Narrow-hardenability pinion steel and preparation method thereof
A technology of hardenability and gear steel, which is applied in the manufacture of converters and the improvement of process efficiency, etc., can solve the problems of high production cost, and achieve the effects of low production cost, high hardenability and narrow hardenability band at the end
- Summary
- Abstract
- Description
- Claims
- Application Information
AI Technical Summary
Problems solved by technology
Method used
Examples
Embodiment 1
[0035] A narrow hardenability gear steel, which contains the following components in mass percentages:
[0036] C (carbon): 0.20%, Si (silicon): 0.26%, Mn (manganese): 1.02%, P (phosphorus): 0.010%, S (sulfur): 0.008%, Cr (chromium): 1.19%, Ti ( Titanium): 0.06%, B (boron): 0.0045%, W (tungsten): 0.032%, [O]: 11.0×10 -6 , [H]: 1.2×10 -6 , [N]: 40×10 -6 , the rest is Fe (iron) and unavoidable impurities.
[0037] The preparation method of above-mentioned narrow hardenability gear steel, it comprises the following steps:
[0038] 1) Primary smelting of top-bottom compound blowing converter:
[0039] The blast furnace molten iron is desulfurized by Mg which accounts for 20% of the total mass of the molten iron and 80% of the CaO desulfurizer powder spraying method, and then enters the top-bottom composite blowing converter for primary refining; the composition of the molten iron entering the top-bottom composite blowing converter is: C: 4.2%, Si: 0.60%, Mn: 0.48%, P: 0.098%,...
Embodiment 2
[0054] A narrow hardenability gear steel, which contains the following components in mass percentages:
[0055] C: 0.18%, Si: 0.30%, Mn: 0.90%, P: 0.012%, S: 0.010%, Cr: 1.35%, Ti: 0.04%, B: 0.005%, W: 0.025%, [O]: 11.5 ×10 -6 , [H]: 1.4×10 -6 , [N]: 45×10 -6 , and the rest are Fe and unavoidable impurities.
[0056] The preparation method of above-mentioned narrow hardenability gear steel, it comprises the following steps:
[0057] 1) Primary smelting of top-bottom compound blowing converter:
[0058] The blast furnace molten iron is desulfurized by Mg which accounts for 20% of the total mass of the molten iron and 80% of the CaO desulfurizer powder spraying method, and then enters the top-bottom composite blowing converter for primary refining; the composition of the molten iron entering the top-bottom composite blowing converter is: C: 3.8%, Si: 0.50%, Mn: 0.40%, P: 0.010%, S: 0.095%, and the rest are iron and unavoidable impurities. The temperature of molten iron ente...
Embodiment 3
[0072] A narrow hardenability gear steel, which contains the following components in mass percentages:
[0073] C: 0.22%, Si: 0.20%, Mn: 1.15%, P: 0.016%, S: 0.013%, Cr: 1.00%, Ti: 0.08%, B: 0.004%, W: 0.038%, [O]: 10.8 ×10 -6 ,[H]: 1.44×10 -6 , [N]: 35×10-6 , and the rest are iron and unavoidable impurities.
[0074] The preparation method of above-mentioned narrow hardenability gear steel, it comprises the following steps:
[0075] 1) Primary smelting of top-bottom compound blowing converter:
[0076] The blast furnace molten iron is desulfurized by Mg and 80% of the total mass of the molten iron, and then enters the top-bottom compound blowing converter for primary refining; the composition of the molten iron entering the top-bottom compound blowing converter is: C: 4.8%, Si: 0.70%, Mn: 0.60%, P: 0.008%, S: 0.008%, and the rest are iron and unavoidable impurities. The temperature of molten iron entering the converter is 1390°C; Five-hole Laval nozzle is used, the angle...
PUM
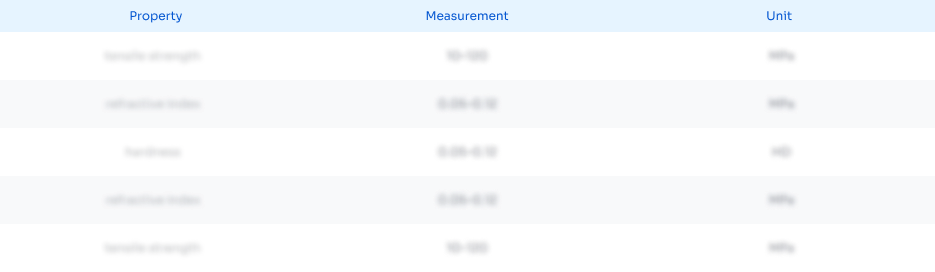
Abstract
Description
Claims
Application Information

- Generate Ideas
- Intellectual Property
- Life Sciences
- Materials
- Tech Scout
- Unparalleled Data Quality
- Higher Quality Content
- 60% Fewer Hallucinations
Browse by: Latest US Patents, China's latest patents, Technical Efficacy Thesaurus, Application Domain, Technology Topic, Popular Technical Reports.
© 2025 PatSnap. All rights reserved.Legal|Privacy policy|Modern Slavery Act Transparency Statement|Sitemap|About US| Contact US: help@patsnap.com