Method for preparing high-comfortable composite functional polyester fiber
A composite function, polyester fiber technology, applied in the direction of fiber chemical characteristics, single-component polyester rayon, rayon manufacturing, etc., can solve the problems of easy pilling, easy to generate static electricity, difficult to dye, etc.
- Summary
- Abstract
- Description
- Claims
- Application Information
AI Technical Summary
Problems solved by technology
Method used
Image
Examples
Embodiment 1
[0039] This embodiment provides a method for preparing a high-comfort composite functional polyester chip, which includes the following steps:
[0040] (1), Primary esterification reaction section: Take 18kg of purified terephthalic acid (PTA), 7.5kg of ethylene glycol (EG) and 225g of 1,4-cyclohexanedicarboxylic acid, add 70 liters of polyester experimental equipment, and stir After uniformity, start to raise the temperature and pressurize to 0.3Mpa to carry out esterification. The esterification temperature is controlled at 255°C to 260°C. After the esterification is completed, return to normal pressure and end the reaction.
[0041] (2) Secondary esterification reaction section: After the primary esterification is completed, ethylene glycol is first added to lower the temperature of the reactor to 230-235°C, and then 450g of polyethylene glycol with a number average molecular weight of 2500 that has been heated and melted The diol was added into the reactor under the protec...
Embodiment 2
[0044] This embodiment provides a method for preparing a high-comfort composite functional polyester chip, which includes the following steps:
[0045] (1), primary esterification reaction section: take 18kg of purified terephthalic acid (PTA), 7.5kg of ethylene glycol (EG) and 225g of 5-methylisophthalic acid, add 70 liters of polyester experimental equipment, and stir evenly Afterwards, start to raise the temperature and pressurize to 0.3Mpa to carry out esterification. The esterification temperature is controlled at 255°C to 260°C. After the esterification is completed, return to normal pressure and complete the reaction.
[0046] (2) Secondary esterification reaction section: After the primary esterification is completed, ethylene glycol is first added to lower the temperature of the reactor to 230-235°C, and then 450g of polyethylene glycol with a number average molecular weight of 2500 that has been heated and melted The diol was added into the reactor under the protecti...
Embodiment 3
[0049] This embodiment provides a method for preparing a high-comfort composite functional polyester chip, which includes the following steps:
[0050] (1), primary esterification reaction section: get 18kg of purified terephthalic acid (PTA), 7.5kg of ethylene glycol (EG) and 225g of adipic acid, add 70 liters of polyester experimental equipment, after stirring evenly, start to heat up and Pressurize to 0.3Mpa to carry out esterification, and the temperature of esterification is controlled at 255°C to 260°C. After the esterification is completed, return to normal pressure and complete the reaction.
[0051] (2) Secondary esterification reaction section: After the primary esterification is completed, ethylene glycol is first added to lower the temperature of the reactor to 230-235°C, and then 450g of polyethylene glycol with a number average molecular weight of 3000 that has been heated and melted is added The diol was added into the reactor under the protection of nitrogen, a...
PUM
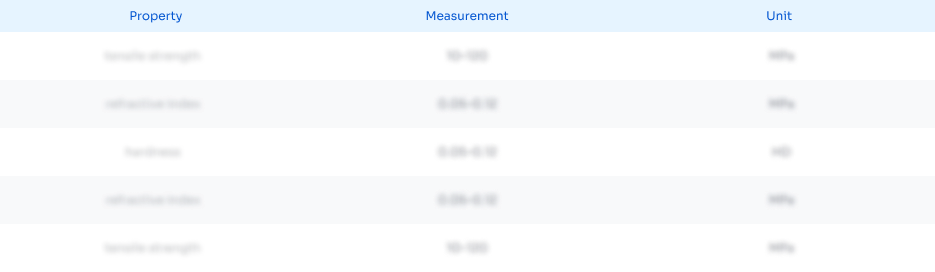
Abstract
Description
Claims
Application Information

- Generate Ideas
- Intellectual Property
- Life Sciences
- Materials
- Tech Scout
- Unparalleled Data Quality
- Higher Quality Content
- 60% Fewer Hallucinations
Browse by: Latest US Patents, China's latest patents, Technical Efficacy Thesaurus, Application Domain, Technology Topic, Popular Technical Reports.
© 2025 PatSnap. All rights reserved.Legal|Privacy policy|Modern Slavery Act Transparency Statement|Sitemap|About US| Contact US: help@patsnap.com