio of 2:1, and move it into a reaction kettle at 600r·min -1 , Reaction at 104°C for 1h. The reacted slurry is moved into a filter for separation to obtain solid-phase desiliconized fly ash and fly ash desiliconized mother liquor respectively. Mix process water and desiliconized fly ash at a liquid-solid ratio of 2:1, and -1 , Wash at 80°C for 1h. Mix 20% hydrochloric acid with water-washed desiliconized fly ash at a liquid-solid ratio of 2:1; -1 , Wash at 80°C for 1h. Mix the process water and the desiliconized fly ash after pickling according to the liquid-solid ratio of 2:1, and -1 , Wash at 80°C for 1h. The washed desiliconi...
PUM
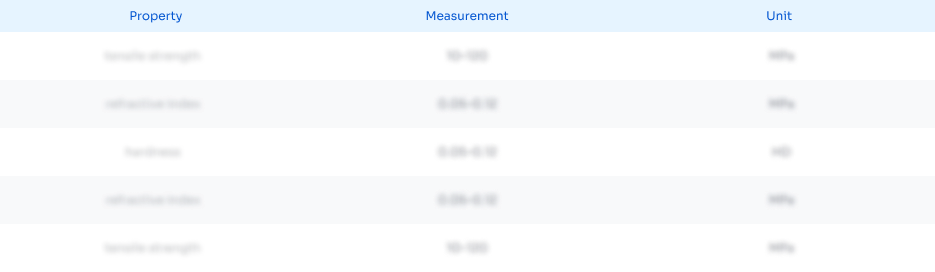
Abstract
Description
Claims
Application Information

- R&D
- Intellectual Property
- Life Sciences
- Materials
- Tech Scout
- Unparalleled Data Quality
- Higher Quality Content
- 60% Fewer Hallucinations
Browse by: Latest US Patents, China's latest patents, Technical Efficacy Thesaurus, Application Domain, Technology Topic, Popular Technical Reports.
© 2025 PatSnap. All rights reserved.Legal|Privacy policy|Modern Slavery Act Transparency Statement|Sitemap|About US| Contact US: help@patsnap.com