Hot melt adhesive membrane for bonding bi-metallic composite plate and preparing method thereof
A hot-melt adhesive film, composite board technology, applied in the direction of adhesives, adhesive types, ester copolymer adhesives, etc., can solve the problems of poor bonding strength, water resistance and salt spray aging resistance, etc. The effect of durable bonding, high peel strength and simple bonding process
- Summary
- Abstract
- Description
- Claims
- Application Information
AI Technical Summary
Problems solved by technology
Method used
Image
Examples
Embodiment 1
[0027] Mix 10% acrylate rubber, 10% polyethylene-acrylic acid, 30% chlorinated polyethylene, 20% rosin, and 30% calcium carbonate with a high-speed mixer, and extrude at 150°C with an extruder Granulate, and then stretch, pull, and roll through a casting machine to make a 0.15mm thick hot melt adhesive film. Investigate the 180°peel strength, water resistance, salt spray resistance and weather resistance of the adhesive film to metal Al / Al, Cu / Cu, stainless steel / stainless steel. The specific test results are shown in Table 1.
Embodiment 2
[0029] 20% acrylate rubber, 30% polyethylene-butyl acrylate, 20% polymethyl methacrylate, 15% maleic rosin, and 15% white carbon black are mixed with a high-speed mixer, and extruded Extrude and granulate at 180°C, and then stretch, pull, and wind through a casting machine to make a 0.15mm thick hot melt adhesive film. Investigate the 180°peel strength, water resistance, salt spray resistance and weather resistance of the adhesive film to metal Al / Al, Cu / Cu, stainless steel / stainless steel. The specific test results are shown in Table 1.
Embodiment 3
[0031] Mix 30% polyethylene-acrylic acid, 30% polyethylene-methyl acrylate, 20% polyethylene-methyl acrylate-maleic anhydride copolymer, and 20% polyethylene with a high-speed mixer, and extrude The machine is extruded and granulated at 150°C, and then stretched, drawn, and rolled by a casting machine to make a 0.15mm thick hot melt adhesive film. Investigate the 180°peel strength, water resistance, salt spray resistance and weather resistance of the adhesive film to metal Al / Al, Cu / Cu, stainless steel / stainless steel. The specific test results are shown in Table 1.
PUM
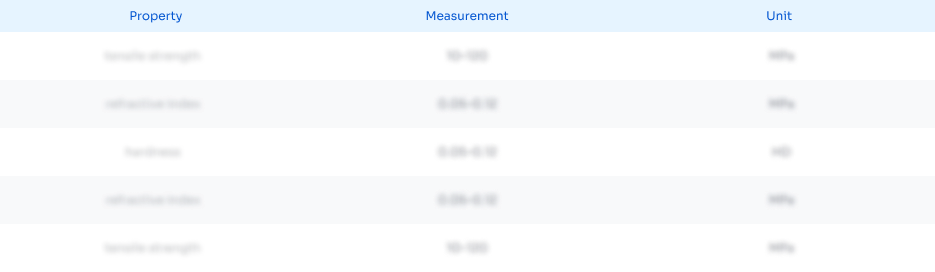
Abstract
Description
Claims
Application Information

- R&D
- Intellectual Property
- Life Sciences
- Materials
- Tech Scout
- Unparalleled Data Quality
- Higher Quality Content
- 60% Fewer Hallucinations
Browse by: Latest US Patents, China's latest patents, Technical Efficacy Thesaurus, Application Domain, Technology Topic, Popular Technical Reports.
© 2025 PatSnap. All rights reserved.Legal|Privacy policy|Modern Slavery Act Transparency Statement|Sitemap|About US| Contact US: help@patsnap.com