High temperature anti-oxidation coating molybdenum material and preparation method thereof
A high-temperature anti-oxidation and anti-oxidation coating technology, applied in the direction of coating, metal material coating process, solid-state diffusion coating, etc., can solve the problem of general high-temperature oxidation resistance, poor thermal matching between coating and substrate, and complex preparation process and other problems, to achieve the effects of easy control of structure and phase state, excellent high temperature oxidation resistance, and simple preparation process
- Summary
- Abstract
- Description
- Claims
- Application Information
AI Technical Summary
Problems solved by technology
Method used
Image
Examples
Embodiment 1
[0029] (1) Pretreatment of metal molybdenum base material: the metal molybdenum base material is polished with sandpaper until the surface is smooth and flat, and put into absolute ethanol or ethanol solution for degreasing and degreasing treatment, then dried and set aside.
[0030] (2) Nitriding treatment: place the pretreated metal molybdenum substrate in an atmosphere furnace, and raise the temperature to 800°C at a rate of 5°C / min under a 99.99% high-purity nitrogen atmosphere with a flow rate of 500mL / min. After heat preservation at 800°C for 24 hours, it was cooled to room temperature with the furnace, then taken out, cleaned with ultrasonic waves for 5-10 minutes, and dried to obtain a semi-finished product A with a molybdenum nitride coating on the molybdenum surface. Its diffraction spectrum and cross-sectional appearance are as follows: figure 2 , image 3 shown.
[0031] (3) Silicification treatment: Put the semi-finished product A into a high-purity alumina cruc...
Embodiment 2
[0034] (1) Pretreatment of metal molybdenum base material: the metal molybdenum base material is polished with sandpaper until the surface is smooth and flat, and put into absolute ethanol or ethanol solution for degreasing and degreasing treatment, then dried and set aside.
[0035] (2) Nitriding treatment: place the pretreated metal molybdenum substrate in an atmosphere furnace, and raise the temperature to 1400°C at a rate of 15°C / min under a 99.99% high-purity nitrogen atmosphere with a flow rate of 50mL / min. After heat preservation at 1400°C for 1 hour, it was cooled to room temperature with the furnace, then taken out, cleaned with ultrasonic waves for 5-10 minutes, and dried to obtain a semi-finished product A with a molybdenum nitride coating on the molybdenum surface.
[0036] (3) Silicification treatment: Put the semi-finished product A into a high-purity alumina crucible equipped with a uniformly mixed siliconization agent, which contains silicon powder, NaF, Al 2 o...
Embodiment 3
[0039] (1) Pretreatment of metal molybdenum base material: the metal molybdenum base material is polished with sandpaper until the surface is smooth and flat, and put into absolute ethanol or ethanol solution for degreasing and degreasing treatment, then dried and set aside.
[0040] (2) Nitriding treatment: place the pretreated metal molybdenum substrate in an atmosphere furnace, and raise the temperature to 1000°C at a rate of 10°C / min under a 99.99% high-purity nitrogen atmosphere with a flow rate of 200mL / min. After heat preservation at 1000°C for 10 hours, it was cooled to room temperature with the furnace, then taken out, cleaned with ultrasonic waves for 5-10 minutes, and dried to obtain a semi-finished product A with a molybdenum nitride coating on the molybdenum surface.
[0041] (3) Silicification treatment: Put the semi-finished product A into a high-purity alumina crucible equipped with a uniformly mixed siliconization agent, which contains silicon powder, NaF, Al ...
PUM
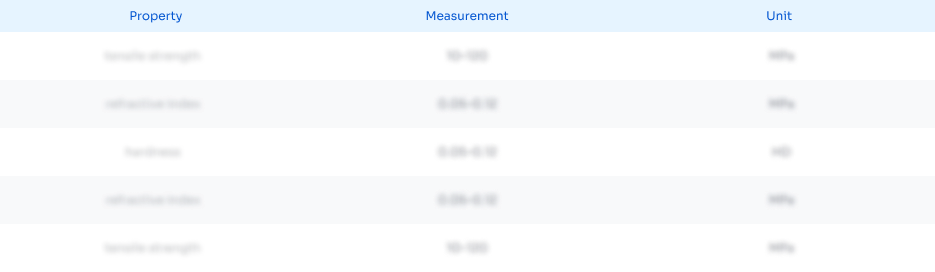
Abstract
Description
Claims
Application Information

- R&D
- Intellectual Property
- Life Sciences
- Materials
- Tech Scout
- Unparalleled Data Quality
- Higher Quality Content
- 60% Fewer Hallucinations
Browse by: Latest US Patents, China's latest patents, Technical Efficacy Thesaurus, Application Domain, Technology Topic, Popular Technical Reports.
© 2025 PatSnap. All rights reserved.Legal|Privacy policy|Modern Slavery Act Transparency Statement|Sitemap|About US| Contact US: help@patsnap.com