Flame retardant polyurethane material as well as preparation method and application thereof
A polyurethane material, flame retardant technology, applied in the field of polymer material modification, can solve the problems of low tensile strength, air pollution, poor wind resistance, etc., and achieves good thermal insulation, sound insulation, environmental protection, flame retardant and sound insulation performance , Good waterproof and compact effect
- Summary
- Abstract
- Description
- Claims
- Application Information
AI Technical Summary
Problems solved by technology
Method used
Image
Examples
Embodiment 1
[0042] 100 parts of sorbitan (hydroxyl value 500), polyester P 3152 Put 20 parts and 125 parts of polyphenyl polymethylene polyisocyanate (PAPI) into a reaction kettle with a stirrer and heat and stir for 8 minutes at a temperature of 120°C to generate a prepolymer containing free isocyanate, and then send it to the storage groove.
[0043] Then add 10 parts of heat and sound insulation additive diatomite, 6 parts of ammonium polyphosphate coated with epoxy resin, 4 parts of melamine cyanurate, 3 parts of antimony trioxide, and 2 parts of compatibilizer maleic anhydride grafted polypropylene. Pour into the reaction kettle and stir for 10 minutes, then put into another storage tank for later use;
[0044] The above-mentioned processed mixture is sent to the mixer with 6.5 parts of foaming agent AC at the same time by two metering pumps respectively, and the remaining components (1 part of triethanolamine, 0.5 part of dibutyltin dilaurate, foam stabilizer silicone oil L-580 1....
Embodiment 2
[0046] 100 parts of sorbitan (hydroxyl value 500), polyester P 3152 Put 22 parts and 122 parts of polyphenyl polymethylene polyisocyanate (PAPI) into a reaction kettle with a stirrer and heat and stir for 8 minutes at a temperature of 120°C to generate a prepolymer containing free isocyanate, and then send it to the storage groove.
[0047] Add 10 parts of heat and sound insulation additive diatomite, 6.4 parts of epoxy resin-coated ammonium polyphosphate, 4.4 parts of melamine cyanurate, and 2 parts of maleic anhydride grafted polypropylene into the reaction kettle and stir for 8 minutes. into another storage tank for use;
[0048] The above-mentioned treated mixture was sent to the mixer with 10.2 parts of foaming agent AC at the same time by two metering pumps, and the remaining components (1.3 parts of triethanolamine, 1.8 parts of foam stabilizer silicone oil L-580) were used in sequence Another metering pump is sent into the mixer, and after vigorous stirring for 10 mi...
Embodiment 3
[0050] 100 parts of sorbitan (hydroxyl value 500), polyester P 3152 Put 25 parts and 125 parts of polyphenyl polymethylene polyisocyanate (PAPI) into a reactor with a stirrer and heat and stir for 6 minutes at a temperature of 120°C to generate a prepolymer containing free isocyanate, and then send it to the storage groove.
[0051] Then add 12 parts of diatomite, 9.6 parts of epoxy resin-coated ammonium polyphosphate, 7.5 parts of melamine cyanurate, 3 parts of antimony trioxide, and 7 parts of maleic anhydride grafted polypropylene to the reaction. Stir in the kettle for 10 minutes, put into another storage tank for use;
[0052] The above-mentioned treated mixture was sent to the mixer with 10.8 parts of foaming agent AC at the same time by two metering pumps, and the remaining components (1.2 parts of triethanolamine, 1.8 parts of foam stabilizer silicone oil L-580) were used in sequence Another metering pump is sent into the mixer, and after vigorous stirring for 15 min...
PUM
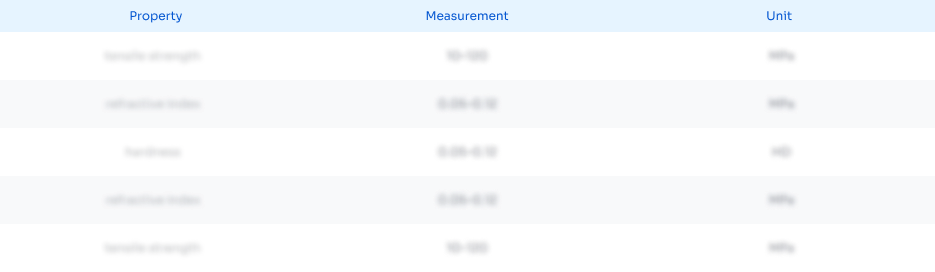
Abstract
Description
Claims
Application Information

- R&D
- Intellectual Property
- Life Sciences
- Materials
- Tech Scout
- Unparalleled Data Quality
- Higher Quality Content
- 60% Fewer Hallucinations
Browse by: Latest US Patents, China's latest patents, Technical Efficacy Thesaurus, Application Domain, Technology Topic, Popular Technical Reports.
© 2025 PatSnap. All rights reserved.Legal|Privacy policy|Modern Slavery Act Transparency Statement|Sitemap|About US| Contact US: help@patsnap.com